YASKAWA HC DTP Series Use-Cases
Ranked Nr. 22 of 207 Cobots

- Precision Assembly Tasks: The HC20SDTP's short reach and high rigidity make it ideal for precise assembly applications where space is constrained, such as electronics assembly or small component assembly.
- Screw Fastening: Its robust design and integrated torque sensors support reliable and accurate screw fastening operations in confined spaces, ensuring consistent quality and safety.
- Compact Pick-and-Place Operations: The cobot's compact size and flexible mounting options enable effective pick-and-place tasks in tight environments, such as loading/unloading small parts or handling delicate items.
- Collaborative Handling in Confined Spaces: The HC20SDTP's collaborative capabilities allow it to work alongside human operators without additional safety barriers, making it suitable for tasks in narrow work areas where human-robot interaction is required.
Automated Palletizing with Yaskawa Motoman HC20 Cobot at Verla-Pharm
Problem
Verla-Pharm faced increasing throughput and logistics costs due to growing production demands. Their existing manual palletizing setup was inefficient and required modernization. They needed an automated solution that was easy to operate, required minimal space, and could integrate smoothly into their existing production environment.
Solution
The solution involved replacing the manual palletizing system with an automated cell featuring the Yaskawa Motoman HC20 cobot. The HC20 is designed for human-robot collaboration (HRC), allowing it to operate safely without a security fence. This cobot’s flexibility, compact design, and ease of integration made it ideal for the confined space at Verla-Pharm’s facility.
Outcome
The HC20 cobot successfully automated the palletizing process, handling cartons with a payload of up to 20 kg and a reach of 1,900 mm. It operates in a safe, slow mode and requires no additional protective measures, which saved space and costs. The system has been running smoothly, meeting Verla-Pharm’s expectations and proving to be a valuable asset in their production line. The successful implementation has also highlighted the potential of collaborative robots for future applications.
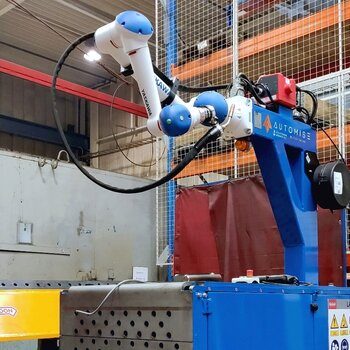
Ensuring Safe Operation of a Welding Cobot at Nooteboom Trailers through Comprehensive RI&E
Problem
The main challenge was to design a flexible cobot system that could move between locations while still maintaining safety standards. Traditional industrial robots, fixed in place, don't face this challenge. However, with a mobile cobot system like the HC-Series, the RI&E had to account for changing environments, ensuring safety across all potential work locations and conditions. This included safeguarding workers from welding hazards such as UV radiation, hot welding wires, and potential collisions.
Solution
Automise B.V., alongside Nooteboom's safety team, developed a two-part RI&E process. The first part assessed the cobot itself as an assembled machine, while the second part focused on each environment where the cobot might operate. Safety measures, including physical shields, welding screens, torque sensors, and controlled cobot speeds, were implemented to protect workers. Additionally, a checklist ensured that the new environment met safety standards before moving the cobot.
Outcome
With the RI&E properly executed and divided, the cobot system could be used safely across multiple locations. The system's safety features reduced risks, from harmful UV radiation to tripping hazards and potential injuries from welding wires. The cobot now operates efficiently, allowing Nooteboom to leverage its flexibility while maintaining full compliance with safety regulations. The approach ensured that both the cobot and its surroundings were safe for employees, minimizing the risk of industrial accidents.