Peeters CoWelder Welding Cobot Alternatives & Competitors
Ranked Nr. 48 of 61 Turnkey Robot Solutions
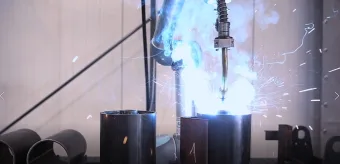
Top 10 CoWelder Welding Cobot Alternatives
- Qviro AUBO i10 SwitchWeld Station
- ABB Cobot Arc Welding Package
- Indeva Cobotics MyWelder Set
- ABB OmniVance™ Collaborative Arc Welding Cell
- Indeva Cobotics MoveFlex
- Peeters GoBot Palletise Solution

Qviro AUBO i10 SwitchWeld Station
The AUBO i10 SwitchWeld Station is a cobot-based welding solution tailored for users with limited experience in robotic welding. It leverages a simplified control interface, particularly the SwitchWeld Navigator Puck™, which enables precise robot positioning without the need for complex programming. The puck-based control system allows users to set up and execute welding tasks through just three buttons, streamlining the learning curve and increasing accessibility for operators. The system’s software further enhances efficiency by suggesting appropriate weld schedules based on project specifications, minimizing the need for manual adjustments.
With a payload capacity of 10 kg and a reach of 1350 mm, the AUBO i10 cobot in the SwitchWeld system is suited for medium-duty welding applications. Its repeatability of 0.03 mm ensures precision in tasks requiring consistent weld quality. The system is designed to integrate easily with existing welding tools and power supplies, allowing users to continue utilizing familiar equipment without additional investments in new hardware. The hardware bundle, including the necessary cables, mounting tools, and safety features, ensures that the cobot can be operational out of the box.
- No programming required: It only takes three buttons to program an entire welding project with the SwitchWeld Navigator puck.
- Easy to Understand User Interface: The SwitchWeld UI was designed in a way that is intuitive and simple for anyone to understand – regardless of robotic experience or training.
The primary applications for the AUBO i10 SwitchWeld Station include small- to medium-sized welding tasks in industries such as metal fabrication, automotive, and machinery production. Its ease of use, combined with a customizable setup, makes it ideal for operations looking to automate their welding processes without overhauling their existing workflows or investing in proprietary equipment.
Every SwitchWeld cobot welding bundle comes standard with all you’ll need to start welding, including:
- AUBO i-Series Cobot (i10 Cobot for this solution)
- AUBO Control Box
- AUBO Teach Pendant
- AUBO Cobot Cables and Adapters
- ATTC Lightning, Air Cooled MIG Welding Torch
- Welding Torch Mount
- SwitchWeld Navigator Puck & Cable
- SwitchWeld Mounting Tophat
- SwitchWeld 6 Depth of Field Joystick
- SwitchWeld Plugin Box & Labeled Wires
- SwitchWeld Safe Operation Console
- Safe Operation Console Connection Cables
- SwitchWeld Safety Whip Clamps
- SwitchWeld Welding Power Supply Connection Cable & Adapter
- SwitchWeld EZ Mount Base Plate
- SwitchWeld Installation Instructions
- SwitchWeld Software USB Hub & Flash Drive
- WiFi Hub for Software Installer
NAME | VALUE | UNIT |
---|---|---|
Robot Max Payload | 10 | kg |
Cobot max reach | 1350 | mm |
Repeatability | 0.03 | mm |
Mounting base footprint | Ø220 | mm |

ABB Cobot Arc Welding Package
The ABB Cobot Arc Welding Package simplifies welding tasks with its intuitive programming approach. It features the "Easy Teach Device," which allows users to guide the robot's arm along the welding path to generate programming code automatically. This lead-through programming significantly reduces the learning curve and setup time, making it accessible for users without extensive robotics experience.
The package is designed for high-mix, low-volume welding applications, where ease of use and flexibility are crucial. It can create and execute welding sequences in under 30 seconds, cutting programming time by up to 70 percent. The GoFa Cobot's high position accuracy and the Easy Teach Device's user-friendly interface ensure consistent weld quality.
Included in the package are all essential components: the robot, gripper, welding protective cover, wiring, and instructional materials. The Easy Teach Device, with its compact dimensions and dual screens for visual feedback, facilitates easy operation and programming by non-experts, ensuring a streamlined setup for collaborative welding applications.

Indeva Cobotics MyWelder Set
The set includes:
MyWelder software;
Doosan cobot – payload 9 kg – reach 1200 mm
o Doosan cobot – payload 6 kg – reach 1700 mm;
Esab welding machine.
Does not include:
welding bench;
final application certification.
Available welding trajectories:
ZIG-ZAG
Ability to control the wave amplitude and path speed of a period.
CIRCULAR
Possibility of modifying the two amplitudes and their respective speeds separately.
SINUOSOIDAL
Possibility of changing the amplitude and period.
TRAPEZOIDAL
It is possible to set a welding time from P1 to P2 and a different one for going from P2 to P1, as well as for accelerations, and it is possible to set a rest time after reaching the points.

ABB OmniVance™ Collaborative Arc Welding Cell
The ABB OmniVance™ Collaborative Arc Welding Cell is a turnkey solution for automating arc welding processes, designed to be accessible even to users without robotics programming experience. Pre-tested and fully integrated, this CE-certified cell includes a GoFa™ CRB 15000 collaborative robot, welding equipment, and ABB's ArcWare application software. Its standout feature is the Easy Teach Device, enabling users to program welding sequences quickly without coding expertise, reducing programming time by up to 70%.
This system combines high precision with industrial-grade software to deliver consistent weld quality, making it ideal for high-mix, low-volume production environments. Its flexibility allows operators to reprogram the cell easily for diverse welding tasks, addressing the needs of industries like manufacturing, automotive, and construction equipment. By automating simple welds, it enables manual welders to focus on complex or high-value work, boosting overall workforce efficiency.
Key elements of the OmniVance Collaborative Arc Welding Cell include a cobot-mounted Easy Teach Device, a safety fence, and a complete welding package comprising a torch, table, wire feeder, and power source. The cell offers an ideal solution for organizations aiming to address skilled labor shortages while enhancing productivity and maintaining high safety standards.

Indeva Cobotics MoveFlex
Solution consisting of the integration of a Doosan Cobot with an Automated Guided Vehicle (AGV).
This integration allows the handling of components over long distances, making the cobot’s range unlimited.
It is also possible to configure the robot to perform different operations along the way.
The use of a vision system eliminates positioning problems and gives the system maximum flexibility.
Cobots, AGVs and DC controllers are battery powered.

Peeters GoBot Palletise Solution
The cobot palletiser is the palletiser robot’s little brother. The cobot also automatically loads pallets with pre-packed products but is half the size of the larger version and easy to move around. We developed this cobot palletiser, named GoBot Palletise Solution, in-house.
COBOT PALLETISER IDEAL FOR SMES
Our GoBot Palletise Solution is the ideal (and often first) robot solution for small and medium-sized industrial companies that no longer want to manually stack goods coming off of the production line.
THE COBOT IS EASY TO HANDLE
(Pre)programming makes it easy for any employee to work with this cobot. No programming knowledge is required to set stacking patterns, for example. The cobot palletiser also stores each stacking pattern in its memory.
The cobot is equipped with motion sensors so people can work safely in its vicinity (changing pallets, for example, is not a problem)
Cobot Palletiser features:
- Product name:
- Application: Standard turnkey palletising cobot for light industrial palletising
- Capacity: up to 6 strokes per minute
- Maximum stacking height: 2 metres
- Voltage: 230 V
- Dimension: < 4 m2
- Cage: no
- Installation time: 1 day
- Force sensors: yes
- Change over time: minimum
- Maintenance: low
- Vision and line tracking: optional
- Energy consumption: low
- Delivery time: 4-6 weeks
- Programmed according to the ISO/TS-15066 standard
- Extra options:
> Malfunction data can be read out via Remote Support Router
> Lift unit for stacking up to 2 metres