SOLOMON vision Solmotion Specifications
Ranked Nr. 32 of 85 Robot Software

Vision-guided robot solution combines 3D-vision with machine learning
Increases manufacturing flexibility and efficiency
Solmotion is a system that automatically recognizes the product’s location and makes corrections to the robot path accordingly. The system reduces the need for fixtures and precise positioning in the manufacturing process, and can quickly identify the product’s features and changes. This helps the robot to react to any variations in the environment just as if it had eyes and a brain. The use of AI allows robots to break through the limitations of the past, providing users with high flexibility, even when dealing with previously unknown objects.
Solomon’s AI technology combines 2D and 3D vision algorithms, alternating them in different contexts. Through the use of neural networks, the robot is trained not only to see (Vision) but also to think (AI), and move (Control). This innovative technology was honored in the Gold Category at the Vision Systems Design Innovators Awards. In addition to providing a diverse and flexible vision system, Solmotion supports more than twenty world-known robot brands. This greatly reduces the time and cost of integrating or switching different robots, giving customers the ability to rapidly automate their production lines or quickly move them to a different location. This makes Solmotion a one-stop solution that provides system integrators and end-users with a full range of smart vision tools.
Through a modular and intelligent architecture, Solmotion can quickly identify product changes and make path adjustments in real-time, regardless of any modifications made to the production line. This results in a more -flexible manufacturing process while improving the production environment to become a zero mold, zero inventory smart production factory.
Solmotion Key Advantages:
Cuts mechanical tooling costs
Saves the costs of fixture and storage space
Reduces changeover time
Decreases the accumulated tolerance caused by placing position
Solmotion Key Features:
CAD/CAM software support (offline instead of off-line)
Graphical User Interface, easy for editing program logic
Automatic object recognition, and corresponding path loading
Automatic/manual point cloud data editing
User-friendly path edition/creation/modification
Project Management/Robot Program Backup
Support for more than 20 world-known robot and PLC brands
ROS automatic obstacle avoidance function
Solmotion Key Functions
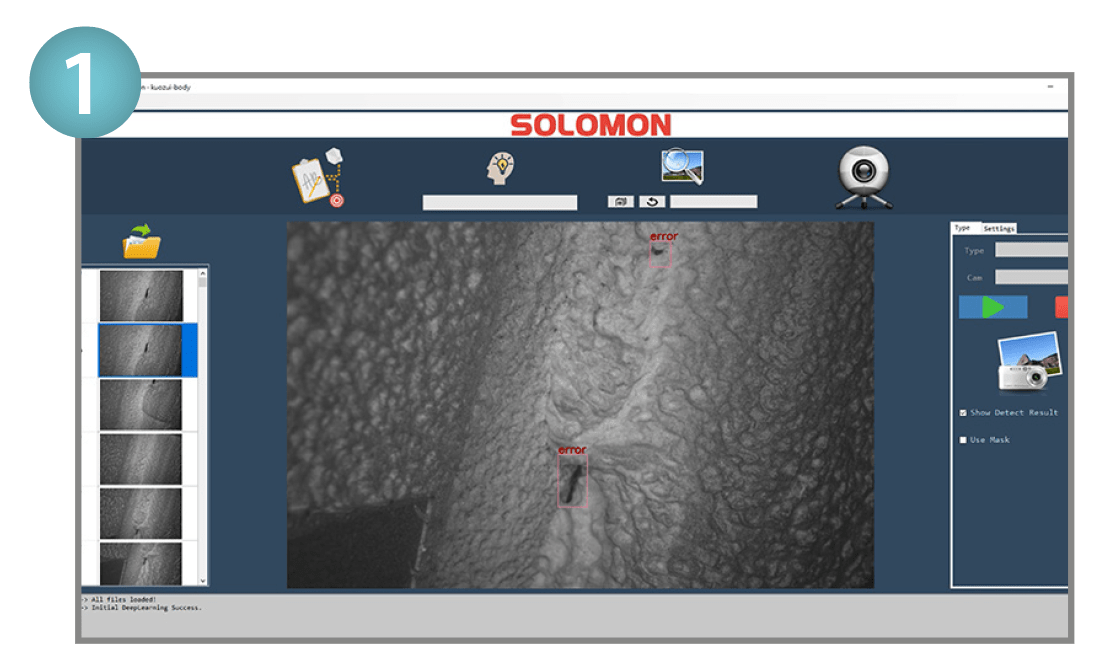
AI Deep Learning tool
Neural networks can be used to train the AI to learn to identify object features/defects on the surface of the items. Comparing it to traditional “rule-based” AOI, AI inspection application scenarios are wider, smarter, and do not require deep technical knowledge. Together with the Solmotion vision-guided robot technology, a camera mounted on a robot can perform just like human eyes and inspect each detail on the surface of the objects.
Applications :
Painting defects and welding inspection, mold repairing, metal defect inspection, and food sortation.
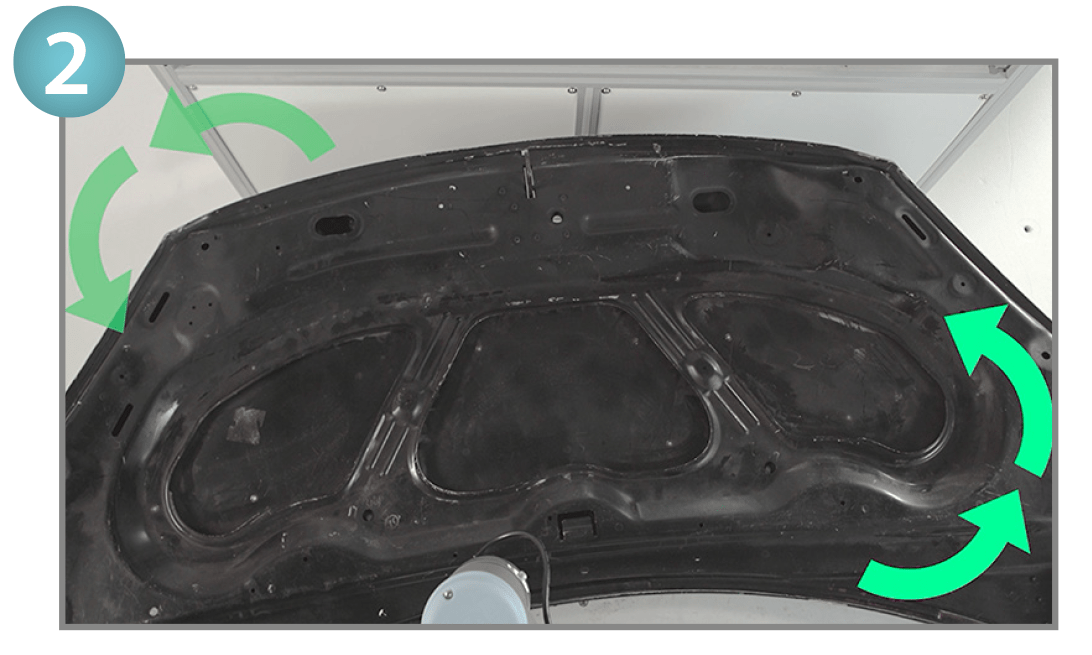
3D vision positioning system
The objects can be placed randomly without the need for precision fixtures or a positioning mechanism. Through the use of visual recognition of partial features, AI can locate the position of the parts in space, generating their displacement and rotation coordinates in real-time, which are then fed back to the robot for direct processing. Also, to achieve flexible production, the system uses a path-loading function based on an object feature recognition function. The software can also generate the robot path through off-line programming, making it a suitable solution for Hi-Mix or Low-Volume, mixed production scenarios.
Applications:
Various Robot Machine Tending Applications.
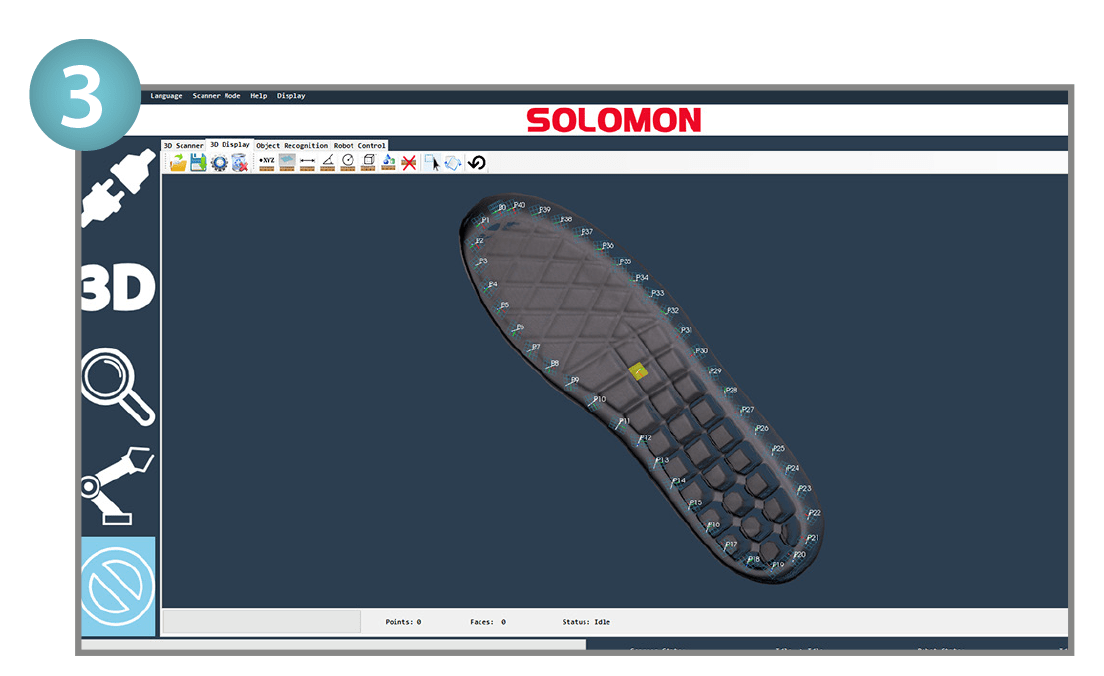
Robotic path planning auto-generation
There is no need to manually set the robot path, Solomon’s AI will learn the edge and automatically generate the path planning. The processing angle can be adjusted to “vertical” or “specified” according to the situation. The surface-filling path generating and corner path optimization functions are also available. Supporting more than 20 robot and PLC brands; our solution is suitable for products that are time-consuming, Hi-Mix or Low-Volume, and highly variable in path teaching.
Applications:
Cutting, Gluing, Edge trimming, Painting.
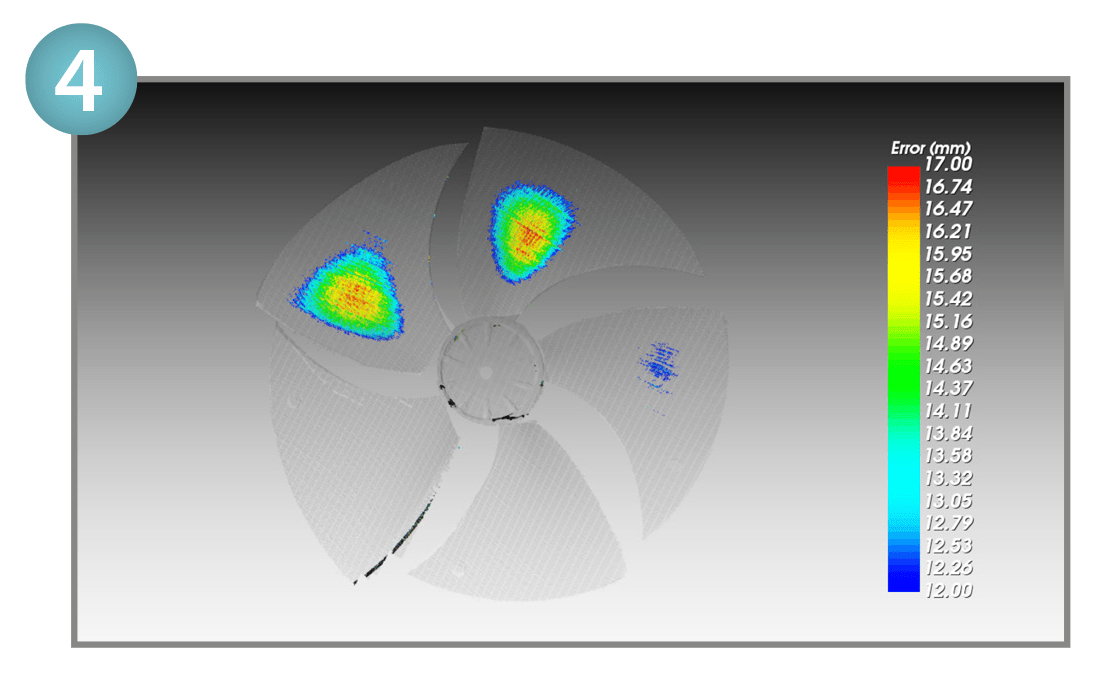
3D Matching Defect Inspection
The software will perform a comparison between the generated 3D point cloud data of the object and the standard CAD in real-time, generating a report according to the pre-set difference threshold. The report will contain the differences in height, width, and volume data. This data can also be used to automatically generate the robot path. This solution is suitable for object matching and deformation compensation applications.
Applications:
Inspection,Trimming,Repairing,Milling, and 3D Printing.
Software type |
|