Boston Dynamics Atlas Alternatives & Competitors
Ranked Nr. 1 of 33 Humanoid Robot
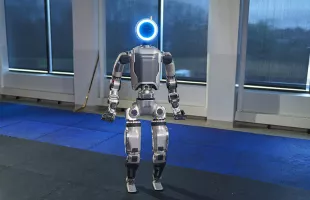
Top 10 Atlas Alternatives
- Ti5 Robotics Yao Guang
- Unitree H1
- Unitree G1
- FDROBOT TLIBOT
- Engineered Arts Ameca
- UBTECH Robotics Walker S
- Honda ASIMO
Ti5 Robotics Yao Guang
Ti5 Robotics offers the "Yao Guang" humanoid robot, designed with advanced features for various applications. Standing at 1.7 meters tall and weighing only 48 kg, the robot boasts an impressive 44 degrees of freedom, enabling agile movements and adaptability in dynamic environments. Its lightweight construction, combined with high-torque leg joints capable of delivering up to 490 N·m, facilitates strong performance in tasks requiring significant lifting capabilities and maneuverability.
The Yao Guang is equipped with a high-computing power controller and dual-vision systems, allowing it to perform complex navigational and operational tasks autonomously. The robot features a 7-degree-of-freedom arm, with articulated shoulder, elbow, and wrist joints, enabling it to manipulate objects with precision. Additionally, it integrates advanced sensors, including a depth camera and ultra-high-definition long-range lidar, enhancing its ability to operate in challenging terrains and hazardous environments.
Applications for the Yao Guang humanoid robot span various fields, including manufacturing, logistics, and research. Its collaborative capabilities make it suitable for working alongside humans in industrial settings, while its adaptability allows for use in hazardous environments, where human intervention may be risky. Overall, the Yao Guang represents a significant advancement in robotic technology, aiming to enhance automation and efficiency across multiple sectors.

Unitree H1
The Unitree H1 stands out as a full-size universal humanoid robot, primarily known for its high power performance. It is equipped with advanced powertrain technologies, allowing it to achieve speeds of up to 3.3 meters per second, a record in robot mobility. Its robust construction enables high maneuverability and flexibility, with a peak torque density of 189N.m/kg, making it highly capable in a variety of demanding operational scenarios.
Unitree H1 also excels in autonomous navigation, being the first full-size humanoid robot capable of running autonomously in China. It features a stable gait and flexible movement capabilities, designed to navigate complex terrains and environments. This level of autonomy is supported by its sophisticated sensor system, including 3D LiDAR and depth cameras, facilitating precise spatial awareness and environmental interaction.
Additionally, the robot is equipped with state-of-the-art sensory capabilities, offering 360° depth perception. This is achieved through an integration of 3D LiDAR and a depth camera system that captures high-precision spatial data for panoramic scanning. This capability ensures the Unitree H1 can operate effectively in intricate settings, enhancing its utility across a wide range of applications, from industrial tasks to research and development in robotics.

Unitree G1
Payload 2kgThe Unitree G1 is a versatile and innovative robot designed to push the boundaries of flexibility and manipulation capabilities. With an impressive range of motion thanks to its 23~43 joint motors, it offers a level of flexibility that surpasses conventional robotics platforms. This expansive joint movement space enables the G1 to navigate complex environments and perform a wide variety of tasks with ease, making it suitable for diverse applications in research, industry, and beyond.
Driven by imitation and reinforcement learning techniques powered by AI, the Unitree G1 represents the cutting edge of robotics technology. This integration of AI accelerates its development and evolution, allowing it to adapt and learn from its interactions with the environment. By leveraging advanced AI-driven algorithms, the G1 can continually improve its performance and capabilities, paving the way for enhanced efficiency and productivity in various tasks and applications.
One of the standout features of the Unitree G1 is its force control dexterous hand, which enables precise manipulation of objects with sensitivity and reliability. Combined with force-position hybrid control, this hand can simulate human-like movements, making it adept at handling delicate objects and executing intricate tasks. Whether it's grasping, lifting, or manipulating items with dexterity, the G1's versatile hand offers a level of control that opens up new possibilities in robotics applications, from assembly lines to research laboratories.

FDROBOT TLIBOT
Payload 145kgThe TLIBOT by FDROBOT is a highly advanced humanoid robot designed for a wide range of industrial applications, including film and TV entertainment, military industry, education and training, logistics handling, wellness care and nursing, industrial production, medication delivery, and housekeeping services. Its design integrates multifunctional capabilities and intelligent interaction systems, making it versatile across different scenarios.
TLIBOT is equipped with sophisticated sensory technologies including 3D vision and LIDAR, which enable precise environmental mapping and object recognition. This allows for effective automatic obstacle avoidance, enhancing its operational safety and efficiency in complex environments. The robot also features force feedback and voice interaction capabilities, providing a more interactive and responsive user experience.
The robot's mechanical design is notable for its 71 degrees of freedom, which allows movements that closely mimic human dexterity. This level of articulation is supported by powerful actuators capable of a maximum joint torque of 450Nm and a joint speed of up to 720°/s. TLIBOT's robust build includes a long-lasting 1250Wh battery and a substantial load capacity, with each leg capable of bearing up to 65kg, and a combined load capacity of 145kg. These features make TLIBOT an effective tool for handling demanding industrial tasks and for applications requiring high levels of mobility and manipulation.

Engineered Arts Ameca
Ameca, developed by Engineered Arts, represents a pinnacle in humanoid robotics designed for advanced human-robot interaction. Its framework is built on the company's proprietary Mesmer technology, which aims to achieve lifelike human movements and expressions. Ameca's standout capability lies in its ability to display smooth, natural motion and a wide range of facial expressions, making it highly effective for engaging and interacting with humans in diverse settings.
In terms of architecture, Ameca is designed to be modular and upgradeable, both in hardware and software. This allows for specific components, like an arm or the head, to be independently operated, which is advantageous for users who may not require a full humanoid robot. The modularity also ensures that Ameca remains a future-proof platform, where upgrades can be integrated without the need to replace the entire unit. This design philosophy extends Ameca’s utility and enhances its adaptability to evolving technological advancements.
Ameca is also cloud-connected, which significantly broadens its applications. Users can access robot data, control it remotely as a personal avatar, and utilize animation and simulation features from anywhere globally. This connectivity supports a wide array of uses, from educational and entertainment purposes to practical implementations in telepresence and digital interactions. This makes Ameca not just a robot but a versatile platform for exploring the future dynamics between humans and machines in both physical and digital realms.

UBTECH Robotics Walker S
The UBTech Walker S is an advanced industrial humanoid robot designed for sophisticated manufacturing environments. Standing 1.7 meters tall, it features a robust structure with force-compliant drive joints and a rigid-flexible coupling hybrid system, allowing for stable walking and navigation on mobile production lines. Its all-terrain autonomous adaptation enhances its ability to operate in diverse conditions.
Walker S excels in comprehensive perception, thanks to its 41 servo joints with force feedback, and a range of sensors including visual, audio, and distance inputs. This setup supports its advanced 3D semantic navigation, where high-resolution RGBD sensors help it create detailed 3D maps and navigate safely by avoiding obstacles.
The robot's integration of a large language model (LLM) allows it to understand complex intents and plan finely-tuned actions. Its capabilities extend to advanced object detection and grasping through 3D point cloud processing, enhancing its efficiency in tasks requiring hand-eye coordination. Additionally, Walker S ensures real-time data synchronization with manufacturing management systems, promoting seamless operations across the factory floor.

Honda ASIMO
Honda's ASIMO, an acronym for Advanced Step in Innovative Mobility, was one of the most advanced humanoid robots during its time of active development. Engineered to operate in human environments, ASIMO could walk or run on two legs, with the ability to navigate around people and objects without falling. This capability was highlighted by its ability to maintain balance even when unexpectedly bumped into. ASIMO's design focused on mobility within the same spaces as humans, showcasing a significant stride in robotics aimed at practical daily interactions.
ASIMO was also designed to perform tasks using its hands, which allowed it to interact with objects and environments in a human-like manner. It could perform a variety of manual tasks from opening a bottle to operating switches and handling delicate objects, making it a potential assistant in both home and office settings. Furthermore, ASIMO could understand spoken commands and respond to them, facilitating interaction with people that included responding to the intentions and commands of nearby individuals.
Beyond its immediate functionalities, ASIMO served as a long-term research project that contributed to Honda's understanding of safe robot-human coexistence. Over its operational period, ASIMO took over 33 million steps and walked a total distance of nearly 7,907 kilometers, providing extensive data on long-term robot use in human environments. This experience informed safety enhancements and highlighted the need for ongoing development to address scenarios like ensuring safety when falling near children, reflecting the complexities of real-world human-robot interaction. Honda's ongoing research now also explores non-bipedal robot mobility to enhance safety and efficiency, underscoring the evolving nature of robotics in adapting to human spaces.