Best Box Stacking Tools 2025
By Qviro · August 7, 2024
Best 10 Box Stacking Tools of 2025:
UNIVERSAL ROBOTS UR20
Rating: 4.6/5 (41 Reviews)
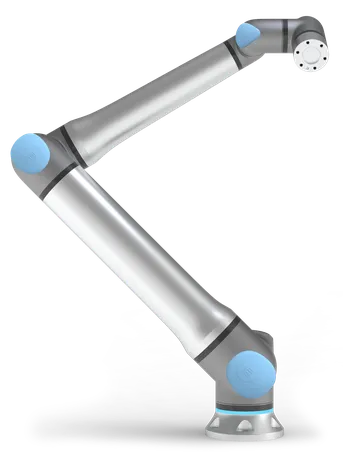
Description: Efficient palletizing robot with 1750 mm reach and 20 kg payload, designed for speed and adaptability.
Price: $57,000.00
Specs: Payload 20kg | Reach 1750mm
Read more about UR20
ABB GoFa 12
Rating: 4.7/5 (9 Reviews)
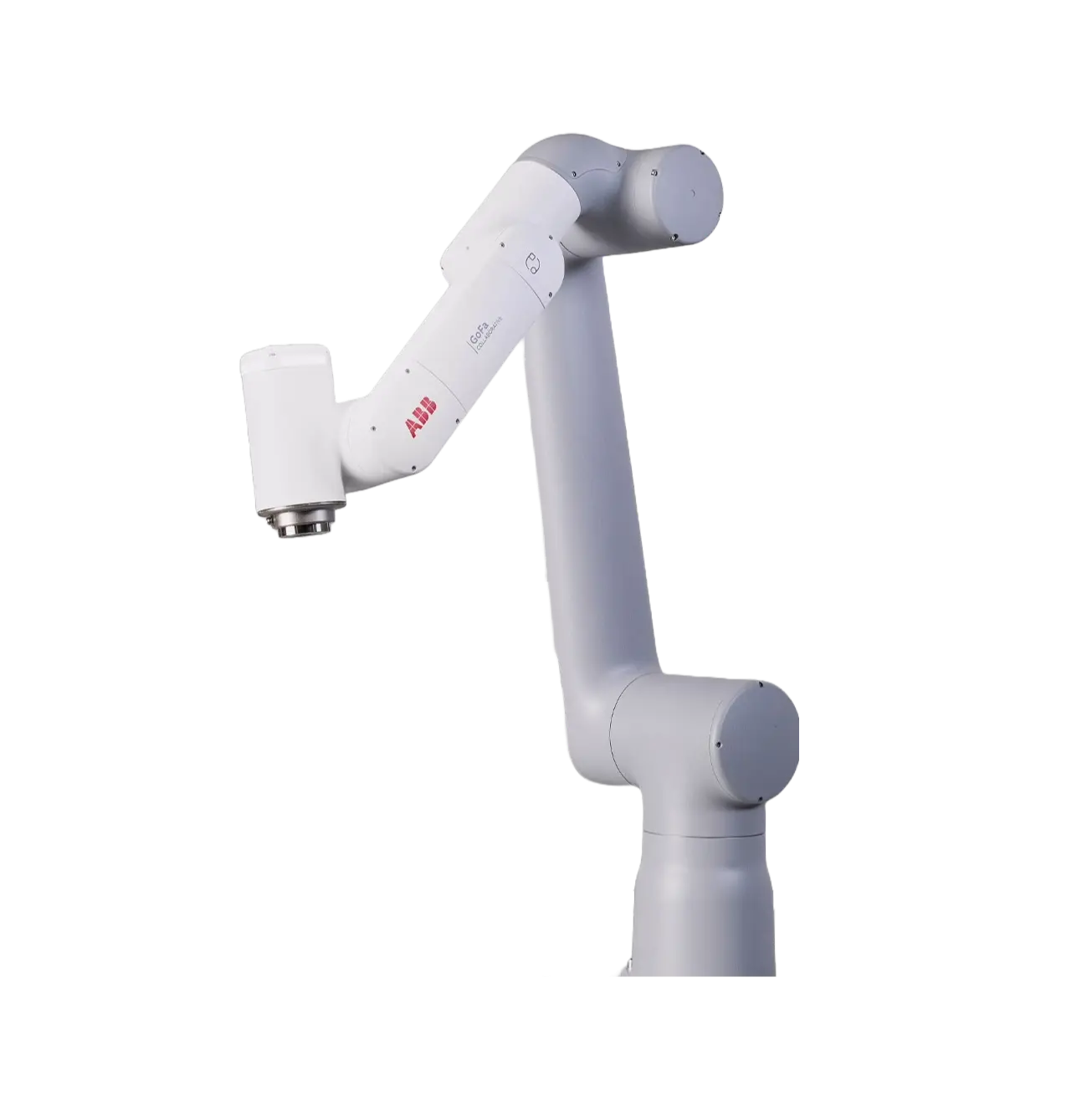
Description: Compact palletizing robot with 950 mm reach and 12 kg payload, ideal for handling small packages.
Specs: Payload 12kg | Reach 950mm
Read more about GoFa 12
Kinova Gen3 (7DoF)
Rating: 4.7/5 (12 Reviews)
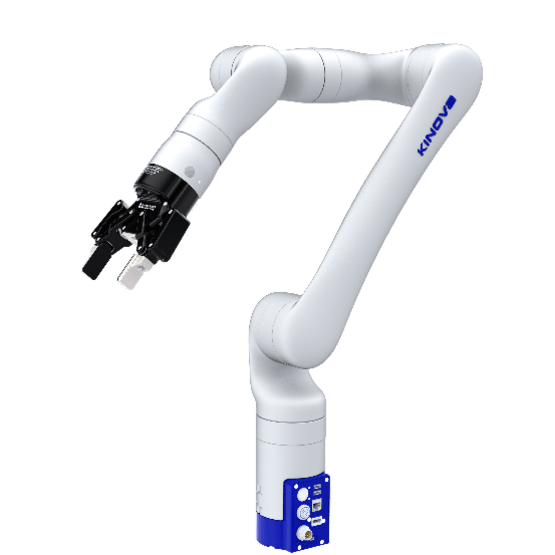
Description: Versatile collaborative robot with 915mm reach, 4kg payload. Suitable for research and light industrial tasks.
Specs: Payload 4kg | Reach 915mm
Read more about Gen3
Yaskawa HC20DTP
Rating: 4.7/5 (10 Reviews)
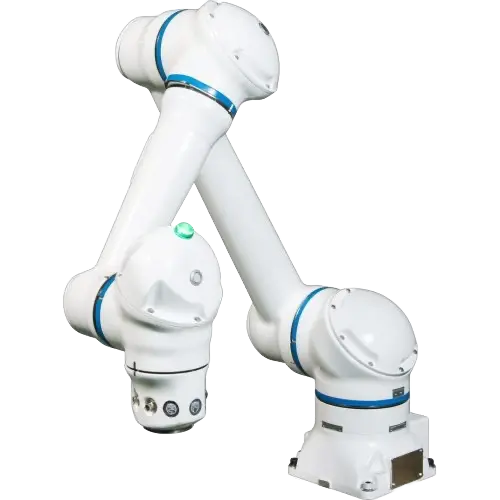
Description: 20 kg payload, 1700 mm reach; ideal for fast, safe palletizing with intuitive hand-guided programming.
Specs: Payload 20kg | Reach 1900mm
Read more about HC20DTP
FANUC CRX-25iA
Rating: 4.8/5 (5 Reviews)
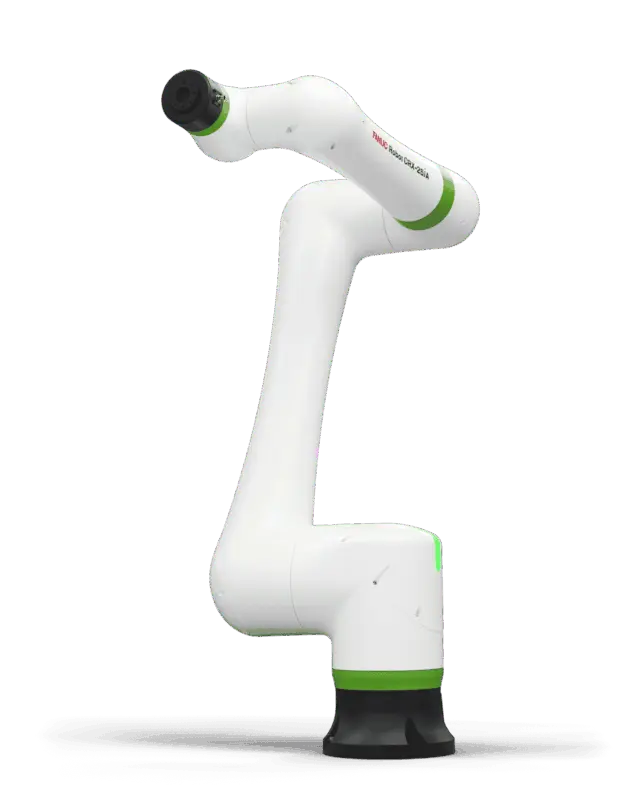
Description: Heavy-duty palletizing robot with 1889 mm reach and 25 kg payload, ideal for robust applications.
Specs: Payload 25kg | Reach 1889mm
Read more about CRX-25iA
Techman TM14
Rating: 4/5 (1 Review)
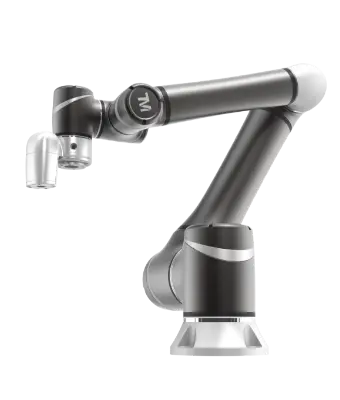
Description: Precision palletizing robot with 1100 mm reach and 14 kg payload, featuring an integrated vision system.
Specs: Payload 14kg | Reach 1100mm
Read more about TM14
AUBO i10
Rating: 4.1/5 (1 Review)
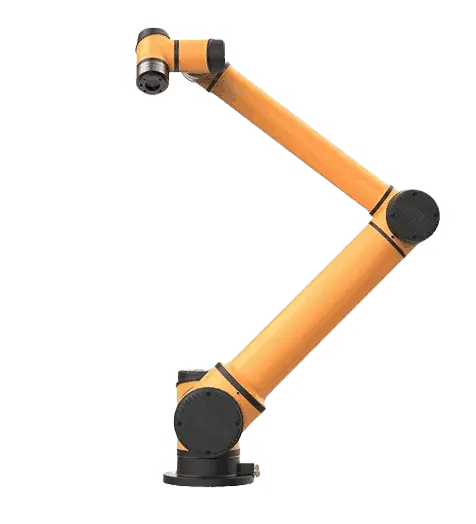
Description: Compact collaborative robot. Ideal for precise and efficient palletizing in light industrial settings. Easy integration and cost-effective operation.
Specs: Payload 10kg | Reach 1350mm
Read more about i10
Doosan H2017
Rating: 4.3/5 (2 Reviews)
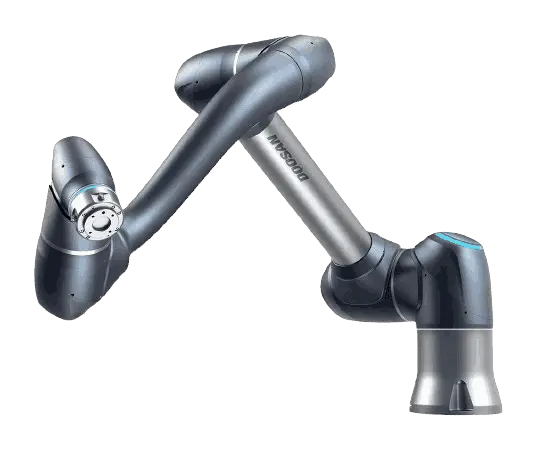
Description: Heavy-duty collaborative robot optimized for high-efficiency palletizing tasks. Features advanced safety systems and intuitive programming for seamless integration.
Specs: Payload 20kg | Reach 1700mm
Read more about H2017
KUKA LBR iiwa 14 R820
Rating: 4.1/5 (3 Reviews)
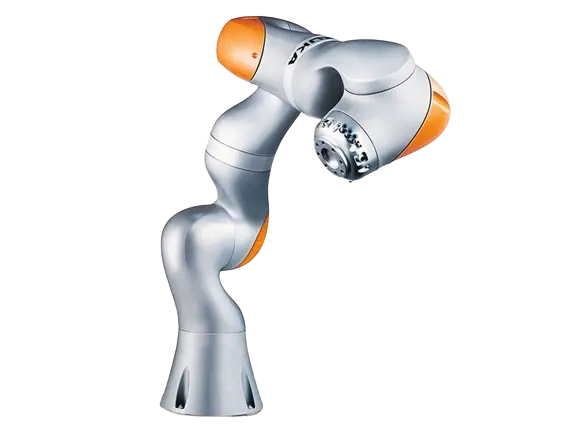
Description: Collaborative robot ideal for precise palletizing. Features sensitive control for safe human-robot collaboration.
Specs: Payload 14kg | Reach 820mm
Read more about LBR iiwa 14 R820
Hanwha HCR12
Rating: 4.1/5 (1 Review)
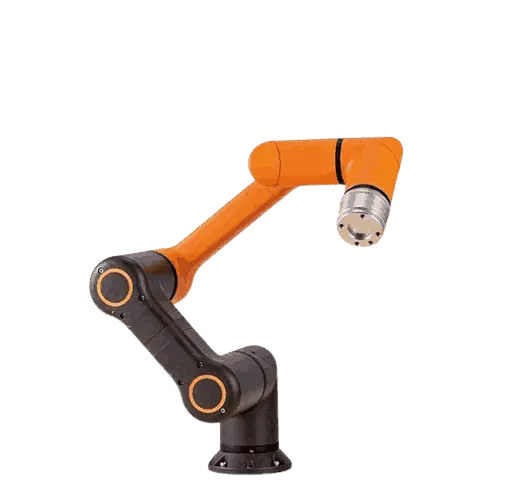
Description: Versatile robot with 1300 mm reach and 12 kg payload, perfect for light palletizing and handling tasks.
Specs: Payload 12kg | Reach 130mm
Read more about the HCR12
Comparing the Main Types of Palletizers:
Features | Industrial Palletizers | Collaborative Palletizers | Conventional Palletizers |
---|---|---|---|
Primary Use | High-speed, heavy-load tasks | Flexible and adaptable operations | Pattern-based stacking |
Key Industries | Food processing, manufacturing | Warehouses, small manufacturing | Uniform product operations |
Operation | Automated, high precision | Human-in-the-loop, safe collaboration | Mechanical systems |
Space Requirement | Compact design | Flexible, minimal barriers | Larger space needed |
Flexibility | Handles high volumes | Easily reprogrammable | Fixed stacking patterns |
Safety | High-speed operation safety | Enhanced with collaboration | Basic mechanical safety |
Cost Details:
Understanding the cost and efficiency of palletizers is important for making informed decisions about your operations. Here’s what you should know:
Initial Investment:
When you invest in a palletizer, you’ll face some upfront costs. Basic systems start at about $50,000. If you need an advanced model, the cost can exceed $300,000. This price includes the robot, software, and any necessary accessories. While this initial cost might seem high, consider the long-term benefits you’ll gain.
Long-Term Savings:
Palletizers help you save money by reducing labor costs. They automate repetitive tasks and work continuously without breaks, which cuts down on overtime and the need for manual labor. Over time, these efficiencies can lead to significant savings, making your investment in palletizers worthwhile.
Selecting the right cobots for your business is important. You need to understand your specific requirements to make the best choice. This is where automation consulting can help. Qviro’s Alina is here to make the selection process easier. Alina offers expert guidance that is tailored to your needs.
Benefits of Box Stacking Automation:
1. Boost Productivity & Throughput:
With automation, you can stack items faster, boosting your productivity. Robots work non-stop, helping you get more done in less time.
2. Cut Labor Costs & Reduce Injuries:
Automation means less manual labor, saving you money and reducing the risk of injuries from heavy lifting or repetitive tasks.
3. Ensure Accuracy & Consistency:
Robots ensure every item is stacked precisely, minimizing errors and keeping your products safe. This consistent quality enhances customer satisfaction.
4. Optimize Warehouse Space:
Automated stacking maximizes your warehouse space by stacking items efficiently, allowing you to store more in the same area.
5. Enhance Adaptability to Demand:
Automation gives you flexibility to handle different items and production needs easily, ensuring your operation stays efficient even as things change.
Steps to Program Your Automatic Box Stacker:
Steps | What To Do: |
---|---|
1. Choose Your Stack Style | |
2. Show the Robot the Ropes | |
3. Prioritize Safety | |
4. Perfect the Pace |
Why Robots for Palletizing?
Speed:
Choosing robots for palletizing makes your work faster and more precise. They work non-stop, ensuring consistent productivity.
Safety:
Robots reduce the risk of injuries from heavy lifting and repetitive tasks, making your workplace safer for you and your team.
Accuracy:
Robots excel at placing items exactly where they need to be on the pallet, helping you use space more efficiently and reducing errors.
Cost-Effectiveness:
By automating palletizing with robots, you save time and money. This efficiency means lower labor costs and optimized storage.
Flexibility:
As your business grows, robots can adapt to new tasks and increased demand, ensuring you can keep up without sacrificing efficiency.
Types of Grippers for Fragile or Irregular Pallet Items:
Gripper Type | Description |
---|---|
Vacuum Grippers | Soft Yet Strong: Imagine a tool that can pick up a sheet of glass or a thin plastic without leaving a mark. That’s what vacuum grippers do. They suck onto surfaces gently, moving your delicate items without any pressure that could cause damage. |
Mechanical Grippers | Grab Anything Firmly: Need to lift something heavy or with an awkward shape? Mechanical grippers are like strong hands that can adjust to hold almost any item securely, no matter its shape or size. They’re your go-to for the tough stuff. |
Soft-Touch Grippers | Handle with Care: For items that need an extra soft touch, soft-touch grippers are here. They’re like cushioned fingers, gentle enough for the most sensitive items but with a precise grip for complex shapes. |
Key Considerations When Designing a Palletizing Layout:
Analysis of Product Dimensions & Weight:
Before you design your layout, check the size and weight of your products. Make sure your system can handle these effectively to avoid any issues.
Evaluation of Throughput Rates and Production Schedules:
Look at your production schedule. Determine how quickly items need to move through your system. This helps you plan for busy times and avoid slowdowns.
Assessment of Floor Space and Warehouse Layout:
Check your available space and current warehouse layout. Ensure your palletizing system fits well and doesn’t interfere with other operations.
Integration with Existing Conveyor Systems and Equipment:
Ensure your new system works smoothly with your current equipment. This will help you avoid delays and improve efficiency.
Incorporation of Safety Measures and Ergonomic Considerations:
Prioritize safety. Add features like barriers and emergency stops to protect your workers. Consider ergonomic factors to make tasks easier and more comfortable for your team.
End-of-Line Automation: Simplifying Final Processes for Efficiency
End-of-line automation means using robots and tech at the end of your production or packaging lines.
What is it?: This is where your products get packaged, labeled, and ready to be shipped.
Why use it?: You use end-of-line automation to make these final processes faster, more accurate, and consistent.
What it includes: This includes tasks like stacking boxes, packing cases, sealing cartons, putting on labels, and checking quality.
What you get: With end-of-line automation, you save on labor costs, reduce mistakes, and boost how much you can make, making your business more competitive.
Industries That Use Palletizing Robots:
Industry | Usage |
---|---|
Food and Beverage | You’ll find palletizing robots stacking and packing everything from canned goods to bottled drinks, ensuring faster production rates. |
Pharmaceuticals | These robots handle delicate medicines and vaccines, maintaining precision and cleanliness during packaging. |
Consumer Goods | Palletizing robots help in packing personal care products like soaps and shampoos, boosting efficiency. |
Chemicals | They manage hazardous materials safely, stacking heavy chemical containers without spills or accidents. |
Automotive | Used for organizing parts and final products, these robots streamline the assembly line and storage processes. |
Electronics | They precisely stack fragile electronics, from smartphones to TVs, protecting them from damage. |
Construction | Palletizing robots handle heavy building materials like bricks and tiles, reducing labor costs. |
Agriculture | These robots speed up the packaging of seeds, grains, and fertilizers, enhancing throughput. |
Metal Manufacturing | Handling heavy metal products and scraps, they improve safety and organization in metal processing. |
Logistics & Warehousing | They optimize space by efficiently stacking various products, crucial for inventory management. |