- Robot Software
- MVTec
- MERLIC
- Specifications

A NEW GENERATION OF MACHINE VISION SOFTWARE
MVTec MERLIC is an all-in-one software product for quickly building machine vision applications without any need for programming.
It is based on MVTec's extensive machine vision expertise and combines reliable, fast performance with ease of use. An image-centered user interface and intuitive interaction concepts like easyTouch provide an efficient workflow, which leads to time and cost savings.
MERLIC provides powerful tools to design and build complete machine vision applications with a graphical user interface, integrated PLC communication, and image acquisition based on industry standards. All standard machine vision tools such as calibration, measuring, counting, checking, reading, position determination, as well as 3D vision with height images are included in MVTec MERLIC.
MERLIC 5
MERLIC 5 introduces a new licensing model for greatest possible flexibility. It allows customers to choose the package – and price – that exactly fits the scope of their application. Depending on the required number of image sources and features (“add-ons”) for the application, the packages Small, Medium, Large and X-Large as well as a free trial version is available. This new "package" concept replaces the previous "editions" model.
With the release of MERLIC 5, MVTec’s state-of-the-art deep learning technologies are finding their way into the all-in-one machine vision software MERLIC. Easier than ever before, users can now harness the power of deep learning for their vision applications.
MERLIC 5 includes Anomaly Detection and Classification deep learning technologies:
The "Detect Anomalies" tool allows to perform all training and processing steps to detect anomalies directly in MERLIC.
The "Classify Image" tool enables using classifiers (e.g., trained with MVTec's Deep Learning Tool) to easily classify objects in MERLIC.
Software type |
|
MERLIC Alternatives
See all 89 Robot Software

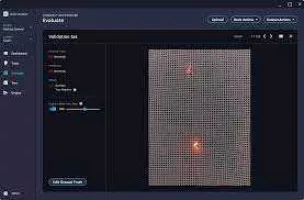
neurala Vision AI Software
Vision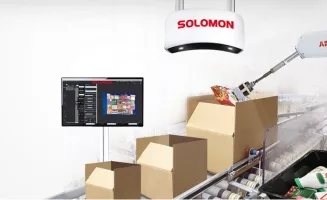
SOLOMON vision JustPick
Vision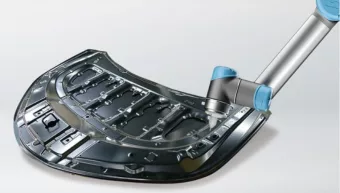
SOLOMON vision Solmotion
Vision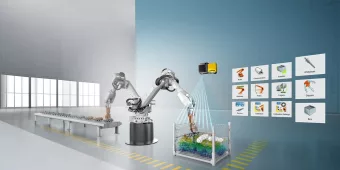
Liebherr Group Robot vision technology packages - LHRobotics.Vision
Bin picking | Vision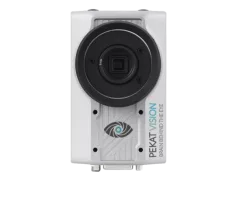
PEKATVISION Software Bundled with Camera
Vision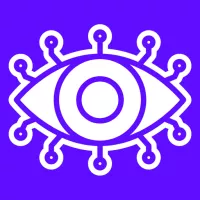
EasyODM.tech EasyODM Machine Vision Software
Vision