RAD Spring-Loaded Compliance Alternatives & Competitors
Ranked Nr. 139 of 116 End of Arm Tools
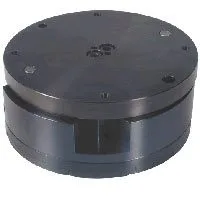
Top 10 Spring-Loaded Compliance Alternatives
- RAD Pneumatic Compliance
- RAD Spring-Loaded
- Zimmer SERIES WWR
- RAD Pneumatic Spring-Assist

RAD Pneumatic Compliance
- Reduce robot* programming time
- Open up part tolerances
- Decrease scrap caused by misalignment
- Increase assembly speed
- Minimize part and tool damage caused by contact forces
- Reduce downtime and machine wear caused by parts jamming and wedging
RAD’s Pneumatic Compliance Device:
- Compensates for positional misalignment
- Is compliant in X and Y axes, radially (laterally), as well as rotationally
PLEASE NOTE: If you require axial (“Z” axis) or angular compliance, as well as rotational, the Ultimatic™ Collision Sensor can be used as a compliance device in some cases. - Provides precise centering to within ±0.001″ (0.025mm)
- Features a standard pneumatic ‘lock up in the center position’ function to prevent the device from floating during rapid transport and/or to disable the compliance when it’s not needed
- Allows instantaneous transition from smooth compliance to centered rigidity
- Offers no compression in the Z axis – making it ideal for applications requiring moderate insertion forces through the center line of unit
- Allows pneumatic adjustment so user can easily change the external force required to offset the movable plate
Assembly Operations
- Positioning on an assembly line
- Aligning molds
- Locating parts in machines
Insertion Operations
- Placing washers, fans, or gears onto shafts
- Inserting bearings into drive assemblies
Operating Principle
RAD’s Compliance Devices provide allowances for both lateral and rotational misalignments. This compliancy allows parts to automatically align themselves upon striking a lead-in chamfer or tapered guide. RAD Compliance Devices function through a series of bearings and pneumatic pistons.
* can also be used on linear actuators, pick & place machines, and other automated equipment.

RAD Spring-Loaded
The Uni-Coupler™ Collision Sensor is RAD’s patented, spring-loaded, mechanical collision sensor that:
- Stops the robot* in the event of a crash to minimize costly damage to the robot and/or tooling. RAD’s collision sensor provides protection even if the robot itself is not moving.
- Absorbs the crash energy by allowing up to 15º of deflection following a collision.
- Automatically resets to within ± 0.002″ (0.051mm) to maximize uptime and eliminate the need for human intervention.
- Allows up to 0.040″ (1.02mm) “give” in the coupling before the load sensing mechanism is activated (in compliant models) to avoid nuisance tripping.
Operating Principle
RAD’s Uni-Coupler™ Collision Sensor is a spring-loaded mechanical device that signals your robot’s E-stop or controller when the tooling encounters an obstruction. The lateral or vertical force applied during a collision opens a normally closed switch that sends the “stop” signal.
Note: The Uni-Coupler™ Collision Sensor can be used as a compliance device by installing the unit without connecting the sensor switch.
* can also be used on linear actuators, pick & place machines, and other automated equipment.

Zimmer SERIES WWR
Payload 20-300 kg- Secure hold during pressure drop
The combination of spring-loaded and a high gear ratio guarantees them a safe machine - Extremely flat design
This structure reduces the moment load for your robot to a minimum and makes it possible to use smaller and more affordable sizes - Inexhaustible variety of media transfer systems
No matter which medium you would like to transmit, we will draw from our wealth of experience in implementing projects and find a solution to suit your needs!

RAD Pneumatic Spring-Assist
RAD’s Spring-Assist Ultimatic™ Pneumatic Collision Sensor minimizes the potential for costly damage to the robot arm or tooling in the event of a crash and maximizes uptime by automatically returning to within 0.0005″ (0.013mm) of its starting position once it has been separated from the source of the crash.
NOTE: RAD Spring-Assist Ultimatic™ Collision Sensors effectively replace the discontinued EOA MultiClutch Breakaway Safety Devices.
The Spring-Assist Ultimatic™ Collision Sensor is RAD’s patented mechanical collision sensor that:
- Sends a signal to the system’s E-stop or controller within 4 to 10ms of a collision to minimize costly damage to equipment and/or tooling. RAD’s collision sensor provides protection even if the system itself is not moving.
- Absorbs the crash energy without loss of air pressure in the collision sensor. Keeping the air in the collision sensor prevents tooling “sag” and eliminates the effects of compressed air being released into the environment.
- Resets Automatically to within ± 0.0005″ (0.013mm) in X, Y, and Z dimensions and to within ± 0.017º rotationally to maximize uptime and eliminate the need for human intervention.
- Increases Payload Capacity to nearly double that of RAD’s standard U-4622 with no increase in size
- Maintains significant resistance even with no air pressure, reducing tooling sag if air pressure is lost
- Provides angular, rotation and axial (compressive) compliance
- Allows pneumatic adjustment so the user can easily change the amount of resistance the unit must encounter before signaling a collision.
- Has a compliance adjustment feature that lets the user determine the amount of deflection allowed before a signal is sent to the robot’s E-stop or controller.
Operating Principle
RAD’s Spring-Assist Ultimatic™ Collision Sensor works by establishing the minimal points of contact required to restrain all degrees of freedom (movement) in normal operation. When a robotic crash occurs, external forces upset this balance thereby allowing angular, rotational or compressive compliance. This motion opens a normally closed switch and sends a signal to your robot’s E-stop or controller.
Note: The Spring-Assist Ultimatic™ Collision Sensor can be used as a compliance (alignment) device rather than a collision sensor by simply mounting the unit without wiring it to the robot. Please see the Compliance Device section for more end-effector compliance options.