- Linear Motion Systems
- ABB
- Electric linear unit IRBT 2005
- Specifications
ABB Electric linear unit IRBT 2005 Specifications
Ranked Nr. 3 of 33 Linear Motion Systems

Modular platform design
ABB’s Medium Track Motion (MTM)’s design is smart and compact with a symmetrical profile. Maximum integration ensures the protection of components in a small footprint.
The IRBT 2005 consists of a standard 1 meter long module that allows for the addition of numerous track and travel lengths for robots and transfer applications. The track’s modularity allows for product evolution during its entire life span. Adaptable to various environments, the IRBT 2005 is available in two variants, standard uncovered and fully covered.
Prepared for different process applications
The IRBT 2005 is available with multiple carriages - two for the robot and up to three for transfer applications. The robot track is available with additional carriage plates that allow them to carry the required equipment for specific applications such as Arc Welding and Sealing.
The internal cable chain of IRBT 2005 can be delivered pre-equipped with the suitable cables for different arc welding sources, or different customer power and signal cables. Each robot carriage has the option of being equipped with an empty external cable chain for additional application cables. Robot pedestals range from 250mm to 1000mm and can be selected as can robot orientations.
Outstanding speed and accuracy
ABB’s unique QuickMove™ and TrueMove are also critical to the MTM’s functionality. Together they guarantee optimal movement for the robot and the track with actual load. Path accuracy and speed are also optimized.
Type |
|
Max. Stroke | -21000 mm |
Min. Stroke | -1000 mm |
Extra info | Benefits: Path accuracy best in class / Compactness and modularity / Integrated and protected components / Prepared for different applications |
Electric linear unit IRBT 2005 Downloads
Electric linear unit IRBT 2005 Alternatives
See all 63 Linear Motion Systems

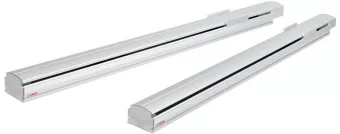
YAMAHA GF type Long stroke, High payload
Max. Stroke 2500mm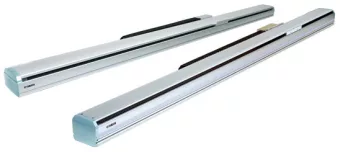
YAMAHA N type Nut rotation type model
Max. Stroke 2500mm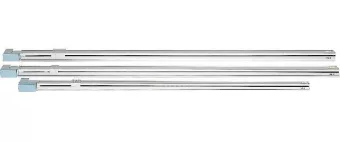
YAMAHA B type - Timing belt drive model
Max. Stroke 3050mm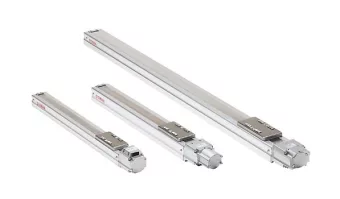
YAMAHA T type- Frameless structure model
Max. Stroke 1050mm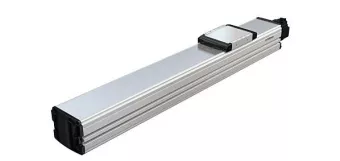
YAMAHA GX05L
Max. Stroke 800mm | Vertical Payload 12kg | Horizontal Payload 32kg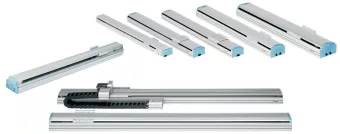
YAMAHA F type- High rigidity frame model
Max. Stroke 2050mm
HIWIN Electric linear axis KK series
Max. Stroke 1mm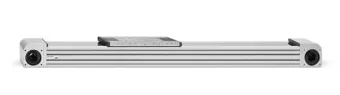
Camozzi Group Electric linear axis 5E series
Max. Stroke 6mm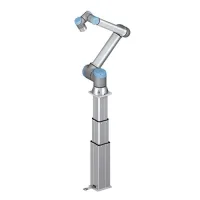
EWELLIX Ewellix Liftkit
Max. Stroke 500-900 mm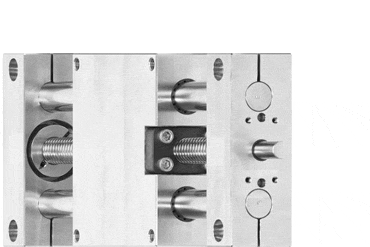
igus drylin® SHT linear systems with lead screw drive
Max. Stroke 250mm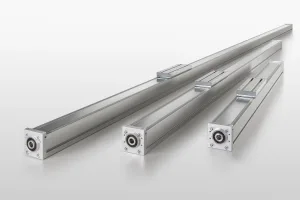