Best Welding Tools 2024
By Qviro · August 9, 2024
Best 10 Welding Cobots of 2024:
UNIVERSAL ROBOTS UR20
Rating: 4.6/5 (41 Reviews)
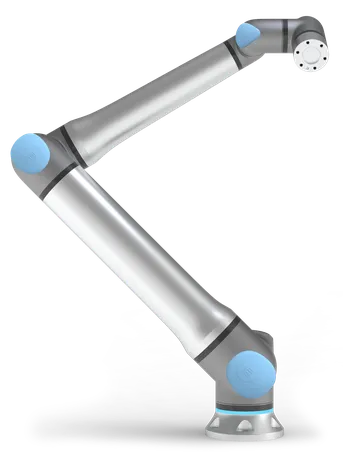
Description: Efficient palletizing robot with 1750 mm reach and 20 kg payload, designed for speed and adaptability.
Price: $57,000.00
Specs: Payload 20kg | Reach 1750mm
Read more about UR20
ABB GoFa 12
Rating: 4.7/5 (9 Reviews)
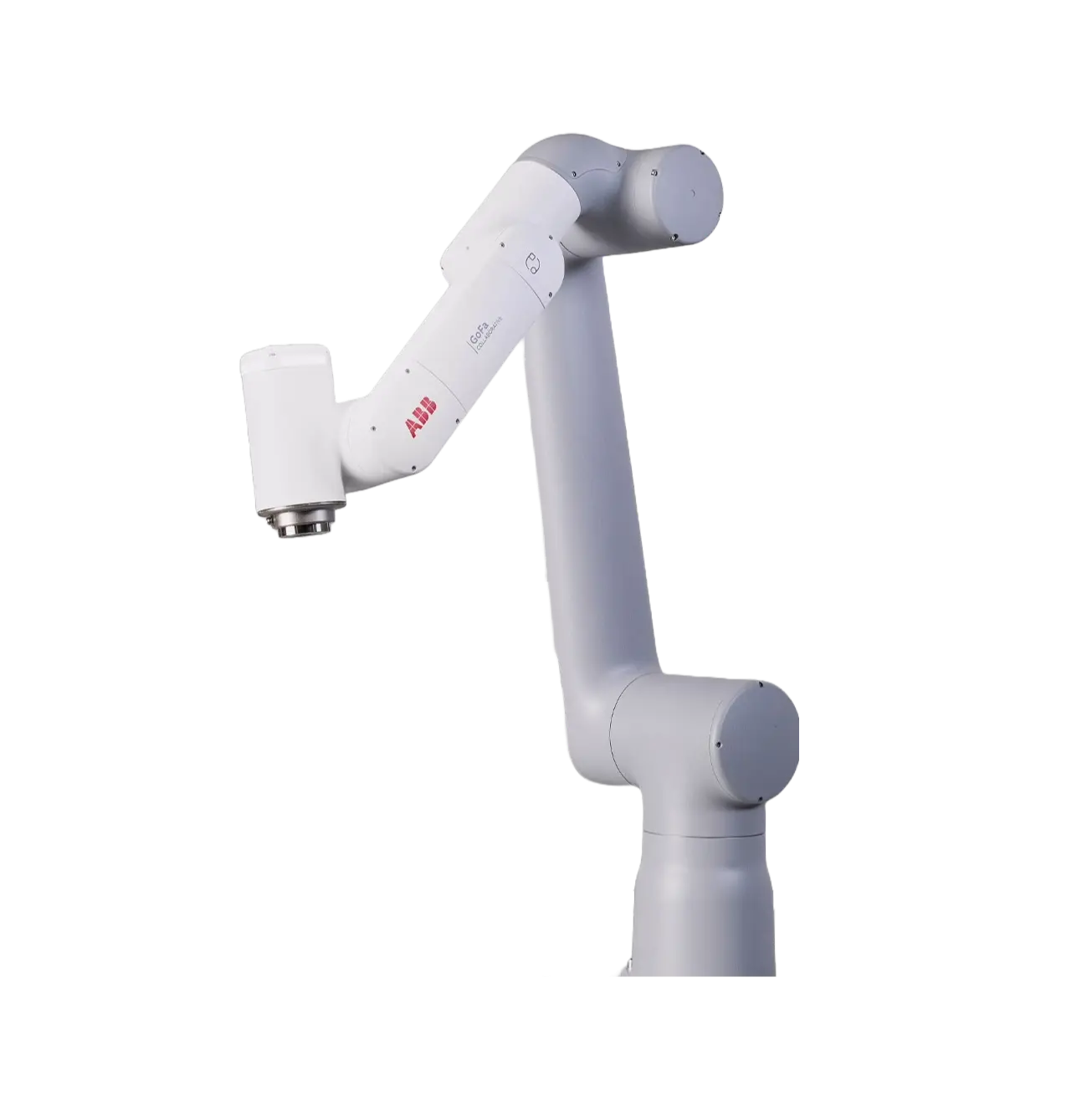
Description: Compact palletizing robot with 950 mm reach and 12 kg payload, ideal for handling small packages.
Specs: Payload 12kg | Reach 950mm
Read more about GoFa 12
Kinova Gen3 (7DoF)
Rating: 4.2/5 (12 Reviews)
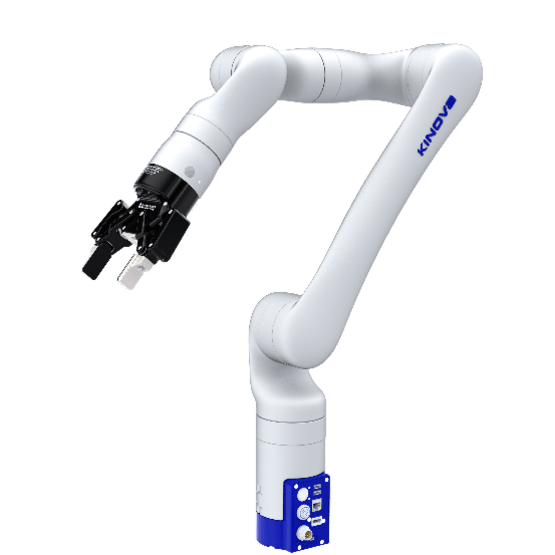
Description: Versatile collaborative robot with 915mm reach, 4kg payload. Suitable for research and light industrial tasks.
Specs: Payload 4kg | Reach 915mm
Read more about Gen3
Elephant Robotics MyCobot 320-M5
Rating: 4.0/5 (1 Review)
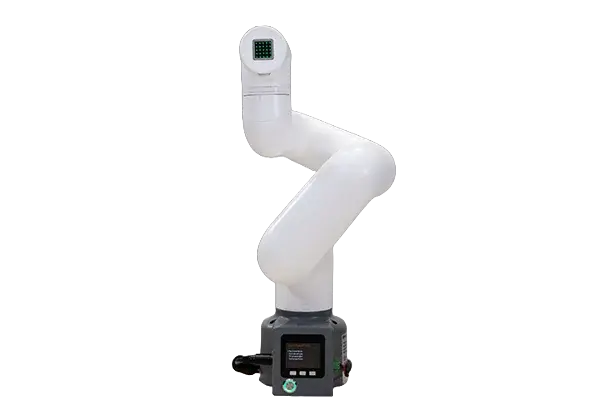
Description: Compact collaborative robot with 320mm reach, 1kg payload. Ideal for educational and light industrial applications.
Price: $2,399.00
Specs: Payload 1kg | Reach 320mm
Read more about MyCobot 320-M5
Yaskawa HC20DTP
Rating: 4.3/5 (12 Reviews)
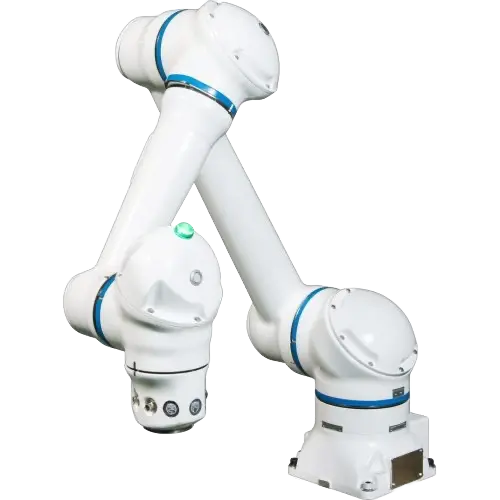
Description: 20 kg payload, 1700 mm reach; ideal for fast, safe palletizing with intuitive hand-guided programming.
Specs: Payload 20kg | Reach 1900mm
Read more about HC20DTP
FANUC CRX-25iA
Rating: 4.8/5 (5 Reviews)
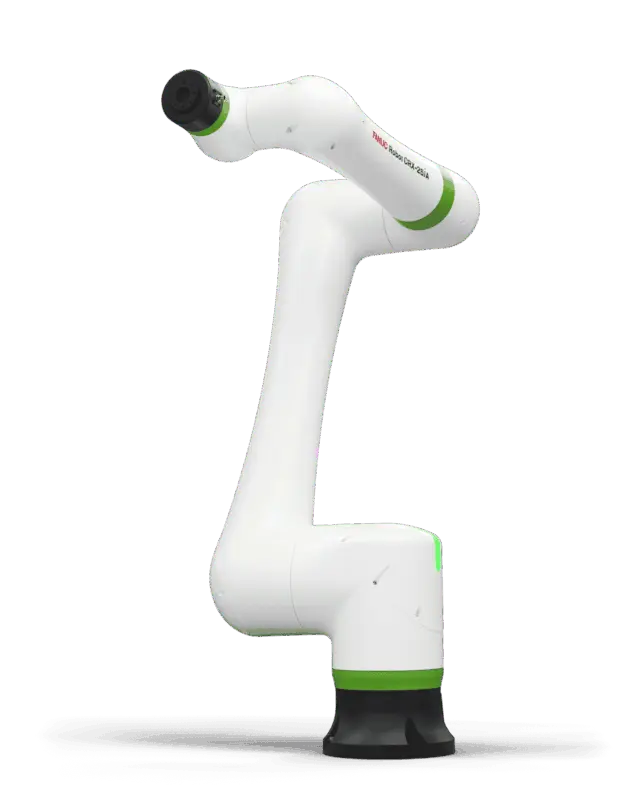
Description: Heavy-duty palletizing robot with 1889 mm reach and 25 kg payload, ideal for robust applications.
Specs: Payload 25kg | Reach 1889mm
Read more about CRX-25iA
Techman TM14
Rating: 4/5 (1 Review)
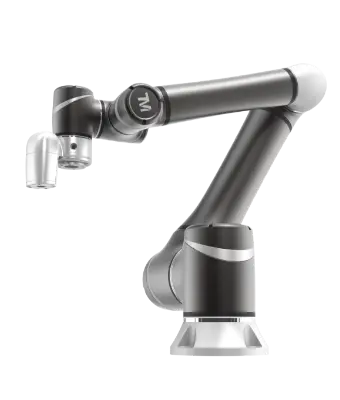
Description: Precision palletizing robot with 1100 mm reach and 14 kg payload, featuring an integrated vision system.
Specs: Payload 14kg | Reach 1100mm
Read more about TM14
Doosan H2017
Rating: 4.3/5 (2 Reviews)
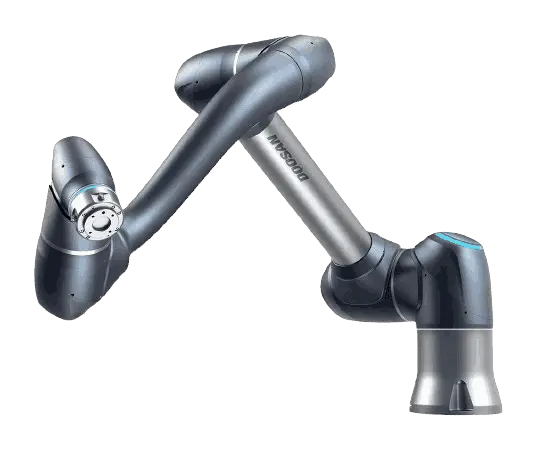
Description: Heavy-duty collaborative robot optimized for high-efficiency palletizing tasks. Features advanced safety systems and intuitive programming for seamless integration.
Specs: Payload 20kg | Reach 1700mm
Read more about H2017
KUKA LBR iiwa 14 R820
Rating: 4.6/5 (3 Reviews)
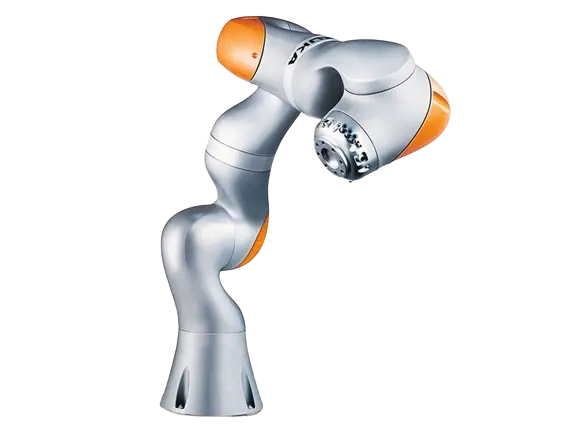
Description: Collaborative robot ideal for precise palletizing. Features sensitive control for safe human-robot collaboration.
Specs: Payload 14kg | Reach 820mm
Read more about LBR iiwa 14 R820
Kassow Robots KR1410
Rating: 4.6/5 (1 Review)
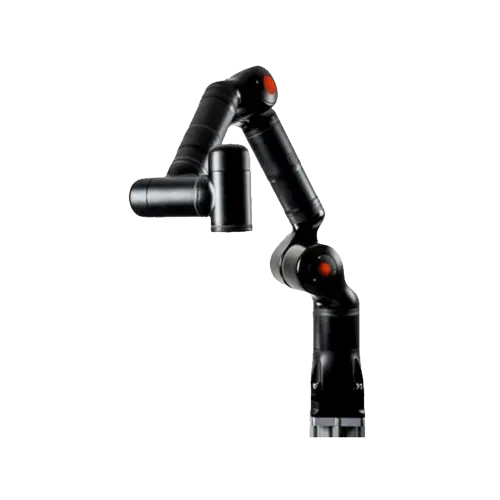
Description: Versatile collaborative robot with 850mm reach, 3kg payload. Great for light tasks.
Specs: Payload 3kg | Reach 850mm
Read more about the Robots KR810-3
Best 9 Welding Industrial Robots of 2024:
ABB IRB 6700
Rating: 4.6/5 (9 Reviews)
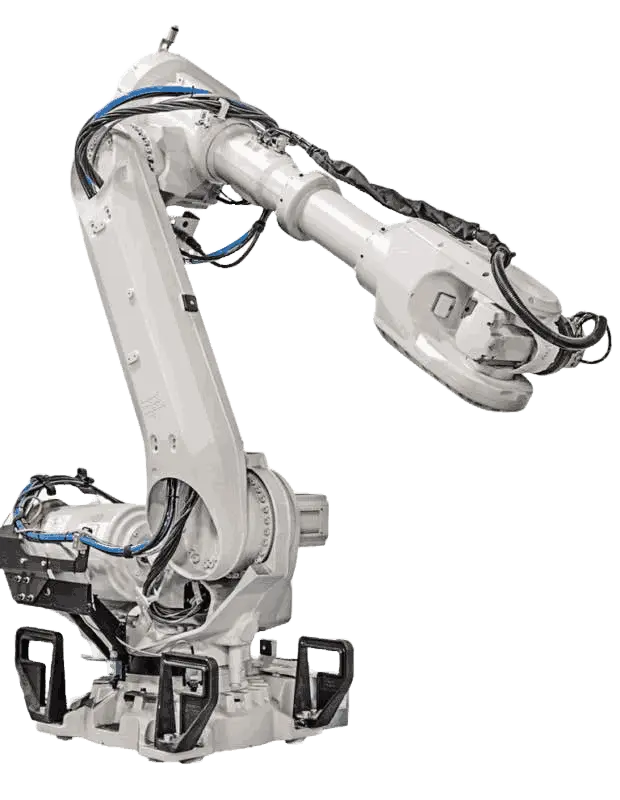
Description: Robust design with 150-300 kg payload and 2.6-3.2 m reach, ideal for welding and handling.
Specs: Payload 300kg | Reach 3200mm
Read more about IRB 6700
Stäubli TX2-60
Rating: 3.4/5 (2 Reviews)

Description: 6-axis robot with 4.5 kg payload and 670 mm reach, featuring SIL3-PLe safety options.
Specs: Payload 4.5kg | Reach 670mm
Read more about TX2-60
Comau NJ4-110-2.2
Rating: 4.5/5 (6 Reviews)
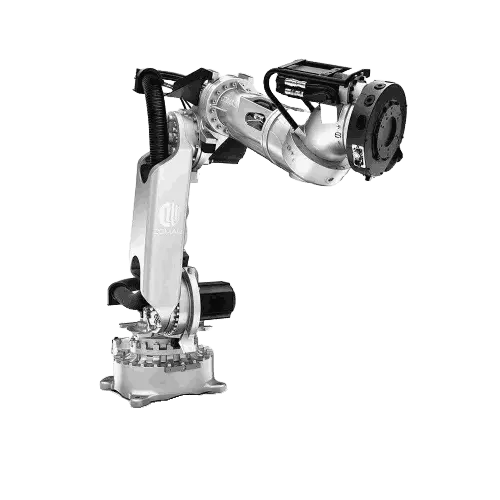
Description: Lean and compact design with 110 kg payload and 2210 mm reach, ensuring higher efficiency.
Specs: Payload 110kg | Reach 2210mm
Read more about NJ4-110-2.2
Kawasaki BX100L
Rating: 4.7/5 (1 Review)
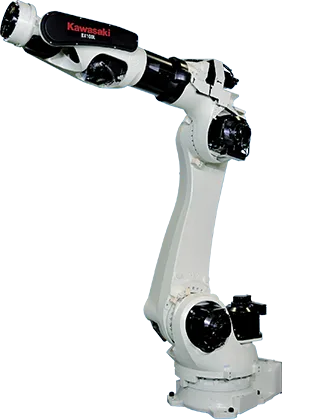
Description: Floor-mounted robot with 100 kg payload and 2597 mm reach, optimized for spot welding.
Specs: Payload 100kg | Reach 2597mm
Read more about BX100L
Omron Viper RL6-2066020
Rating: 4.3/5 (2 Reviews)
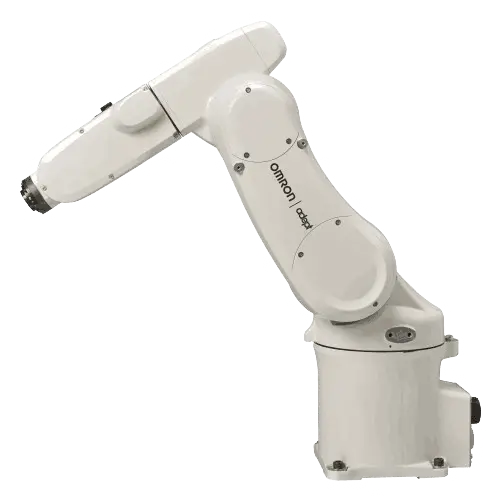
Description: 6-axis robot with 5 kg payload and 653 mm reach, ideal for machining and material handling.
Specs: Payload 5kg | Reach 653mm
Read more about Viper RL6-2066020
Nachi MZ07L
Rating: 5.0/5 (1 Review)
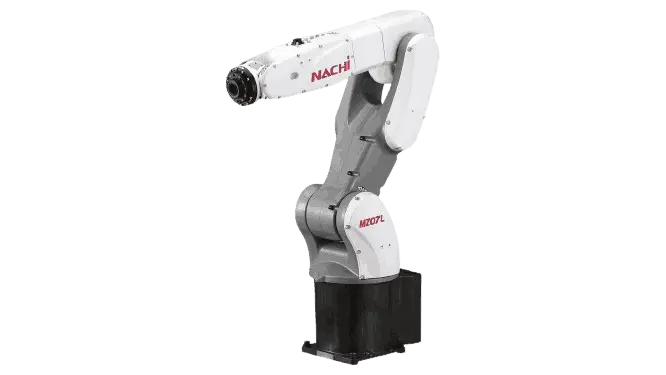
Description: Compact 6-axis robot with 7 kg payload and 912 mm reach, suitable for multiple mounting positions.
Specs: Payload 7kg | Reach 912mm
Read more about MZ07L
FANUC ARC Mate 50iD
Rating: 4.6/5 (1 Review)
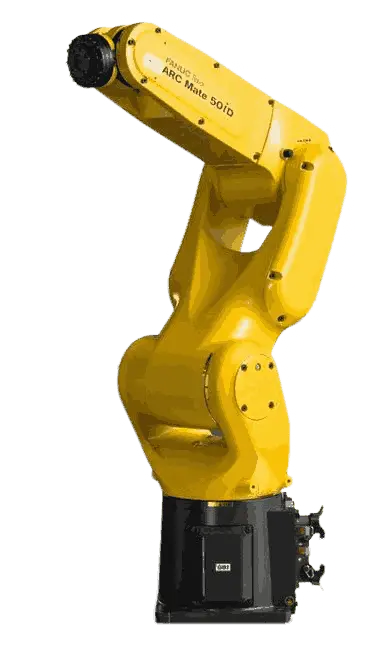
Description: 6-axis rugged robot with 7 kg payload and 717 mm reach, designed for welding in harsh environments.
Specs: Payload 7kg | Reach 717mm
Read more about ARC Mate 50iD
KUKA KR 150 R3100
Rating: 5.0/5 (1 Review)
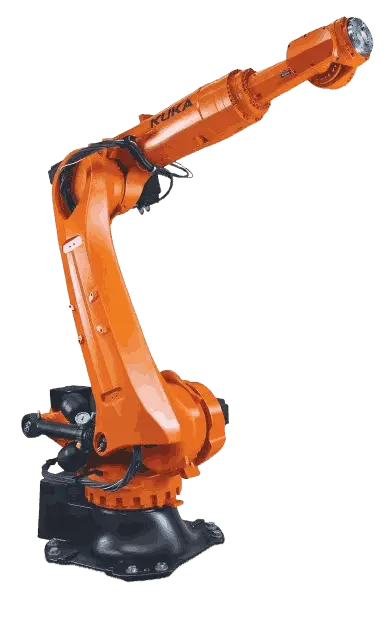
Description: 5-axis robot with 240 kg payload and 3195 mm reach, optimized for palletizing and material handling.
Specs: Payload 240kg | Reach 3195mm
Read more about KR 240 R3200 PA
Yaskawa GP25
Rating: 4.9/5 (3 Reviews)
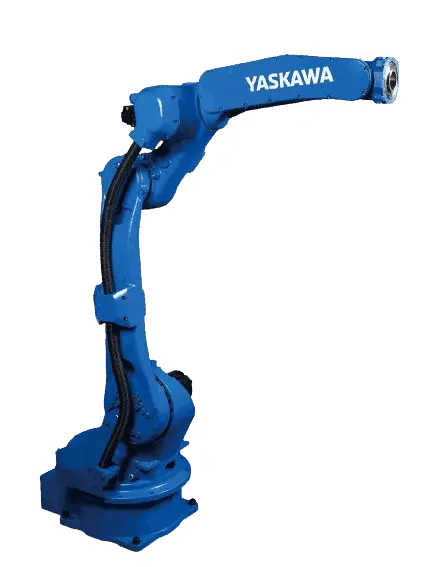
Description: Highly versatile 6-axis robot with 25 kg payload and 1730 mm reach, ideal for welding and handling.
Specs: Payload 25kg | Reach 1730mm
Read more about GP25
Why is Welding Important in Manufacturing?
Welding is essential in manufacturing because it helps build and repair many products you use every day. By joining materials like metals and thermoplastics, welding forms strong, permanent bonds. This process is crucial for creating everything from cars and airplanes to bridges and buildings. Without welding, assembling these complex structures would be much more difficult.
Welding provides strength and durability that bolting or adhesives can’t match, ensuring that the products you rely on are safe and dependable. It also allows for more flexibility in design, enabling manufacturers to create complex and innovative products. Additionally, welding is often faster and more cost-effective than other methods, which helps keep production costs down and makes products more affordable for you. In short, welding is key to manufacturing sturdy, efficient, and innovative products.
What are the Different Types of Welding Processes?
Welding comes in various forms, each suited for different materials and projects. Here are a few key types you might encounter:
MIG Welding (Metal Inert Gas):
This is like using a hot glue gun, but for metal. A wire feeds through a gun, melting to join pieces together. It’s great for beginners and versatile for many projects.
TIG Welding (Tungsten Inert Gas):
Picture an artist with a paintbrush, but instead of paint, they use a precise heat beam to fuse metal. It’s perfect for detailed work and strong, high-quality joins.
Stick Welding:
This method is like using a magic wand that releases sparks to meld metal. It’s rugged, works outdoors, and is good for heavy-duty repairs.
Flux-Cored Arc Welding:
Think of this as a hybrid between MIG and stick welding. It uses a special wire filled with flux, allowing it to work well in windy conditions and on dirty materials.
Each process has its own strengths, making welding a versatile tool for creating and fixing a wide range of products.
How Does Automation Impact Welding?
Automation has transformed welding, making it faster, more precise, and safer. Imagine robots doing the welding work – that’s automation in action.
Speed & Efficiency:
Automated welding machines work non-stop, much faster than humans, speeding up production. This means products can be made and repaired quicker, getting them into your hands faster.
Consistent Quality:
Robots are incredibly precise, delivering consistent welds every time. This uniform quality ensures that the items you use are reliable and durable.
Safety:
Welding can be dangerous, with risks from heat, sparks, and harmful fumes. Automation takes these tasks away from humans, reducing the risk of injuries in the workplace.
Cost-Effective:
Although setting up automated welding systems requires an initial investment, they save money in the long run by increasing efficiency, reducing waste, and cutting down on labor costs
Can Welding Be Performed On All Metals?
Welding can be done on many metals, but not all metals are easy to weld. The process depends on the metal’s properties, like melting point and reactivity. Here’s a quick look:
Metal Type | Description |
---|---|
Steel | Versatile and Strong: Steel is the most welded metal due to its versatility and strength. |
Aluminum | Lightweight but Tricky: Popular for its light weight, aluminum requires specific techniques because it conducts heat quickly. |
Stainless Steel | Corrosion Resistant: Widely used for its resistance to corrosion; welding needs control to avoid warping. |
Cast Iron | Brittle and Demanding: Requires pre- and post-heating processes to weld properly. |
Copper and Brass | High Temperature Needed: These metals need higher temperatures to weld and can be tricky because of their thermal conductivity. |
Titanium and Magnesium | Special Environments Required: Weldable but require special environments to prevent contamination. |
Lead and Zinc | Rarely Welded: Difficult to weld and generally not recommended due to health hazards and reactivity. |
How Do I Choose the Right Welding Process for My Project?
Choosing the right welding process for your project depends on a few key factors. Here’s how to decide:
Material Type:
Different metals require different welding techniques. For example, TIG welding is great for thin metals like aluminum, while MIG is versatile enough for both thin and thick materials.
Welding Position:
Some methods are more flexible than others. Stick welding works well in various positions, including overhead or vertical welding.
Weld Quality:
If your project needs a high-quality, clean weld, TIG welding is known for precision and neatness. MIG welding also provides strong welds with less cleanup.
Speed & Efficiency:
If you’re under time constraints, MIG welding is faster than TIG. Flux-cored arc welding is another fast option, especially for thicker materials.
Consider your project’s specific needs regarding the material, required strength, appearance of the weld, and how quickly you need the job done. Matching these requirements to the strengths of each welding type will guide you to the best choice
Selecting the right cobots for your business is important. You need to understand your specific requirements to make the best choice. This is where automation consulting can help. Qviro’s Alina is here to make the selection process easier. Alina offers expert guidance that is tailored to your needs.