KEYENCE 3D VGR series Specifications
Ranked Nr. 28 of 96 3D Vision Systems

The KEYENCE 3D VGR series excels in object detection and user-friendliness. Suited for assembly, de-palletizing, and machine tending, it employs a 4-camera, 1-projector imaging unit to capture 136 images with striped-light patterns. Setup involves auto robot-camera calibration and CAD data upload. The Path Planning tool calculates collision-free robot motion paths for efficient object handling. A Picking Simulator enables gripper and cell design testing during work cell setup.
Unique features encompass specialized optics and advanced 3D search algorithms, ensuring precision and speed. The 4-camera setup eliminates blind spots for optimal 3D imaging. The system's novel 3D search function assures stable target detection in any orientation, bolstering accuracy. These capabilities make the KEYENCE 3D VGR series an adept solution for industrial automation.
Integrated Design Comprised of Four Cameras and a Single Projector

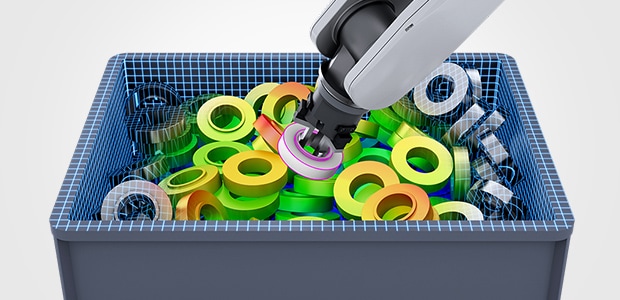
Automatically Calculate Movements for the Robot, Taking Peripheral Equipment and the Position of the Robot into Account
Path Planning Tool
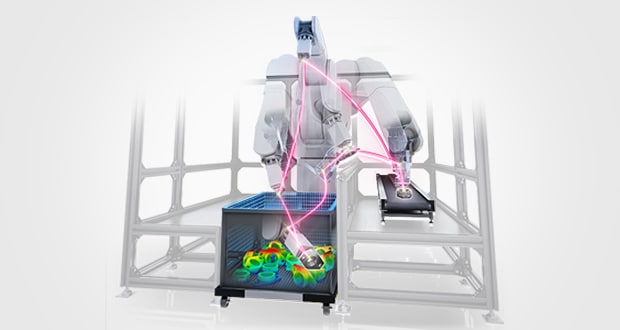
Automatic Robot Path Planning
Robot motion paths are automatically calculated to eliminate all collisions of the robot, target, and surroundings to greatly reduce robot programming time and to allow for uninterrupted bin picking operation.
Picking Simulator
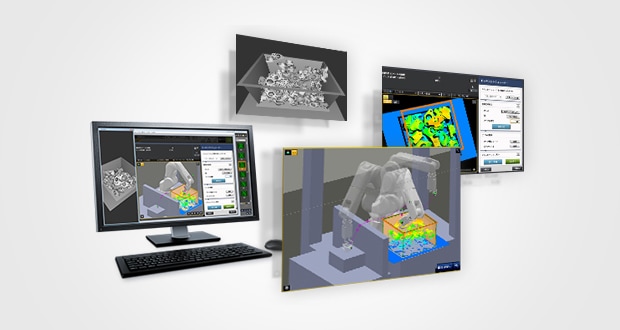
Worksite Modeling Simulation
The workcell and program can be designed in the Simulator before any physical setup is completed, which can identify potential setup problems and dramatically increase bin picking success rates.
Industry |
|
Image Type |
|
Application |
|