Fisnar Cartesian robot F8000 series Alternatives & Competitors
Ranked Nr. 37 of 36 Cartesian (Gantry) Robots
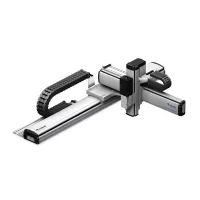
Top 10 Cartesian robot F8000 series Alternatives
- YAMAHA Gantry type

YAMAHA Gantry type
Payload 50kgYamaha's Gantry type robots are designed with a guide railing at the end of the Y-axis for additional support, providing greater stability and precision during operation. The gantry type robots are available in 2, 3, or 4 axes configurations, allowing for flexibility in application and movement range.
With the gantry type configuration, the Y-axis carriage is supported by two guide rails, one on each side, ensuring stability and accuracy during movement. The guide rails also help to minimize vibration and ensure smooth operation. The additional support provided by the guide rail makes this type of robot ideal for applications that require high precision, such as machining, testing, or inspection.
The Gantry type robots are available in 2, 3, or 4 axes configurations, allowing for a wide range of movement options. The X-axis moves horizontally, while the Y-axis moves vertically along the guide rail, providing a large working area. The Z-axis can also be added for up and down movement, and an optional rotary axis can be added for increased flexibility.
The Gantry type robots are ideal for applications such as CNC machining, assembly, and inspection, where high precision and stability are essential. They are also used in industries such as automotive, aerospace, and electronics, where high accuracy and repeatability are critical for quality control.