SSI Schäfer WEASEL Alternatives & Competitors
Ranked Nr. 77 of 182 Mobile Robots
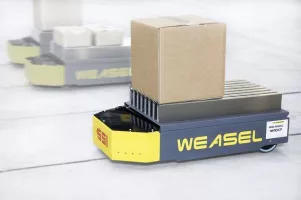
Top 10 WEASEL Alternatives
- WObit MOBOT® AGV FlatRunner MW
- Jungheinrich AG ERE 225a
- Kivnon K03 Twister
- Kivnon K05 Twister
- STÄUBLI PF100
- Beewatec BARY CM-100
- GESSbot GB350
- TÜNKERS TACT TOS
- Linde Material Handling C-MATIC
- Wellwit Robotics W500SL Under Ride Lifting AGV
- STILL Gmbh AXH 10

WObit MOBOT® AGV FlatRunner MW
Payload 1800kg | Product mass 750kgMOBOT® AGV FlatRunner MW (Automated Guided Vehicle) is a mobile robot for the transport of goods, in which movement is executed automatically. Its main task is to autonomously transport goods between selected points. Navigation The robot can be navigated using a laser mapping system (LMS), a free navigation system using a natural object such as walls for navigation.
Unlimited mobility The robot drive system is equipped with Mecanum wheels, which allows movement in any direction and execute 360-degree rotations. A wheel consists of several rollers that are each aligned at an angle of 45 degrees relative to the axle. This excellent maneuverability shortens throughput times and reduces idle times in the manufacturing process. Along with safety scanners and laser navigation, this solution vastly increase possibilities of robot application and allows safe and precise movement even in the tightest spaces.
Charging option The robot is equipped with 2 batteries in cassettes, which enable quick swapping. it can also, be charged using a wire charging station, optionally there is a possibility of use an automatic charging station.

Jungheinrich AG ERE 225a
The Jungheinrich ERE 225a is a reliable and versatile Automated Guided Vehicle (AGV) that excels in repetitive transport tasks. Designed specifically for multi-pallet transport, the ERE 225a offers increased efficiency in your transport processes. Its standout features and capabilities make it a valuable asset for industrial automation.
The AGV is equipped with long forks, allowing it to handle multiple pallets simultaneously. This capability significantly enhances productivity by reducing the number of trips required for transporting goods. Whether it's moving pallets within a warehouse or transferring them between different areas, the ERE 225a streamlines the material handling process, saving time and labor.
To ensure consistent performance over long distances, the ERE 225a incorporates a 2.8-kW 3-phase AC motor. This powerful motor delivers reliable and efficient operation, enabling the AGV to handle demanding transport tasks without compromising on performance. This capability is particularly beneficial in applications where the AGV needs to cover significant distances within a facility.
Safety is a top priority in industrial automation, and the ERE 225a is designed with robustness and safety features in mind. The AGV features a sturdy steel frame and an enclosed structure, enhancing its durability and providing protection for both the vehicle and the goods being transported. Additionally, the AGV is equipped with standard personal protection scanners, ensuring safe operation in mixed environments. These scanners detect obstacles in the travel route, whether it's in the drive direction or during cornering, further enhancing safety during operation.
In terms of navigation, the ERE 225a utilizes laser navigation technology. It can navigate by detecting either reflectors placed along the travel route or a combination of reflectors and environmental features. This flexible navigation system allows the AGV to adapt to different environments and layouts, providing reliable and precise movement throughout the facility.
The ERE 225a offers seamless integration into existing IT structures, making it easy to incorporate into your automation setup. It can be integrated as part of a larger system or operated as a standalone AGV solution. Additionally, the AGV is compatible with various software systems, allowing for smooth communication and coordination with other automated equipment or warehouse management systems. This compatibility enhances the overall efficiency and productivity of the AGV within your existing factory structures or new builds.
While not specifically mentioned in the provided information, it's worth noting that the ERE 225a may offer specialized specifications that make it a unique option for industrial automation. For instance, it might have a tolerance for extreme temperatures, enabling it to operate reliably in environments with hot or cold conditions. This capability expands its applicability to industries such as food and beverage, pharmaceuticals, or cold storage facilities.
In summary, the Jungheinrich ERE 225a AGV is a reliable and versatile solution for repetitive transport tasks. With its long forks, powerful motor, sturdy construction, and safety systems, it enhances efficiency and safety in material handling processes. The AGV's laser navigation system, compatibility with software systems, and ease of integration make it a flexible choice for industrial automation.

Kivnon K03 Twister
The Kivnon K03 Twister is an advanced AGV/AMR (Automated Guided Vehicle/Autonomous Mobile Robot) model specifically designed for automating the transport of medium loads in highly specific processes and work environments where space is limited. Its standout feature is its ability to perform a 360-degree rotational movement on its own axis, allowing for greater flexibility of movement and minimizing the time required for operations.
With an on-board load capacity of up to 200kg, the K03 Twister is capable of handling various types of loads. It features a rotational lift table that securely lifts and transports tables, trolleys, and KLT's, providing efficient and reliable material handling solutions.
The K03 Twister offers different guidance options, including magnetic guidance or mapping navigation. This allows the robot to navigate and operate accurately within its environment, ensuring precise movement and positioning. Additionally, it can be adapted to connect with fleet management systems, including those based on VDA 5050, enhancing its integration capabilities within larger automation setups.
One of the notable capabilities of the K03 Twister is its high precision in making stops with full accuracy. This ensures precise positioning when loading and unloading materials, contributing to efficient and error-free operations.
In terms of dimensions, the K03 Twister is compact, measuring 700mm in length, 500mm in width, and 280mm in height. This compact form factor enables it to navigate through narrow spaces and operate in environments with limited room for maneuverability.
The K03 Twister is equipped with a lithium battery that supports online charging through an integrated circuit. This allows for continuous operation without the need for frequent battery replacements or downtime.
To ensure safety, the K03 Twister is equipped with a laser scanner, a safety PLC (Programmable Logic Controller), and LED signaling. These safety measures help detect obstacles, prevent collisions, and alert operators to the robot's status and any potential errors.
With its unique features, the Kivnon K03 Twister offers a specialized solution for industrial automation, particularly in environments where space is limited and precise movement is crucial. Its ability to rotate on its own axis, high load capacity, adaptability to different guidance systems, and compatibility with fleet management systems make it a versatile and efficient option for various applications in industries such as manufacturing, logistics, and warehousing.

Kivnon K05 Twister
The Kivnon K05 Twister is a small and versatile AGV/AMR (Automated Guided Vehicle/Autonomous Mobile Robot) designed specifically for automating the transport of medium loads in highly specific processes and work environments where space is limited. It stands out with its ability to perform a 360-degree rotational movement on its own axis, allowing for exceptional maneuverability and precise positioning.
With an on-board load capacity of up to 450kg and a towing capacity of up to 1,000kg on a wheeled trolley, the K05 Twister is capable of handling various types of loads. It offers different coupling systems, including a retractable pin, lift table, roller conveyor, and even the option to use it as a workbench. This adaptability makes it a versatile solution for a wide range of industrial automation applications.
The K05 Twister features magnetic guidance navigation, which ensures accurate and reliable movement within its operating environment. It can be easily integrated with fleet management systems, including those based on VDA 5050, allowing for seamless coordination and optimization within larger automation setups.
Precision is a key capability of the K05 Twister, enabling it to make precise stops with full accuracy. This ensures efficient and error-free material handling operations, improving productivity and reducing downtime.
In terms of dimensions, the K05 Twister is compact, measuring 800mm in length, 800mm in width, and 280mm in height. This compact form factor allows it to operate in tight spaces and navigate through narrow aisles with ease.
The K05 Twister is powered by either AGM or lithium batteries, and it supports online charging through an integrated circuit.This enables continuous operation without the need for frequent battery replacements, ensuring uninterrupted productivity.
Safety is a priority for the K05 Twister, as it is equipped with a laser scanner and a safety PLC (Programmable Logic Controller) to detect obstacles, prevent collisions, and ensure the well-being of operators and other equipment in its vicinity.
With its compact size, versatile coupling options, precise maneuverability, and compatibility with fleet management systems, the Kivnon K05 Twister offers a unique solution for industrial automation in confined spaces. Its high load capacity, adaptability, and advanced navigation capabilities make it an ideal choice for various applications in industries such as manufacturing, logistics, and warehousing.

STÄUBLI PF100
Stäubli's PF100 is part of their premium AGV (Automated Guided Vehicle) platform series, which has been a trusted choice for manufacturing automation over the last two decades. The PF100, designed for high payload applications, stands out with its impressive capability to transport loads of up to 6 tons. What sets it apart is its omni-directional motion, offering superior maneuverability on the factory floor. Additionally, it boasts high positioning precision, with an accuracy of 5 mm, ensuring that it can handle tasks demanding utmost precision.
One of the unique aspects of the PF100 is its adaptability to both indoor and outdoor environments, providing end-to-end solutions for various industries. This flexibility is crucial for applications where the AGV may need to transition between different working conditions. Furthermore, the PF100 features laser navigation technology for precise and reliable movement, ensuring efficiency and safety in its operations.
The PF100 finds applications in diverse industries, from automotive press shops and assembly lines to e-battery manufacturing, heavy metal industries, and even the semiconductor sector with a cleanroom version. Its ability to handle sensitive and high-precision tasks in demanding environments makes it a valuable asset in industrial intralogistics, railway assembly lines, wind power, and the paper industry. The Stäubli PF100 AGV offers a versatile and robust solution for a wide range of automation needs, particularly those requiring agility, precision, and high payload capabilities.

Beewatec BARY CM-100
Payload 100kgBeeWaTec's BARY CM-100 is an autonomous mobile robot (AMR) designed to revolutionize intralogistics. The CM-100 can be used for in-plant transport, material distribution, automated material supply to workstations, and storage in a warehouse system, eliminating walking distances and improving production and logistics. With 24/7 availability and process stability, the CM-100 ensures efficient and demand-oriented supply.
Controlling the BARY CM-100 is simple and automated, with material requirements in production or logistics triggered by a push button or sensor. The Order Management System (OMS) generates transport jobs based on the signal input, which is then transferred to the fleet management system. The fleet management system plans the robot's routes and sends a transport job to the AMR via WLAN.
The BARY CM-100 navigates freely and autonomously using sophisticated algorithms, calculating the path of least resistance in real-time based on environmental data. The integrated safety laser scanner ensures the safety of employees while detecting obstacles and adjusting the route.
BeeWaTec offers four different navigation types for the AMRs, depending on the operating environment and system requirements. With positioning accuracy of +/- 10mm and even higher positioning accuracy of up to +/- 5 mm, the BARY CM-100 provides maximum efficiency in the allocation of goods at all times. BeeWaTec's AMRs are designed to optimize intralogistics and enhance the overall productivity of your business.
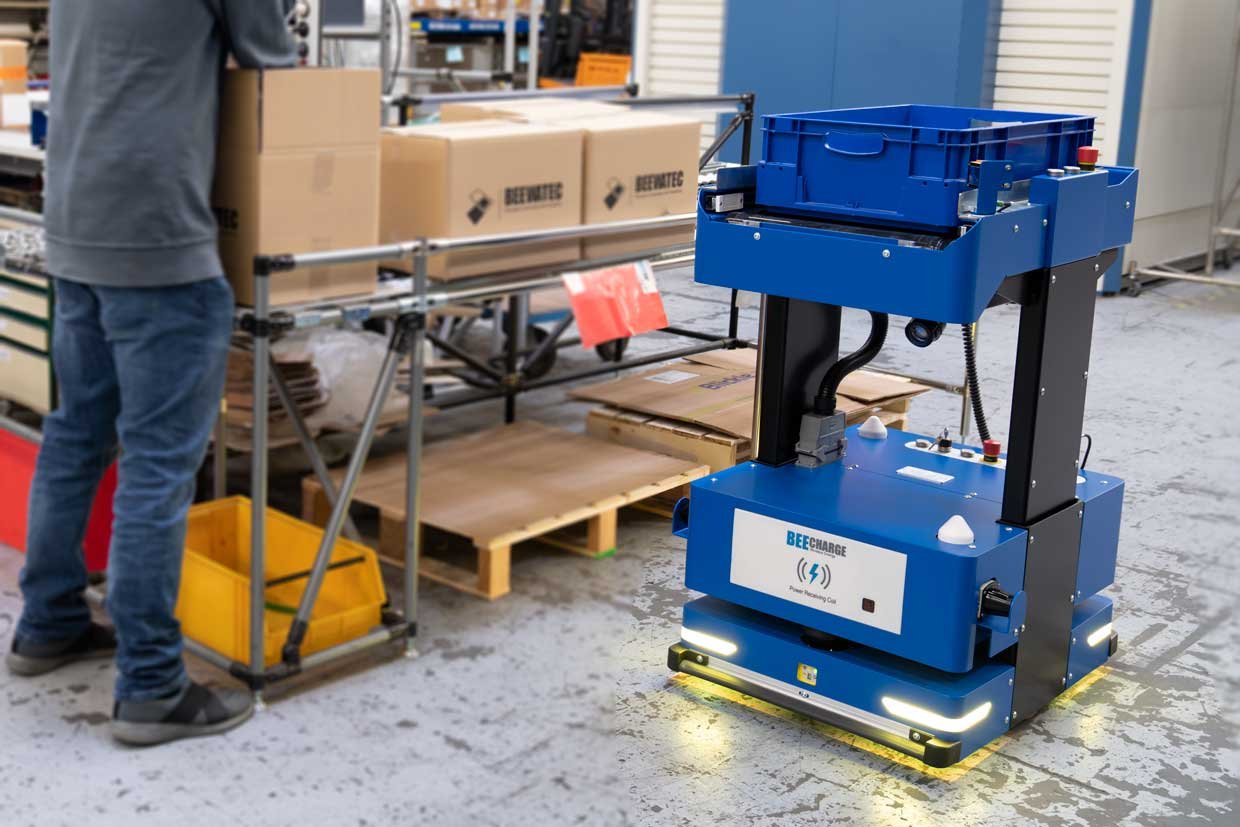
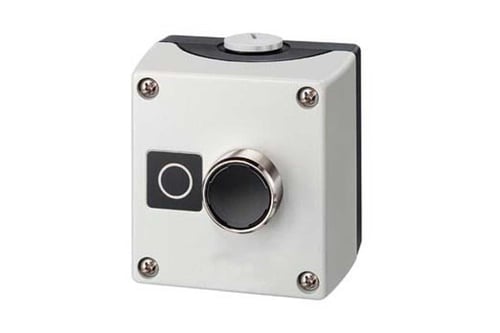
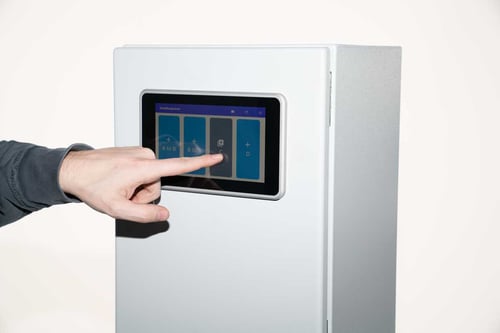
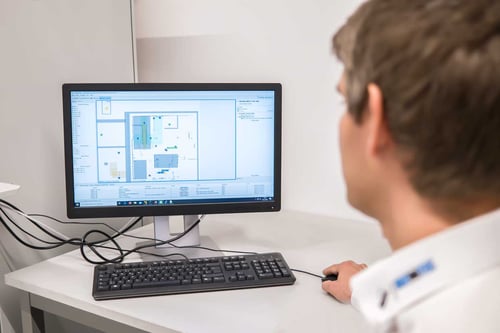
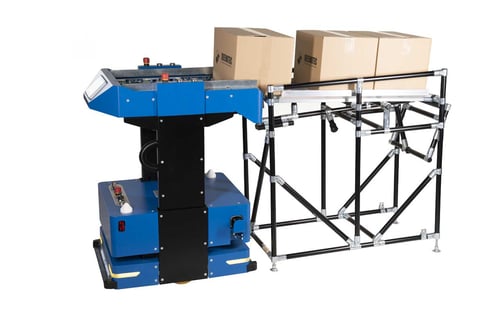
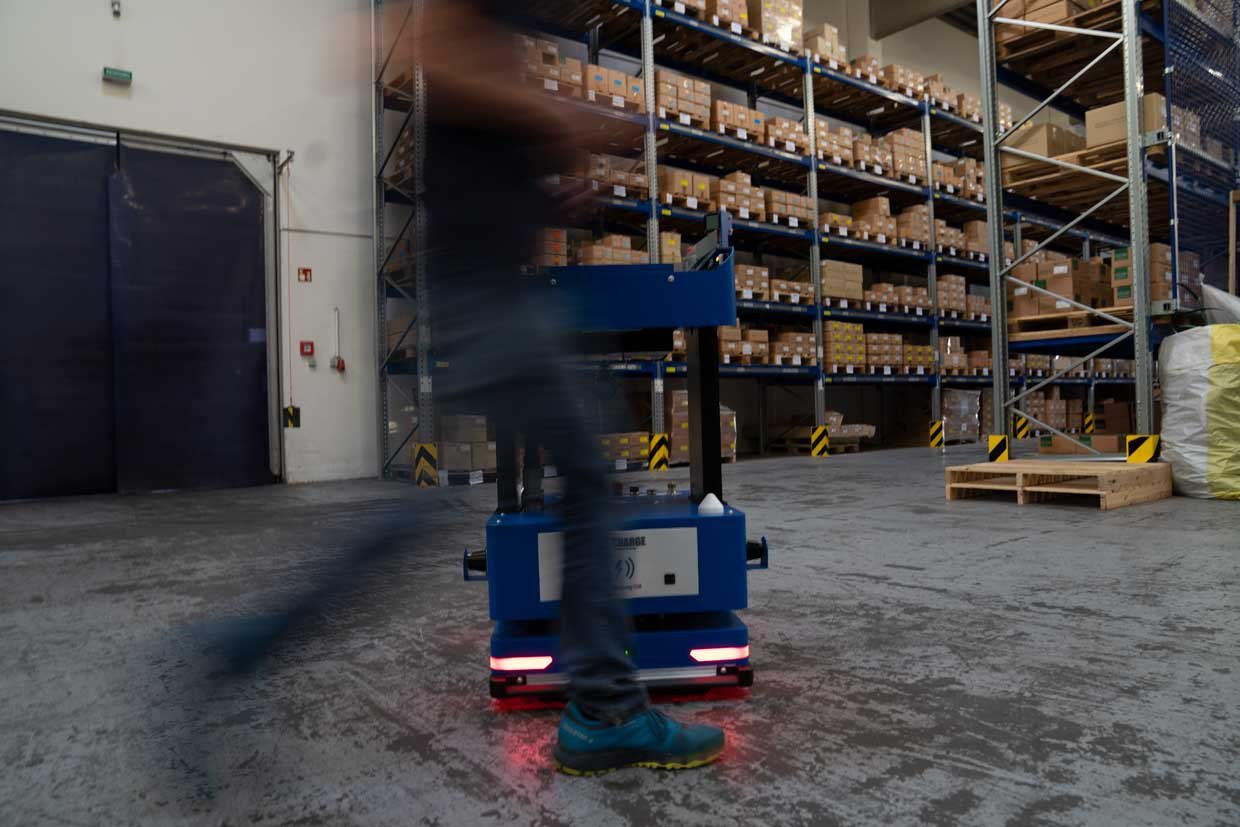

GESSbot GB350
AGV | Payload 350kg | Product mass 150kgThe Gb350 is an automatically guided vehicle (AGV) for quick and cost-efficient automation of your internal transport processes. The Gb350 has a payload of 350kg.
No expensive extras and auxiliary systems, such as magnetic tracks, induction loops or additional safety systems are required. The AGV easily integrates into your existing production and logistics structures.
Autonomous movement
The robot moves autonomously within your company. Thanks to the fusion of various sensor systems, the Gb350 maintains an overview of everything within a radius of 20 m.
Using the Social Navigation System (SNS), it reacts to dynamic changes and always choses the optimum route. People and machines work in perfect harmony thanks to this collaborative behaviour.
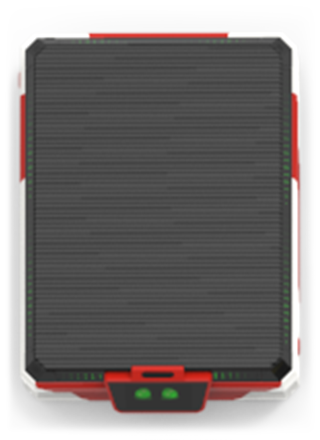
GESSbot Charge System
The charging process is fully automated
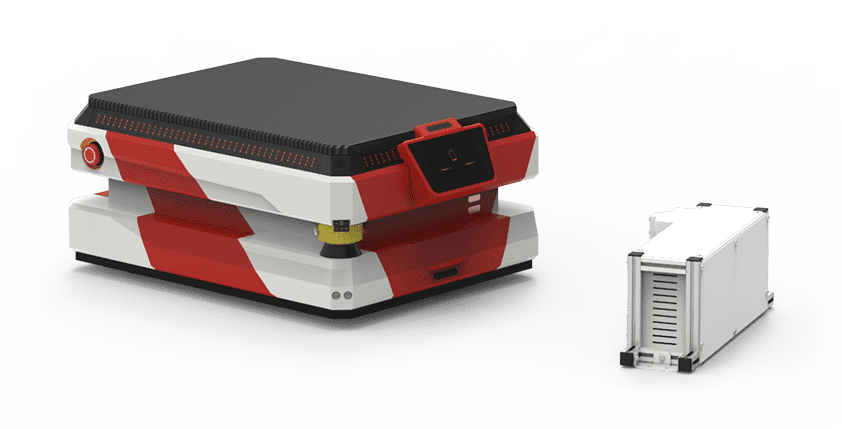
Fall protection thanks to step and cavity recognition
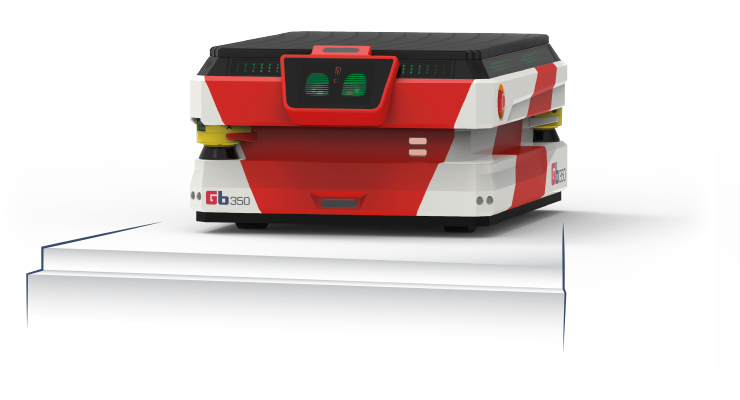
Overload-proof and with integrated scale
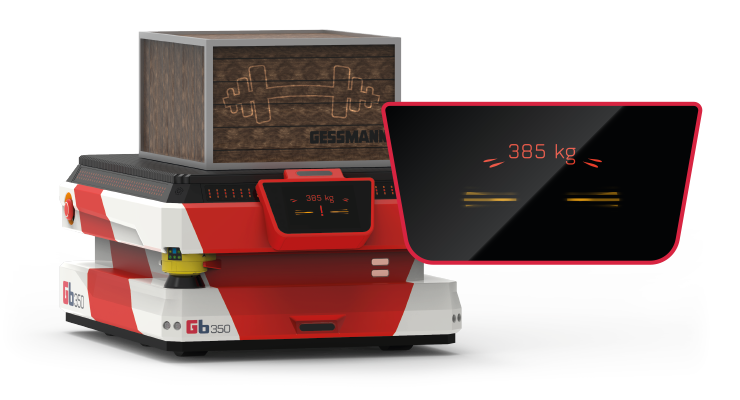
Great audio-visual features
Thanks to the GESSMANN Blackpanel System and an integrated sound module, we underline the actions and movements of the robot visually and acoustically. The latest energy-saving LED technology is used to do this.
Easy to operate
User-friendly, configurable interface
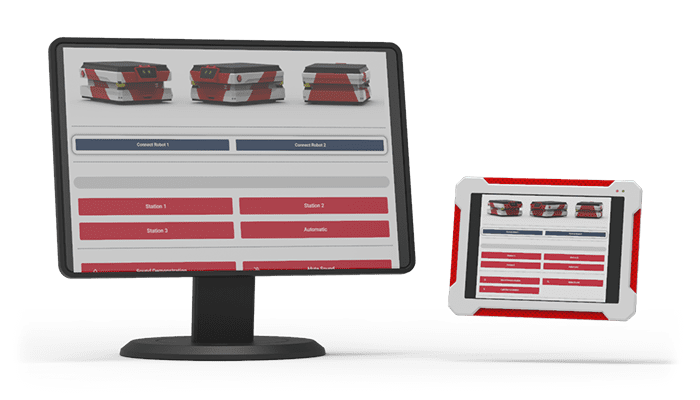
Structures with industry interfaces
Standard structures and customer-specific solutions can be provided. Those are connected directly to the Gb350 and thus form a unit.

TÜNKERS TACT TOS
AGV | Payload 1000kg | Product mass 200kgThe TÜNKERS TACT TOS is one of the most modular vehicles in the range. Use of the TÜNKERS “OneScrew” technology enables individual construction according to customer requirements. The basic frame of the system is based on an octagonal profile with an offset hole pattern to provide a form fit. The connections are based on the standard TÜNKERS round tube components and are force-locked together. An extension with clamping technology enables easy fixing of components on the AGV.

Linde Material Handling C-MATIC
AMR | Payload 600-1500 kgThe Linde Material Handling C-MATIC is a state-of-the-art autonomous truck that guarantees maximum safety, handling efficiency, and serviceability. Its safety features include a laser scanner that detects moving or stationary obstacles in real-time, allowing the truck to adjust its speed or remain stationary until the obstruction is cleared. Additionally, the C-MATIC is equipped with a robust all-round collision protection system and emergency stop switches on all four sides. These safety features ensure the highest possible levels of safety for people and trucks.
The C-MATIC uses QR codes affixed to the hall floor along transport routes to navigate, with each QR code having a unique ID and saved as reference points on a digital map. The software calculates the optimal route for each transport order, allowing the truck to efficiently and autonomously handle material flow. The trolleys are also equipped with QR codes, which makes it possible to identify the goods to be transported, assign storage locations, and position the load carrier. The C-MATIC's optional autonomous charging station allows for automated charging of batteries, ensuring the truck is always fully charged and ready for use.
The C-MATIC’s robust technology ensures reduced service and lifecycle costs, with long maintenance intervals and easily accessible main components that allow for efficient maintenance work. This design-to-service principle also contributes to the truck’s high operational availability, while all the truck data can be read out via a cable connection for fault analysis. In summary, the Linde Material Handling C-MATIC is a reliable and efficient autonomous truck that maximizes safety, handling, and serviceability, making it the ideal solution for material handling in a range of applications.

Wellwit Robotics W500SL Under Ride Lifting AGV
AGV | Payload 500kg | Product mass 220kgThe Wellwit Robotics W500SL Under Ride Lifting AGV is a highly advanced autonomous guided vehicle designed for material handling applications in manufacturing and logistics industries. This AGV features the latest LiDAR SLAM navigation technology, which enables the vehicle to navigate and operate autonomously in complex environments. This technology uses lasers to map and create a 3D image of the AGV's surroundings, allowing it to avoid obstacles and navigate through tight spaces with ease. The LiDAR SLAM navigation system also allows for real-time localization and mapping, ensuring the AGV can quickly adapt to changes in its environment.
One of the key features of the Wellwit Robotics W500SL Under Ride Lifting AGV is its impressive 500 kg payload capacity. This makes it an ideal solution for material handling tasks that require heavy lifting and transport, such as moving large crates or pallets of goods. The AGV is equipped with a high-strength lift mechanism that can easily handle heavy loads, and its compact size and maneuverability make it ideal for use in tight spaces such as factory floors or warehouses.
In addition to its impressive payload capacity, the Wellwit Robotics W500SL Under Ride Lifting AGV also offers a high level of safety and reliability. The AGV is designed with multiple safety features, including a laser safety scanner that ensures the AGV can detect and avoid obstacles in its path. The AGV also features a robust collision avoidance system that can detect and respond to potential collisions, ensuring that the AGV can safely navigate around other vehicles or objects in its environment.
Overall, the Wellwit Robotics W500SL Under Ride Lifting AGV is an advanced and highly capable autonomous guided vehicle that is ideal for material handling applications in manufacturing and logistics industries. Its LiDAR SLAM navigation technology and 500 kg payload capacity make it a valuable asset for any business looking to improve their efficiency and productivity. With its advanced safety features and reliability, this AGV is a powerful tool for streamlining operations and reducing costs.