KUMATECH Lifting Jim Alternatives & Competitors
Ranked Nr. 75 of 186 Mobile Robots
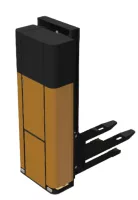
Top 10 Lifting Jim Alternatives
- iRAYPLE Forklift AMR
- IBG Automation FC Load
- Wellwit Robotics W500SL Under Ride Lifting AGV
- Wellwit Robotics W1000SL Under Ride Lifting AGV
- GESSbot GB350
- Kivnon K55A Pallet Stacker
- SAFELOG AGV L1
- MoviĜo Robotics Ŝharko10 AGV/AMR
- TÜNKERS STacker
- Kivnon K32 Tractor
- TÜNKERS TACT 1208

iRAYPLE Forklift AMR
The iRAYPLE Forklift AMR (Autonomous Mobile Robot) is a specialized solution designed based on the concept of a forklift truck. It combines the capabilities of a moving forklift and a stacking forklift, making it a versatile option for industrial automation tasks.
One of the standout features of the iRAYPLE Forklift AMR is its ability to operate in narrow channels for pick-up and release tasks. This feature enables efficient maneuverability in confined spaces, optimizing warehouse utilization and increasing productivity.
The forklift AMR is equipped with intelligent sensing capabilities, allowing it to perceive and respond to its surroundings. This includes the ability to detect obstacles, navigate through complex environments, and interact with its environment intelligently. These sensing capabilities contribute to improved safety, efficiency, and adaptability in various industrial settings.
With independent pallet identification, the iRAYPLE Forklift AMR can accurately identify and handle different types of pallets or loads. This capability enhances operational efficiency and reduces errors in material handling processes.
The forklift AMR utilizes high-precision laser SLAM (Simultaneous Localization and Mapping) navigation technology. This enables precise positioning and mapping of its environment in real-time, allowing for reliable and accurate navigation even in dynamic environments.
The iRAYPLE Forklift AMR incorporates comprehensive 360° three-dimensional safety detection mechanisms. This ensures that it can detect and respond to potential hazards from all directions, maintaining a high level of safety during operation.
The iRAYPLE Forklift AMR finds applications across various industries such as auto parts, new energy, 3C manufacturing, textile, and heavy industries. It has been successfully deployed for tasks such as cargo transfer, stacking, and shelving, offering a reliable and efficient solution for material handling and logistics operations.
While specific information about tolerance for extreme temperatures and compatibility with software systems is not provided in the given information, it is advisable to refer to the product details, parameters, and documentation provided by iRAYPLE or consult the manufacturer or official sources for detailed specifications in these areas.
In summary, the iRAYPLE Forklift AMR combines the functionalities of a moving forklift and a stacking forklift. With its narrow channel capabilities, intelligent sensing, independent pallet identification, high-precision laser SLAM navigation, and comprehensive safety detection, it offers a reliable, adaptable, and efficient solution for material handling in diverse industrial environments.

IBG Automation FC Load
AGV | Payload 1000kg | Product mass 450kgAutonomous forklift AGV for picking up and transporting Euro pallets or pallet cage.

Wellwit Robotics W500SL Under Ride Lifting AGV
AGV | Payload 500kg | Product mass 220kgThe Wellwit Robotics W500SL Under Ride Lifting AGV is a highly advanced autonomous guided vehicle designed for material handling applications in manufacturing and logistics industries. This AGV features the latest LiDAR SLAM navigation technology, which enables the vehicle to navigate and operate autonomously in complex environments. This technology uses lasers to map and create a 3D image of the AGV's surroundings, allowing it to avoid obstacles and navigate through tight spaces with ease. The LiDAR SLAM navigation system also allows for real-time localization and mapping, ensuring the AGV can quickly adapt to changes in its environment.
One of the key features of the Wellwit Robotics W500SL Under Ride Lifting AGV is its impressive 500 kg payload capacity. This makes it an ideal solution for material handling tasks that require heavy lifting and transport, such as moving large crates or pallets of goods. The AGV is equipped with a high-strength lift mechanism that can easily handle heavy loads, and its compact size and maneuverability make it ideal for use in tight spaces such as factory floors or warehouses.
In addition to its impressive payload capacity, the Wellwit Robotics W500SL Under Ride Lifting AGV also offers a high level of safety and reliability. The AGV is designed with multiple safety features, including a laser safety scanner that ensures the AGV can detect and avoid obstacles in its path. The AGV also features a robust collision avoidance system that can detect and respond to potential collisions, ensuring that the AGV can safely navigate around other vehicles or objects in its environment.
Overall, the Wellwit Robotics W500SL Under Ride Lifting AGV is an advanced and highly capable autonomous guided vehicle that is ideal for material handling applications in manufacturing and logistics industries. Its LiDAR SLAM navigation technology and 500 kg payload capacity make it a valuable asset for any business looking to improve their efficiency and productivity. With its advanced safety features and reliability, this AGV is a powerful tool for streamlining operations and reducing costs.

Wellwit Robotics W1000SL Under Ride Lifting AGV
AGV | Payload 1000kg | Product mass 260kgThe Wellwit Robotics W1000SL Under Ride Lifting AGV is a highly advanced autonomous guided vehicle designed for heavy-duty material handling applications. With its impressive 1000 kg payload capacity and advanced LiDAR SLAM navigation technology, the W1000SL AGV is an ideal solution for a wide range of industries, including manufacturing, logistics, and warehousing.
The LiDAR SLAM navigation technology of the W1000SL AGV enables it to navigate autonomously in complex environments, accurately detect obstacles, and efficiently map its surroundings. This advanced technology allows the AGV to operate safely and efficiently in environments with high levels of pedestrian and vehicular traffic.
The W1000SL AGV's high payload capacity makes it ideal for heavy lifting and transport tasks, such as moving large crates, pallets, or other heavy items within a factory or warehouse. Its high-strength lift mechanism can handle heavy loads with ease, and its compact size and maneuverability make it ideal for use in tight spaces.
The W1000SL AGV is designed with multiple safety features, including a laser safety scanner that detects and avoids obstacles in its path, a collision avoidance system that can detect and respond to potential collisions, and a warning system that alerts nearby pedestrians and vehicles of its presence. These safety features ensure that the AGV can safely navigate around other vehicles or objects in its environment, making it an ideal solution for high-traffic industrial settings.
Overall, the Wellwit Robotics W1000SL Under Ride Lifting AGV is a highly capable and versatile autonomous guided vehicle that is ideal for heavy-duty material handling applications. Its advanced navigation and handling capabilities, impressive payload capacity, and safety features make it a valuable asset for streamlining operations and reducing costs in various industrial settings.

GESSbot GB350
AGV | Payload 350kg | Product mass 150kgThe Gb350 is an automatically guided vehicle (AGV) for quick and cost-efficient automation of your internal transport processes. The Gb350 has a payload of 350kg.
No expensive extras and auxiliary systems, such as magnetic tracks, induction loops or additional safety systems are required. The AGV easily integrates into your existing production and logistics structures.
Autonomous movement
The robot moves autonomously within your company. Thanks to the fusion of various sensor systems, the Gb350 maintains an overview of everything within a radius of 20 m.
Using the Social Navigation System (SNS), it reacts to dynamic changes and always choses the optimum route. People and machines work in perfect harmony thanks to this collaborative behaviour.
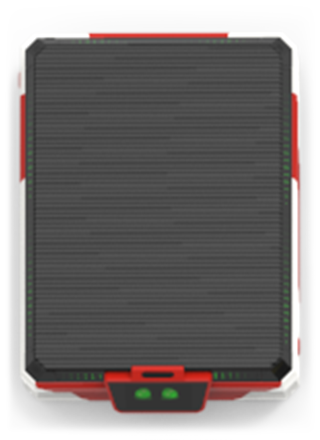
GESSbot Charge System
The charging process is fully automated
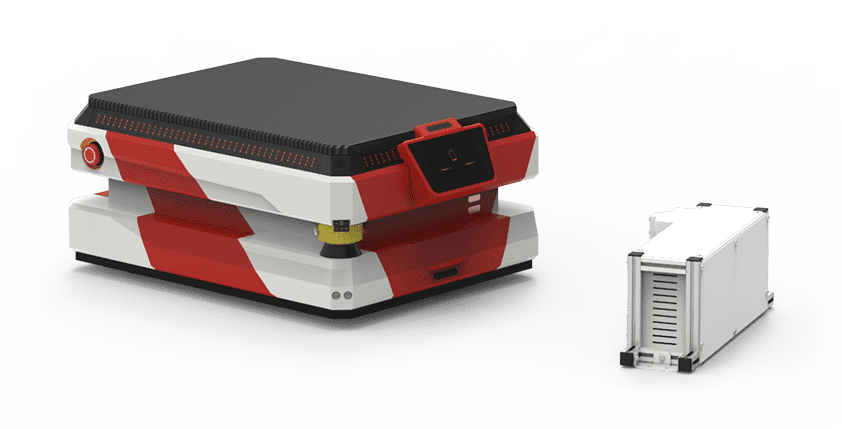
Fall protection thanks to step and cavity recognition
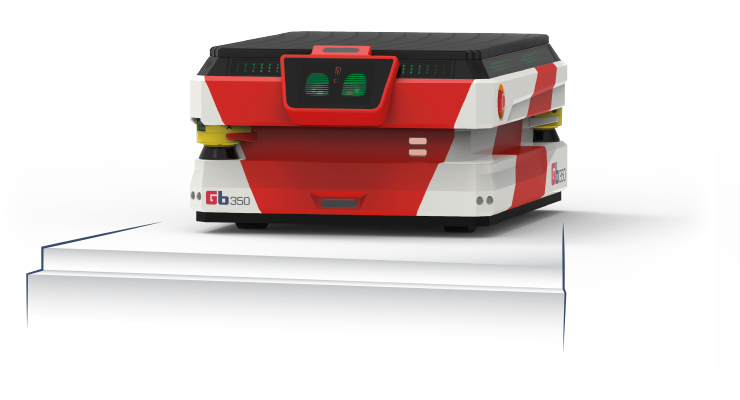
Overload-proof and with integrated scale
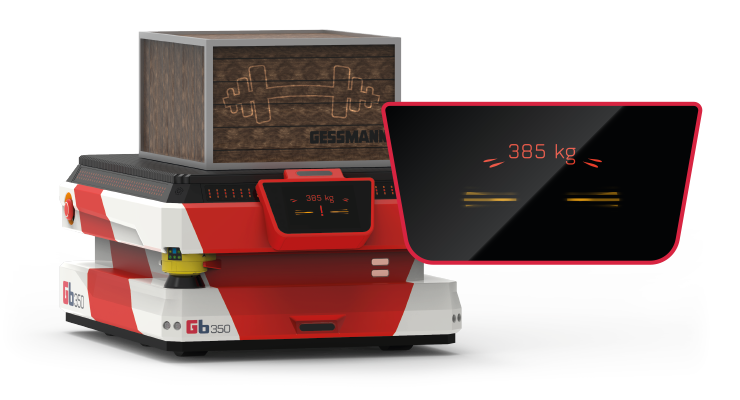
Great audio-visual features
Thanks to the GESSMANN Blackpanel System and an integrated sound module, we underline the actions and movements of the robot visually and acoustically. The latest energy-saving LED technology is used to do this.
Easy to operate
User-friendly, configurable interface
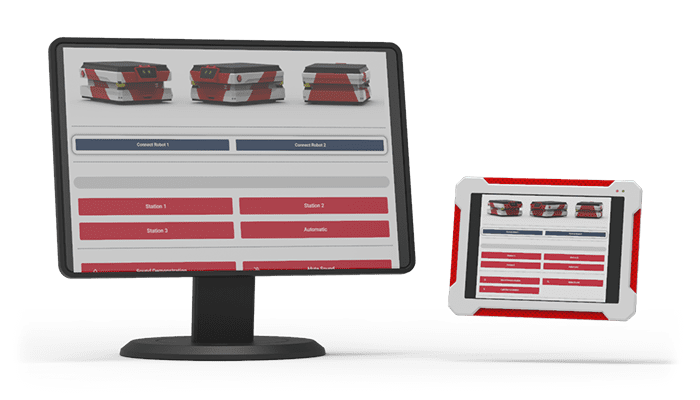
Structures with industry interfaces
Standard structures and customer-specific solutions can be provided. Those are connected directly to the Gb350 and thus form a unit.

Kivnon K55A Pallet Stacker
The Kivnon K55A Pallet Stacker is an innovative lifting automated guided vehicle (AGV/AMR) designed specifically for the transportation and stacking of palletized loads. Unlike traditional forklifts, this AGV/AMR model is equipped with advanced automation capabilities, allowing it to perform robotic process automation applications and interact seamlessly with other AGVs/AMRs, machines, systems, and people.
One of the standout features of the K55A Pallet Stacker is its ability to adapt to various pallet storage applications, including open bottom or American pallets. It is a versatile solution for both internal material dispatches and optimizing storage in intralogistics automations. This adaptability ensures enhanced process efficiency in a wide range of industrial environments.
The K55A Pallet Stacker offers precise and accurate movement, thanks to its high precision capabilities. It can make precise stops with full accuracy, ensuring efficient and reliable handling of palletized loads. The AGV/AMR utilizes lineal, two-way movement, enabling seamless navigation through different areas of the facility.
With a load capacity of up to 2,600 lbs (1,180 kg), the K55A Pallet Stacker is capable of handling heavy loads with ease. Its lifting capacity reaches up to 5 feet (1.5 meters), allowing for efficient stacking and storage of palletized goods. The AGV/AMR is designed to optimize productivity and streamline operations in various industries, including automotive and Tier 1 suppliers, manufacturing, and food and beverage.
In terms of connectivity, the K55A Pallet Stacker can be easily adapted to connect with fleet management systems. This enables seamless integration into existing automation setups, allowing for centralized control and coordination of multiple AGVs/AMRs. The compatibility with fleet management systems, including those based on VDA 5050, enhances operational efficiency and enables comprehensive monitoring and management of the AGV/AMR fleet.
The K55A Pallet Stacker is equipped with mapping navigation, which ensures efficient and accurate movement within the facility. It can navigate predefined routes and adapt to changing environments, making it suitable for dynamic and evolving industrial settings. This AGV/AMR is designed to optimize internal logistics and warehousing processes, facilitating smooth material flow and minimizing manual intervention.
In terms of technical specifications, the K55A Pallet Stacker has a length of 1,933 mm, a width of 1,354 mm, and a height of 2,346 mm. It operates as a lifting AGV and achieves a maximum speed of 2.2 mph (3.5 km/h). The AGV/AMR is powered by a lithium battery that supports online charging in an integrated circuit, ensuring continuous operation and minimizing downtime.
Overall, the Kivnon K55A Pallet Stacker stands out as a highly capable and adaptable solution for industrial automation. Its advanced automation capabilities, precise movement, high load and lifting capacities, and compatibility with fleet management systems make it a unique option for optimizing internal logistics, warehousing, and material handling processes.

SAFELOG AGV L1
Payload 1500kg | Product mass 280kgThe SAFELOG AGV L1 transport robot is characterized by its remarkable combination of high carrying capacity and exceptional maneuverability, attributed to its distinctive omnidirectional driving style. This unique feature allows the AGV L1 to effortlessly navigate in all directions, making it a versatile asset in various industrial environments.
A standout attribute of the AGV L1 is its adaptability in constrained spaces. With a device height of just 340 mm, the robot is adept at maneuvering beneath pallets or lattice boxes while accommodating loads weighing up to 1,500 kg. Its load-handling mechanism, which involves four lifting bolts, ensures secure and efficient transportation. Optional RFID readers further enhance its capabilities by identifying load specifics.
Functioning as a towing vehicle, the AGV L1 demonstrates its strength by moving trolleys and trailers with a maximum weight capacity of 3,000 kg. On the operational front, the robot is equipped with WLAN communication for seamless interaction with other AGVs and peripheral systems. This connectivity is facilitated through the utilization of the company's agent-based control software, IntelliAgent. Notably, the AGV L1 benefits from swarm intelligence, eliminating the need for a higher-level control center and enabling coordinated actions among SAFELOG robots. This advanced feature contributes to their autonomy and efficiency in industrial automation processes.

MoviĜo Robotics Ŝharko10 AGV/AMR
AGV | Payload 1000kg | Product mass 110kgMoviĜo Robotics Ŝharko10 AGV/AMR is a highly capable and extremely compact autonomous mobile robot designed to automate intralogistics in production environments. It is the most maneuverable industrial AGV available and operates in areas where floor space is limited. Due to its compact design, it can even navigate in tight spaces and work in areas with people.
The Ŝharko10 AGV is specifically designed to transport goods and materials in production environments. It can replace the use of manual pallet trucks or pallet jacks, reducing the need for manual labor and increasing efficiency. The AGV can transport pallets between different production or assembly lines, between production lines and warehouse, packing or shipping locations. The vehicle navigates autonomously, so no physical changes to its area of operation is required.
The Ŝharko10 AGV boasts several features, including its small dimensions which offer maximum maneuverability, its ability to communicate with hardware devices, its ability to turn within its own length, and its 7-8 hours operating time on full battery. Additionally, it can lift up to 1,000kg and can transport more than just pallets. It is WiFi-connected to the traffic control system MoviĜo Site and can navigate in dynamic environments. The AGV is also easily integrated with systems like ERP and WMS and can add and remove pick-up and drop-off points easily. Each vehicle can perform different tasks, and there is an online fleet dashboard for managing the vehicles. Finally, the AGV is easily maintained and offers extensive data collection options.
In conclusion, the MoviĜo Robotics Ŝharko10 AGV/AMR is an ideal solution for automating intralogistics in production environments. Its compact design, high maneuverability, and ability to operate autonomously make it an efficient and cost-effective solution for transport tasks. With its easy integration with existing systems and online fleet dashboard, the Ŝharko10 AGV offers a complete solution for modern production facilities looking to automate their intralogistics processes.

TÜNKERS STacker
Payload 1000kg | Product mass 2700kgThe confident TÜNKERS PALLETMOVER AGV STACKER is able to move in narrow aisles with high precision. PALLETMOVER AGV STACKER places its load carriers precisely in transfer stations.
The counterweight principle enables transfer even in locations that are difficult to access. With an optional fork adjustment, it adapts flexibly to the load carriers.

Kivnon K32 Tractor
The Kivnon K32 Tractor is an AGV/AMR designed for efficient and reliable load transportation in internal logistics processes. With its one-way movement and towing capacity of up to 2,000kg, it's ideal for handling large loads.
The AGV utilizes magnetic guidance navigation for precise maneuvering and can be seamlessly integrated with fleet management systems, including those based on VDA 5050. This allows for optimized coordination and control of the AGV within the overall logistics operations.
With high precision and advanced safety measures, including laser scanners, ultrasound sensors, and a safety PLC, the K32 Tractor ensures accurate stops and secure operations. These features contribute to a safe working environment and help prevent collisions or accidents.
The K32 Tractor comes in two versions: the K32 and K32P, offering flexibility to meet different operational requirements. Its compact dimensions, with a length of 1170mm, width of 480mm, and height of 1040mm, allow for easy maneuverability in tight spaces.
The AGV is powered by either AGM or lithium batteries, offering exchangeable and online charging capabilities through an integrated circuit. This ensures continuous operation without the need for manual battery replacement.
The K32 Tractor's standout features, towing capacity, compatibility with fleet management systems, and advanced safety measures make it a reliable and efficient solution for industrial automation in various sectors.