Cognibotics Motion Precision Tool Suite Alternatives & Competitors
Ranked Nr. 113 of 98 Robot Accessories
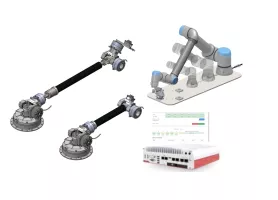
Top 10 Motion Precision Tool Suite Alternatives
- Vikaso i-BASE
- Cognibotics SigmaTau
- Cognibotics HKM1800

Vikaso i-BASE
Cobot- Platforms
Smart
Integrated WIFI allows wireless control and data collection. This data can be used for Visualisation and Data Analytics.
Compact
The i-BASE is split into TWO levels. The Top level is a Drawer that is used to mount all controls equipment. There is plenty of space to accommodate 95% of applications.
Indicative
LEDs mounted on each pillar are used to indicate Cobot System's status to nearby Operators. The i-BASE uses a VIKASO-developed LED controller allowing the use of 8-Bit RGB colours via a simple MODBUS connection.
Flexible
i-BASE has a height of 800mm (can be customised). It has integrated Castor Wheels with locks to allow flexible deployment. A strong and rigid internal structure copes with high Cobot speeds.

Cognibotics SigmaTau
SigmaTau, developed by Cognibotics, stands out for its exceptional performance in accuracy, rigidity, and dynamic motion applications. This robot employs a lightweight eight-link parallel kinematic concept, enabling superior rigidity and precision. The modular system of SigmaTau offers flexibility, allowing integration with various production equipment and installation on standard industrial foundations. Notably, the robot can be easily reconfigured and moved after initial deployment, offering adaptability for evolving manufacturing needs.
One of SigmaTau's key features is its high accuracy and rigidity across large workspaces, making it ideal for heavy-duty processes like machining. The robot's hybrid manufacturing capabilities cater to setups requiring frequent tool changes, providing versatility in applications such as milling, drilling, tapping, welding, and additive manufacturing. The low weight of SigmaTau's mechanics facilitates high-dynamic motions with 2g accelerations, reducing cycle times and enhancing overall efficiency.
The SigmaTau robot fills the gap between CNC machine tools and traditional arm robots, offering in-line high-speed machining for precision processes along the production flow. With its unique design and configuration, the robot can be employed for various tasks, including machining, friction stir welding, laser welding, additive manufacturing, and fiber placement. Integrators and machine builders are encouraged to collaborate with Cognibotics to develop tailored solutions based on the SigmaTau robot, emphasizing its adaptability and performance in advanced manufacturing scenarios.

Cognibotics HKM1800
The Cognibotics HKM1800 distinguishes itself with a unique fourth motion principle designed for fast pick-and-place applications. Unlike traditional robots such as scara, delta, and 6-axis systems, the HKM1800 boasts a patented arm structure optimized for superior performance. With high-strength, low-weight components, it is among the fastest robots available, combining an unprecedented reach with low energy consumption. Notably, 80% of the manipulator's weight is concentrated in its stationary base, contributing to its energy efficiency and enabling a small footprint that allows robots to operate within each other's workspaces, optimizing production space.
Cognibotics' world-class competence aids in integrating HKM1800 robots into various applications, including special-purpose tasks, standard cells, or machines. The robot features active motion stabilization, leveraging feedback from the robot wrist to ensure precise and controlled movements. This system efficiently compensates for payload variations and deviations, resulting in short cycle times for pick-and-place operations without compromising motion smoothness. The design includes safe cable routing through a well-protected cavity in the base, enhancing the robot's longevity and robustness while minimizing the need for maintenance.
The HKM1800's specifications include a 1800 mm radial reach, a 2000 mm pick cycle of 1.6 seconds, energy efficiency, a small footprint, and active motion stabilization. With a nominal payload of 2 kg (maximum payload of 7.5 kg), the robot operates with four axes, providing a high level of precision. Its electrical features encompass integrated bus systems, 24V EtherCAT, RS485/RS232 (optional), IO-Link (optional), and a power consumption of less than 1 kW for 1-2 meters of motion. Overall, the HKM1800 represents a leap in productivity, offering a blend of reach, speed, and energy efficiency for diverse industrial applications.