SCHUNK PCFC Alternatives & Competitors
Ranked Nr. 121 of 116 End of Arm Tools
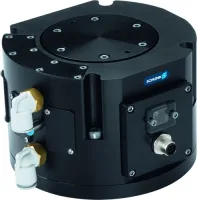
Top 10 PCFC Alternatives
- Bota Systems LaxONE
- Bota Systems MegaONE
- SCHUNK AOV
- Nordbo Robotics Active Compensation Unit
- Hypersen HPS-FT060E

Bota Systems LaxONE
Product mass 0.465kgThe Bota Systems LaxONE is an industrial-grade 6-axis force torque sensor that is designed to meet the demands of advanced applications in the robotics industry. With a lightweight construction and a payload capacity of up to 50kg, the LaxONE is ideal for use with robots that require end-of-arm tooling. The robust and stiff structure of the LaxONE makes it capable of withstanding high overload and cyclic load, while providing high sensitivity that makes it ideal for demanding applications such as sanding, polishing, deburring, precision assembly, and product testing.
The Bota Systems LaxONE offers the following features and benefits:
• All-in-One force torque sensor design
• ISO 9409-1-50-4-M6 mounting
• Compact and lightweight construction
• Embedded signal processing electronics
• 6 DoF IMU (available only with EtherCAT communication)
• 3 mounting flanges for 3D cameras and tools
• Measures on 6-axis
• Power supply of 7-48 V (5V for Serial/USB)
• Overload protection
• CE compliant
• Dustproof and water-resistant design
• Open-source software for TwinCAT, ROS, LabVIEW, and MATLAB®.

Bota Systems MegaONE
Product mass 1.386kgThe MegaONE is a compact and lightweight 6-axis force torque sensor designed for advanced industrial applications with robots that have a payload capacity of up to 120 kg. The sensor's robust and stiff structure can withstand high overload and cyclic load, while still providing high sensitivity, making it suitable for demanding tasks such as sanding, polishing, deburring, precision assembly, and product testing. With its integrated signal processing electronics, the MegaONE is easy to use and can be integrated into a variety of industrial robots, including those from ABB, Stäubli, Kuka, and more. The sensor also features a 6 DoF IMU for process monitoring and state estimation, as well as multiple mounting flanges for 3D cameras and tools.
Bota Systems MegaONE boasts the following features and benefits:
• An all-in-one force torque sensor design with ISO 9409-1-63-4-M8 mounting.
• Compact, lightweight construction for efficient utilization of robot payload.
• Embedded electronics for easy plug-and-play operation.
• A 6 DoF IMU for process monitoring and state estimation (only available with EtherCAT communication).
• 3 mounting flanges for 3D cameras and tools.
• Accurate 6-axis measurement.
• 7-48 V power supply (5V for Serial/USB).
• Overload protection for durability.
• CE compatibility.
• Dustproof and water-resistant design.
• Open-source software compatibility with TwinCAT, ROS, LabVIEW, and MATLAB®.

SCHUNK AOV
SCHUNK AOV is a pneumatic random orbit sander with axial compensation for grinding and polishing of workpiece surfaces.
Benefits:
Compensation can be adjusted by means of a double-action pneumatic cylinder
A constant contact pressure independent of the orientation of the tool.
Optional media change system
Automated exchange of grinding or polishing wheels.
Optional connection for suction
Reduced contamination and susceptibility to faults.
Flexibility in axial direction
Simplified robot programming.
Use of proven, adhesive grinding and polishing wheels
Simplified automation of manual grinding and polishing tasks.
Simple exchange of wear parts
Maximum system availability and minimum spare parts requirements.

Nordbo Robotics Active Compensation Unit
Product mass 2.6kgThe Nordbo Active Compensation unit (NAC) assures a constant applied force, regardless of the complexity of the surface curvature, processing speed and orientation of the tool. Sensors inside the product register the contact with the workpiece, keep the applied force constant and enable a soft landing to ensure that the part is not being over-processed while in first contact with the processing tool. The NAC can be used either as an end-of-arm tool on a robot or as a standalone component.
Consistent quality output
The pressure on the tool flange is actively kept constant on the configured force which results in an consistent and high quality output.
Increased productivity
Fast changes in curvature are compensated by the stroke of the NAC which enables an higher processing speed and results in an increased overall productivity of your processing application.
Easy configuration
Pressure and other settings are configurable through the integrated webserver which is accessible over ethernet using your laptop or phone.
Consistent force control
No matter of complexity of the surface curvature, this technology is able to automate both operations sensitive to contact, and applications with various tolerance levels, in a simple, reliable and economical manner, in turn offering our clients a powerful tool to increase competitiveness on the market.
One robot, multiple tasks
The NAC is designed for both as an end-of-arm mount on a robot or as a standalone component. The rectangular shape offers easy and stable installation possibilities. The compact design makes NAC the lightest compensation unit on the market with a total weight of only 2.6 kg.

Hypersen HPS-FT060E
Product mass 0.255kgHypersen's HPS-FT060E is a high-performance force and torque sensor designed to measure forces and torques on three spatial axes of XYZ. It is equipped with a high-performance processor and 24-bit ADC, ensuring accurate and reliable data collection. The sensor has a high SNR digital output and provides a 2000Hz output data rate, which is suitable for high-speed applications. The device has a high static overload protection and can withstand forces and torques up to 350% of its maximum rated measurement range without damage.
The HPS-FT060E has a low zero drift & cross-axis effect, and low temperature drift, which ensures the accuracy of the sensor over time. It is available with Ethernet, EtherCAT, Analog, and RS-485 communication, making it compatible with a variety of applications. The device is suitable for use in industrial robots, collaborative robots, factory automation, and more.
The sensor has a measuring range of ±600N for the Fxy axis, ±800N for the Fz axis, and ±15Nm for the Mxy and Mz axes. The precision of the device is 0.2N for the Fxy axis, 0.4N for the Fz axis, and 0.002Nm for the Mxy and Mz axes. The device has an overload limit of 350% of its maximum rated measurement range for all axes of force and moment measurement. The HPS-FT060E has a protection class of IP65 and a hysteresis of 0.1% F.S. The non-linearity is less than 1.25%, and creep is less than 2%. The signal noise is 0.03N for the Fxy axis, 0.12N for the Fz axis, and 0.001N for the Mxy and Mz axes. The crosstalk is less than 2% F.S. for all axes of measurement. The sensor weighs 255g and has a size of 877828.5mm.