Loading Robots by DF Nalon Sidebot Alternatives & Competitors
Ranked Nr. 144 of 182 Mobile Robots
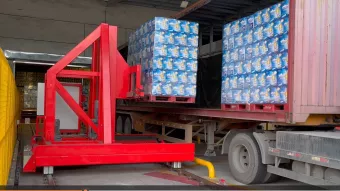
Top 10 Nalon Sidebot Alternatives
- iRAYPLE Forklift AMR
- Loading Robots by DF Nalon Backbot
- Loading Robots by DF Nalon Backbot
- Vecna Robotics VECNA APT
- STILL Gmbh iGo systems
- AiTEN Robotics MP10S
- TÜNKERS TRoll 2216
- TÜNKERS TRoll 2214
- Jungheinrich AG EZS 350a

iRAYPLE Forklift AMR
The iRAYPLE Forklift AMR (Autonomous Mobile Robot) is a specialized solution designed based on the concept of a forklift truck. It combines the capabilities of a moving forklift and a stacking forklift, making it a versatile option for industrial automation tasks.
One of the standout features of the iRAYPLE Forklift AMR is its ability to operate in narrow channels for pick-up and release tasks. This feature enables efficient maneuverability in confined spaces, optimizing warehouse utilization and increasing productivity.
The forklift AMR is equipped with intelligent sensing capabilities, allowing it to perceive and respond to its surroundings. This includes the ability to detect obstacles, navigate through complex environments, and interact with its environment intelligently. These sensing capabilities contribute to improved safety, efficiency, and adaptability in various industrial settings.
With independent pallet identification, the iRAYPLE Forklift AMR can accurately identify and handle different types of pallets or loads. This capability enhances operational efficiency and reduces errors in material handling processes.
The forklift AMR utilizes high-precision laser SLAM (Simultaneous Localization and Mapping) navigation technology. This enables precise positioning and mapping of its environment in real-time, allowing for reliable and accurate navigation even in dynamic environments.
The iRAYPLE Forklift AMR incorporates comprehensive 360° three-dimensional safety detection mechanisms. This ensures that it can detect and respond to potential hazards from all directions, maintaining a high level of safety during operation.
The iRAYPLE Forklift AMR finds applications across various industries such as auto parts, new energy, 3C manufacturing, textile, and heavy industries. It has been successfully deployed for tasks such as cargo transfer, stacking, and shelving, offering a reliable and efficient solution for material handling and logistics operations.
While specific information about tolerance for extreme temperatures and compatibility with software systems is not provided in the given information, it is advisable to refer to the product details, parameters, and documentation provided by iRAYPLE or consult the manufacturer or official sources for detailed specifications in these areas.
In summary, the iRAYPLE Forklift AMR combines the functionalities of a moving forklift and a stacking forklift. With its narrow channel capabilities, intelligent sensing, independent pallet identification, high-precision laser SLAM navigation, and comprehensive safety detection, it offers a reliable, adaptable, and efficient solution for material handling in diverse industrial environments.
Loading Robots by DF Nalon Backbot

Vecna Robotics VECNA APT
Product mass 982kgThe Vecna APT driverless pallet truck stands out as an efficient solution for industrial automation in warehousing and distribution facilities. Designed to optimize operations, this robot eliminates non-value-add long-distance travel and enhances efficiency for lift operators, all while maintaining a high payload capacity.
Noteworthy features of the Vecna APT include its impressive 7,936 lbs maximum payload capacity and a top speed of 6.7 mph. It offers clean hand-offs with an 18'6 ft right angle stack capability and can navigate through narrow 8'6 ft aisles with ease. The robot's adaptability to various pallet types, including stringer, block, and plastic pallets, with or without bottom boards, adds to its versatility.
The Vecna APT's specialized specifications contribute to its uniqueness. It employs dynamic route planning with dynamic traffic management to balance loads efficiently. The capability for multi-pallet hauling, including double-stacked pallets up to 8,000 lbs, sets it apart. Additionally, its compatibility with LPN scanning for pallet barcode tracking, ANSI B56.5 compliance for safety, and real-time task interleaving for optimized forks-full efficiency underline its comprehensive capabilities. With the advantage of opportunistic charging, the Vecna APT ensures 24/7 operation, making it a valuable asset for enhancing warehousing and distribution operations.

STILL Gmbh iGo systems
STILL's iGo systems offer individualized automation solutions tailored to specific warehouse requirements. These systems enable automated interaction between different trucks, allowing for driverless transport tasks within the warehouse. With years of experience, STILL understands that each warehouse situation is unique, and iGo systems provide perfectly coordinated combinations of series-produced trucks and software, customized to meet specific needs.
The iGo systems encompass a comprehensive range of automated STILL series-produced trucks, providing a complete and continuous material flow from goods receipt to outgoing deliveries. The intelligent iGo software controls the trucks, regulates traffic, monitors battery usage, and optimizes fleet utilization. This intelligent control system ensures efficient and streamlined operations throughout the warehouse.
One of the standout features of iGo systems is the effective cooperation between manually driven vehicles and semi- or fully-automated transport systems. This seamless integration allows for smooth collaboration between different types of vehicles, optimizing productivity and ensuring a cohesive workflow.
Modern navigation technologies are employed in iGo systems to enable secure and independent movement of vehicles within the warehouse. These navigation systems provide precise positioning and routing, allowing the trucks to navigate safely and efficiently. Safety is a top priority, with pedestrian protection systems and sensor technology ensuring the utmost safety and precise pallet detection.
The flexibility of iGo systems is another key advantage. The automated series-produced trucks can also be operated manually when required, providing versatility and adaptability in different warehouse scenarios. This flexibility allows for seamless transitions between manual and automated operations, ensuring continuous workflow and adaptability to changing needs.
iGo systems offer standardized and scalable solutions to meet various automation requirements. Whether it's a small-scale automation implementation or a large-scale warehouse transformation, the solutions can be tailored to the specific needs of the facility.
With iGo systems, the response times for design, quotation preparation, and project implementation are short and predictable. This ensures a streamlined and efficient process from the initial planning stages to the successful deployment of the automation solution.


TÜNKERS TRoll 2216
AGV | Payload 1000kg | Product mass 1350kgThe TÜNKERS Automated TRoll has an active chain gripping system that enables a fully automatic pick-up of large load carriers. The loading and unloading options on either side in combination with an omni-directional travel mode makes it particularly flexible in use. The optional 3D cameras reliably detect forklift tines in the room, for example. Digital LEDs visualise events and driving movements.

TÜNKERS TRoll 2214
AGV | Payload 1300kg | Product mass 1400kgThe TÜNKERS Automated TRoll has an active chain gripping system that enables a fully automatic pick-up of large load carriers. The loading and unloading options on either side in combination with an omni-directional travel mode makes it particularly flexible in use. The optional 3D cameras reliably detect forklift tines in the room, for example. Digital LEDs visualise events and driving movements.

Jungheinrich AG EZS 350a
The Jungheinrich EZS 350a is a versatile and robust automated tow tractor designed to enhance production environments. It excels in effectively pulling trailers weighing up to 5,000 kg as part of a tow train system. Developed from their proven standard truck, the EZS 350a is specifically optimized for warehouse work and transport processes, making it a reliable and efficient solution.
The standout feature of the EZS 350a is its precision navigation technology. The truck utilizes laser navigation, detecting reflectors installed along the travel route. This advanced navigation system ensures accurate and reliable movement throughout the facility, enabling smooth and efficient towing operations. This precision is particularly crucial when towing heavy trailers, ensuring safety and reducing the risk of accidents or damage to goods.
Safety is a paramount concern in industrial automation, and the EZS 350a is equipped with an extensive safety system. This system ensures the protection of both the vehicle and the people working in the vicinity. With its integrated safety features, the tow tractor can operate in mixed environments alongside manual trucks and pedestrians. This versatility allows for seamless integration into existing structures or utilization as a standalone solution, providing increased efficiency in diverse production facilities.
The EZS 350a is equipped with a 24-V 3-phase AC motor, which offers high performance while maintaining low energy consumption. This combination of power and energy efficiency ensures optimal performance during towing operations while minimizing operating costs. The motor provides consistent and reliable power delivery, allowing the tow tractor to handle heavy loads with ease.
In terms of specialized specifications, the provided information does not explicitly mention tolerance for extreme temperatures or compatibility with specific software systems. However, it's worth noting that Jungheinrich products are known for their high-quality engineering and customization options. Therefore, it is possible that the EZS 350a may offer features such as tolerance for extreme temperatures, making it suitable for use in challenging environments like cold storage facilities or high-temperature manufacturing areas.
Additionally, the EZS 350a can be integrated into existing IT structures, allowing for seamless communication and coordination with other automated equipment or warehouse management systems. This compatibility enhances overall workflow efficiency and enables the tow tractor to be seamlessly incorporated into existing automation setups.
In summary, the Jungheinrich EZS 350a automated tow tractor is a versatile and robust solution for enhancing production environments. Its standout features include precision navigation technology, an extensive safety system, and a powerful yet energy-efficient motor. The ability to operate in mixed environments, along with its compatibility with existing structures or standalone use, provides flexibility in various production facilities. While not explicitly mentioned, it's possible that the EZS 350a offers specialized specifications such as tolerance for extreme temperatures and compatibility with specific software systems, further enhancing its capabilities in industrial automation.