YAMAHA Dust-proof and drip-proof SCARA robots Alternatives & Competitors
Ranked Nr. 1 of 163 SCARA Robots
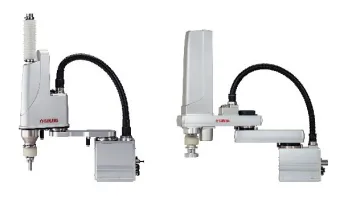
Top 10 Dust-proof and drip-proof SCARA robots Alternatives
- YAMAHA Small type SCARA robots YK-XG
- YAMAHA Tiny SCARA robots - Extra small
- YAMAHA Large type SCARA robots YK-XG
- YAMAHA Wall-mount and inverse type SCARA robots
- TM Robotics TH1050A
- DENSO HS-035/045/055A1

YAMAHA Small type SCARA robots YK-XG
Reach 250-400 mm | Payload 5kgFEATURES:
01. Internal structure achieving the high-rigidity and high-accuracy.
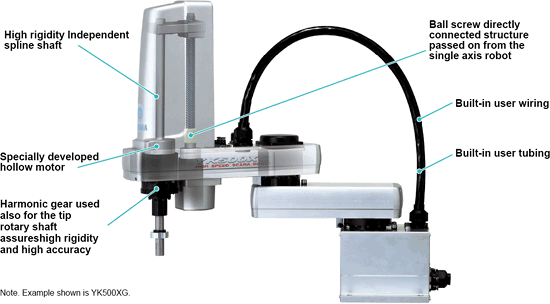
02. Completely beltless structure
A totally beltless structure was achieved by using a ZR axis direct coupling structure. This direct drive structure drastically reduces wasted motion. It also maintains high accuracy over a long period of time. It ensure maintenance-free usage for extended periods with no worries about belt breakage, stretching or deterioration with age (feature applies to all XG series models and the YK180X/YK220X).
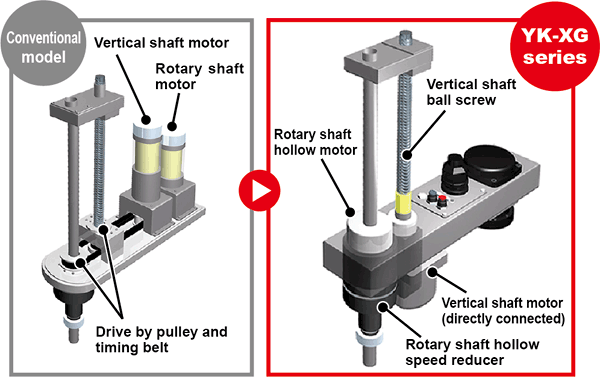
03. High Speed
The standard cycle time is fast of course but the YAMAHA design also stresses tact time in the actual usage region. A drastic improvement in maximum speed was made by changing the gear ratio and maximum motor rpm. This also resulted in a better tact time during long distance movement.
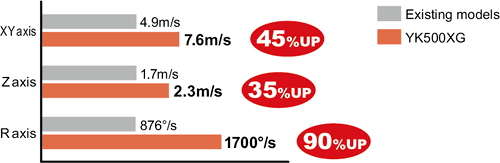
04. Improved maintenance features
The covers on the YAMAHA SCARA robot YK-XG series can be removed from the front or upwards. The cover is separate from the cable so maintenance tasks are easy.
On ordinary robots replacing the grease on the harmonic gear takes a great deal of time and trouble because the gear must be disassembled and position deviations might occur. On YAMAHA SCARA robots however the harmonic gear is the grease-sealed type so no grease replacement is needed (YK-500XG to YK1000XG).
05. Robot R axis inertia moment capacity
SCARA robot performance is not limited to just standard cycle time. Actual work situations include a diverse range of heavy work pieces as well as work with large offsets. Using a low R axis inertia moment in those cases will help drastically cut the cycle time. All YAMAHA SCARA robots have a speed reducer directly coupled to the tip of the rotating axis. The R axis produces an extremely high allowable inertia moment which delivers high speed operation compared to structures where positioning is usually done by a belt after decelerating.
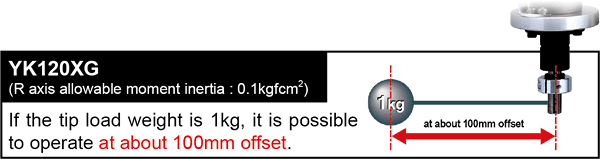
R axis allowable inertia moment : Comparing YK120XG with competitor's models
A large inertia is generated when the offset from the R axis to the load center is large and this can severely restrict the acceleration during operation.
The allowable inertia moment on the YAMAHA XG series is exceedingly large compared to other company SCARA robots in the same class and so can operate at high speed even with a work offset.
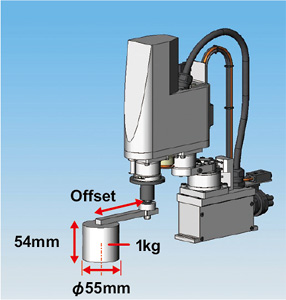
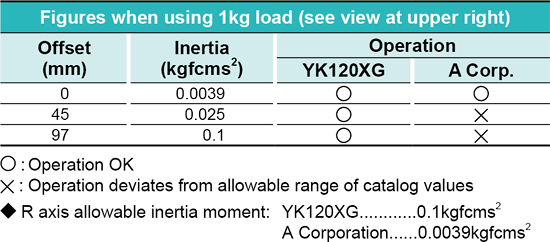
06. Compact
Changing the cable layout made the overall cable height lower than the unit cover.
Also, utilizing a motor with a small overall length and extrusion material base yielded the smallest dimensions among equipment in the same class.
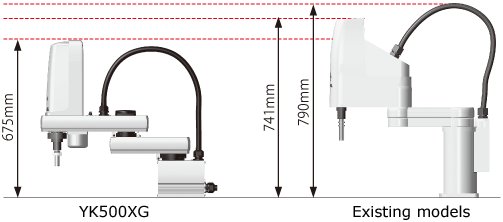
07. Environmentally rugged resolver provides closed loop control
The position detector is a resolver. The resolver has a simple yet strong structure using not electronic components or elements and so has great features such as being extremely tough in harsh environments as well as a low breakdown rate. The resolver structure has none of the detection problems that occur in other detectors such as optical encoders whose electronic components breakdown or suffer from moisture or oil that sticks to the disk. Moreover, mechanical specifications for both absolute and incremental specifications are common to all controllers so one can switch to either absolute or incremental specifications just by setting a parameter.
Also even if the absolute battery is completely worn down, the SCARA can operate on incremental specifications so in the unlikely event of trouble one can feel secure knowing that there will be no need to stop the production line. The backup circuit has been completely renovated and now has a backup period extending to 1 year.
Note. The resolver has a simple structure not using electronic components at all. It is highly resistant to low and high temperatures, impacts, electrical noise, dust particles, oil, etc. and is used in automobiles, trains, and airplanes.
08. Zone control (=Automatically sets the maximum acceleration/deceleration) function
On SCARA robots there is a large difference in the load applied to the motor and the speed reducer depending on whether the robot arm is folded or extended. YAMAHA SCARA robots however can automatically set an optimal maximum acceleration and deceleration using the arm status when starting operation and the arm status when ending operation. This capability means that just entering the initial payload will prevent the robot from exceeding tolerance values for motor peak torque and speed reducer allowable peak torque. So full power can be extracted from the motor whenever needed and a high level of acceleration/deceleration maintained.
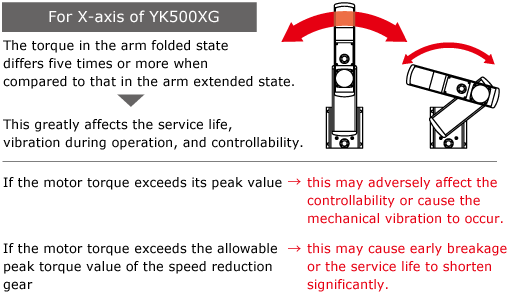
Note.A motor torque that exceeds the peak value will cause bad effects on robot controllability and cause mechanical vibration. Also, exceeding the speed reducer allowable peak torque value will cause early stage robot breakdowns and lead to a drastic drop in the robot service life span.
09. Hollow shaft and tool flange options are selectable
Useful options include a hollow shaft for easy wiring to the tip tool and a tool flange for tool clamping.
* YK250XG/YK350XG/YK400XG/YK500XGL/YK600XGL
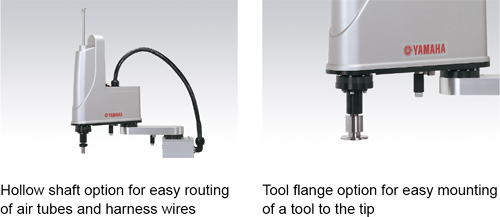
10. History of 30 years
The first YAMAHA robots were SCARA robots. Since the first SCARA robot called "CAME" was produced in 1979, some 30 years of SCARA robot innovations have continually appeared. These SCARA robots have undergone countless modifications in an everchanging marketplace and amassed a hefty record of successful products making them an essential part of the YAMAHA robot lineup.
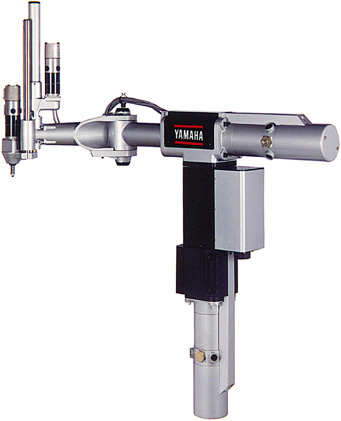

YAMAHA Tiny SCARA robots - Extra small
Reach 120-220 mm | Payload 1-5 kgFEATURES:
01. Internal structure achieving the high-rigidity and high-accuracy.
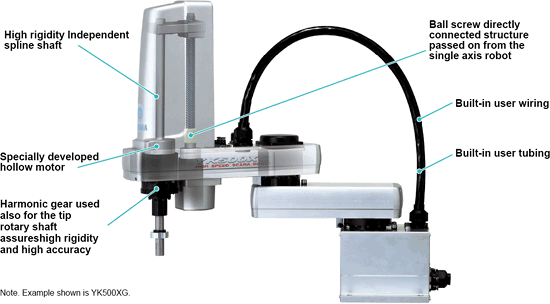
02. Completely beltless structure
A totally beltless structure was achieved by using a ZR axis direct coupling structure. This direct drive structure drastically reduces wasted motion. It also maintains high accuracy over a long period of time. It ensure maintenance-free usage for extended periods with no worries about belt breakage, stretching or deterioration with age (feature applies to all XG series models and the YK180X/YK220X).
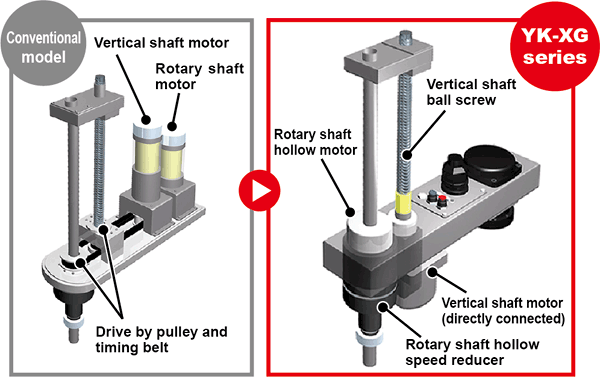
03. High Speed
The standard cycle time is fast of course but the YAMAHA design also stresses tact time in the actual usage region. A drastic improvement in maximum speed was made by changing the gear ratio and maximum motor rpm. This also resulted in a better tact time during long distance movement.
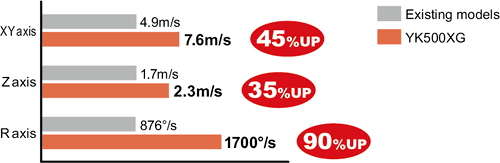
04. Improved maintenance features
The covers on the YAMAHA SCARA robot YK-XG series can be removed from the front or upwards. The cover is separate from the cable so maintenance tasks are easy.
On ordinary robots replacing the grease on the harmonic gear takes a great deal of time and trouble because the gear must be disassembled and position deviations might occur. On YAMAHA SCARA robots however the harmonic gear is the grease-sealed type so no grease replacement is needed (YK-500XG to YK1000XG).
05. Robot R axis inertia moment capacity
SCARA robot performance is not limited to just standard cycle time. Actual work situations include a diverse range of heavy work pieces as well as work with large offsets. Using a low R axis inertia moment in those cases will help drastically cut the cycle time. All YAMAHA SCARA robots have a speed reducer directly coupled to the tip of the rotating axis. The R axis produces an extremely high allowable inertia moment which delivers high speed operation compared to structures where positioning is usually done by a belt after decelerating.
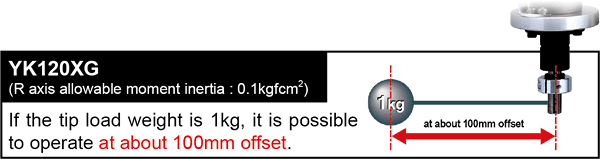
R axis allowable inertia moment : Comparing YK120XG with competitor's models
A large inertia is generated when the offset from the R axis to the load center is large and this can severely restrict the acceleration during operation.
The allowable inertia moment on the YAMAHA XG series is exceedingly large compared to other company SCARA robots in the same class and so can operate at high speed even with a work offset.
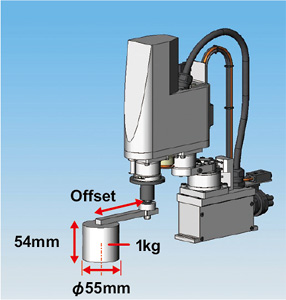
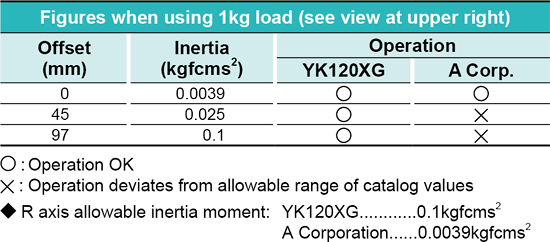
06. Compact
Changing the cable layout made the overall cable height lower than the unit cover.
Also, utilizing a motor with a small overall length and extrusion material base yielded the smallest dimensions among equipment in the same class.
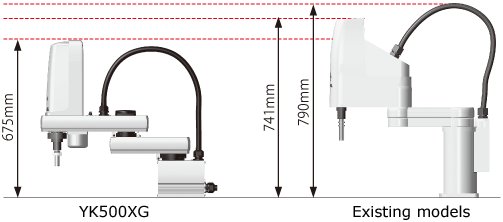
07. Environmentally rugged resolver provides closed loop control
The position detector is a resolver. The resolver has a simple yet strong structure using not electronic components or elements and so has great features such as being extremely tough in harsh environments as well as a low breakdown rate. The resolver structure has none of the detection problems that occur in other detectors such as optical encoders whose electronic components breakdown or suffer from moisture or oil that sticks to the disk. Moreover, mechanical specifications for both absolute and incremental specifications are common to all controllers so one can switch to either absolute or incremental specifications just by setting a parameter.
Also even if the absolute battery is completely worn down, the SCARA can operate on incremental specifications so in the unlikely event of trouble one can feel secure knowing that there will be no need to stop the production line. The backup circuit has been completely renovated and now has a backup period extending to 1 year.
Note. The resolver has a simple structure not using electronic components at all. It is highly resistant to low and high temperatures, impacts, electrical noise, dust particles, oil, etc. and is used in automobiles, trains, and airplanes.
08. Zone control (=Automatically sets the maximum acceleration/deceleration) function
On SCARA robots there is a large difference in the load applied to the motor and the speed reducer depending on whether the robot arm is folded or extended. YAMAHA SCARA robots however can automatically set an optimal maximum acceleration and deceleration using the arm status when starting operation and the arm status when ending operation. This capability means that just entering the initial payload will prevent the robot from exceeding tolerance values for motor peak torque and speed reducer allowable peak torque. So full power can be extracted from the motor whenever needed and a high level of acceleration/deceleration maintained.
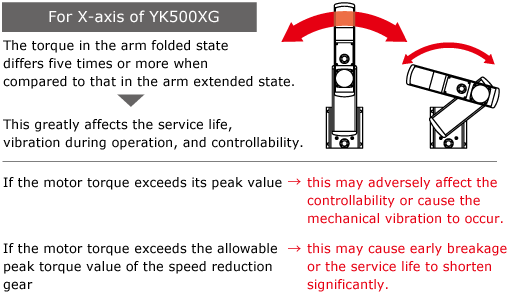
Note.A motor torque that exceeds the peak value will cause bad effects on robot controllability and cause mechanical vibration. Also, exceeding the speed reducer allowable peak torque value will cause early stage robot breakdowns and lead to a drastic drop in the robot service life span.
09. Hollow shaft and tool flange options are selectable
Useful options include a hollow shaft for easy wiring to the tip tool and a tool flange for tool clamping.
* YK250XG/YK350XG/YK400XG/YK500XGL/YK600XGL
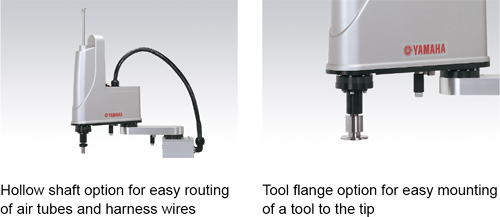
10. History of 30 years
The first YAMAHA robots were SCARA robots. Since the first SCARA robot called "CAME" was produced in 1979, some 30 years of SCARA robot innovations have continually appeared. These SCARA robots have undergone countless modifications in an everchanging marketplace and amassed a hefty record of successful products making them an essential part of the YAMAHA robot lineup.
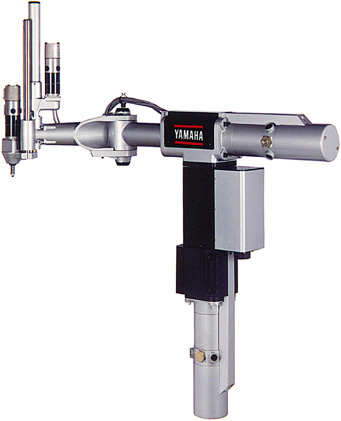

YAMAHA Large type SCARA robots YK-XG
Reach 700-1200 mm | Payload 10-50 kg01 Internal structure achieving the high-rigidity and high-accuracy.
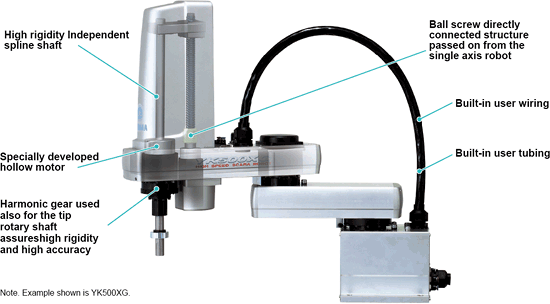
02 Completely beltless structure
A totally beltless structure was achieved by using a ZR axis direct coupling structure. This direct drive structure drastically reduces wasted motion. It also maintains high accuracy over a long period of time. It ensure maintenance-free usage for extended periods with no worries about belt breakage, stretching or deterioration with age (feature applies to all XG series models and the YK180X/YK220X).
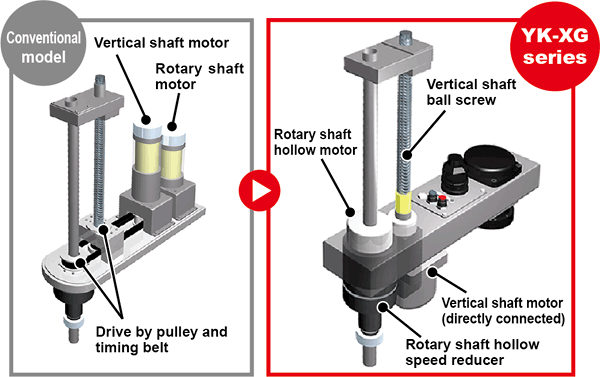
03 High speed
The standard cycle time is fast of course but the YAMAHA design also stresses tact time in the actual usage region. A drastic improvement in maximum speed was made by changing the gear ratio and maximum motor rpm. This also resulted in a better tact time during long distance movement.
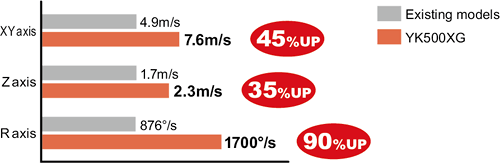
04 Improved maintenance features
The covers on the YAMAHA SCARA robot YK-XG series can be removed from the front or upwards. The cover is separate from the cable so maintenance tasks are easy.
On ordinary robots replacing the grease on the harmonic gear takes a great deal of time and trouble because the gear must be disassembled and position deviations might occur. On YAMAHA SCARA robots however the harmonic gear is the grease-sealed type so no grease replacement is needed (YK-500XG to YK1000XG).
05 Robot R axis inertia moment capacity
SCARA robot performance is not limited to just standard cycle time. Actual work situations include a diverse range of heavy work pieces as well as work with large offsets. Using a low R axis inertia moment in those cases will help drastically cut the cycle time. All YAMAHA SCARA robots have a speed reducer directly coupled to the tip of the rotating axis. The R axis produces an extremely high allowable inertia moment which delivers high speed operation compared to structures where positioning is usually done by a belt after decelerating.
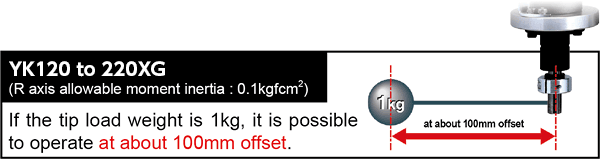
R axis allowable inertia moment : Comparing YK120XG with competitor's models
A large inertia is generated when the offset from the R axis to the load center is large and this can severely restrict the acceleration during operation.
The allowable inertia moment on the YAMAHA XG series is exceedingly large compared to other company SCARA robots in the same class and so can operate at high speed even with a work offset.
Figures when using 1kg load (see view at upper right)
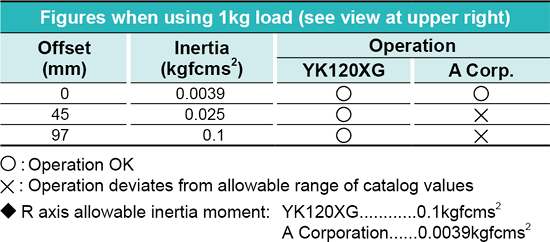
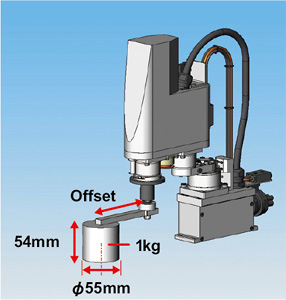
06 Compact
Changing the cable layout made the overall cable height lower than the unit cover.
Also, utilizing a motor with a small overall length and extrusion material base yielded the smallest dimensions among equipment in the same class.
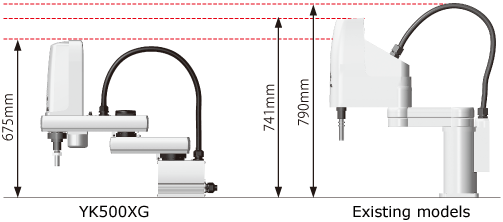
07 Environmentally rugged resolver provides closed loop control
The position detector is a resolver. The resolver has a simple yet strong structure using not electronic components or elements and so has great features such as being extremely tough in harsh environments as well as a low breakdown rate. The resolver structure has none of the detection problems that occur in other detectors such as optical encoders whose electronic components breakdown or suffer from moisture or oil that sticks to the disk. Moreover, mechanical specifications for both absolute and incremental specifications are common to all controllers so one can switch to either absolute or incremental specifications just by setting a parameter.
Also even if the absolute battery is completely worn down, the SCARA can operate on incremental specifications so in the unlikely event of trouble one can feel secure knowing that there will be no need to stop the production line. The backup circuit has been completely renovated and now has a backup period extending to 1 year.
Note. The resolver has a simple structure not using electronic components at all. It is highly resistant to low and high temperatures, impacts, electrical noise, dust particles, oil, etc. and is used in automobiles, trains, and airplanes.
08 Zone control (=Automatically sets the maximum acceleration/deceleration) function
On SCARA robots there is a large difference in the load applied to the motor and the speed reducer depending on whether the robot arm is folded or extended. YAMAHA SCARA robots however can automatically set an optimal maximum acceleration and deceleration using the arm status when starting operation and the arm status when ending operation. This capability means that just entering the initial payload will prevent the robot from exceeding tolerance values for motor peak torque and speed reducer allowable peak torque. So full power can be extracted from the motor whenever needed and a high level of acceleration/deceleration maintained.
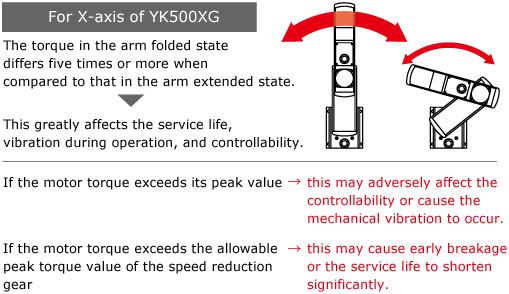
Note. A motor torque that exceeds the peak value will cause bad effects on robot controllability and cause mechanical vibration. Also, exceeding the speed reducer allowable peak torque value will cause early stage robot breakdowns and lead to a drastic drop in the robot service life span.
09 Hollow shaft and tool flange options are selectable
Useful options include a hollow shaft for easy wiring to the tip tool and a tool flange for tool clamping.
*YK250XG/YK350XG/YK400XG/YK500XGL/YK600XGL
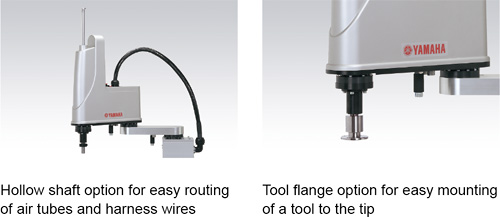
10 History of 30 years
The first YAMAHA robots were SCARA robots. Since the first SCARA robot called "CAME" was produced in 1979, some 30 years of SCARA robot innovations have continually appeared. These SCARA robots have undergone countless modifications in an everchanging marketplace and amassed a hefty record of successful products making them an essential part of the YAMAHA robot lineup.
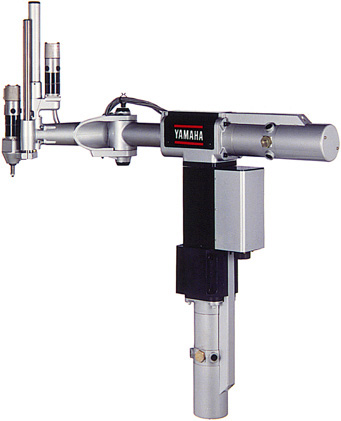

YAMAHA Wall-mount and inverse type SCARA robots
Reach 300-1000 mm | Payload 3-20 kgAs the ceiling installation or the wall installation is used, the robot installation space that could not be used conventionally can be utilized efficiently.
01 Hanging type is renewed. Completely beltless structure and high rigidity
As the conventional hanging type is changed to the wall mount type, the flexibility of the system design is improved. The production equipment can be downsized. Additionally, as an inverse type that allows upward operation is also added to the product lineup, the flexibility of the working direction is widened. Furthermore, use of a completely beltless structure achieves a maximum payload of 20 kg and a R-axis tolerable moment of inertia of 1 kgm2* that are the top in the class. A large hand can also be installed. So, this robot is suitable for heavy load work.
*YK700XGS to YK1000XGS
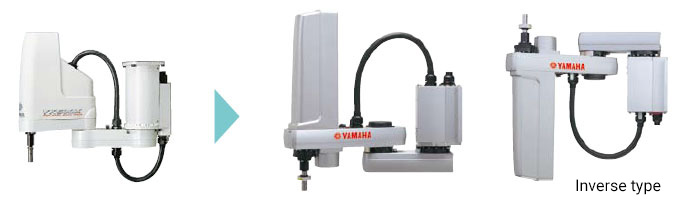
02 Internal structure achieving the high-rigidity and high-accuracy.
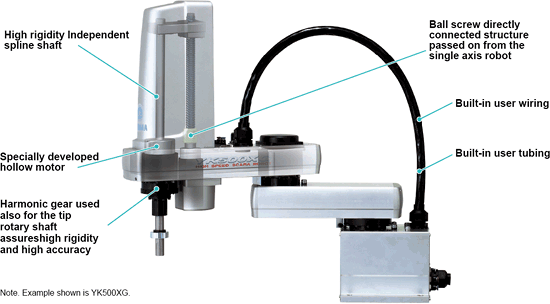
03 Completely beltless structure
A totally beltless structure was achieved by using a ZR axis direct coupling structure. This direct drive structure drastically reduces wasted motion. It also maintains high accuracy over a long period of time. It ensure maintenance-free usage for extended periods with no worries about belt breakage, stretching or deterioration with age (feature applies to all XG series models and the YK180X/YK220X).
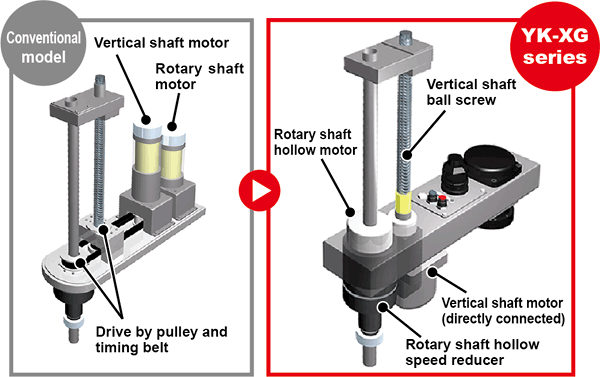
04 High speed
The standard cycle time is fast of course but the YAMAHA design also stresses tact time in the actual usage region. A drastic improvement in maximum speed was made by changing the gear ratio and maximum motor rpm. This also resulted in a better tact time during long distance movement.
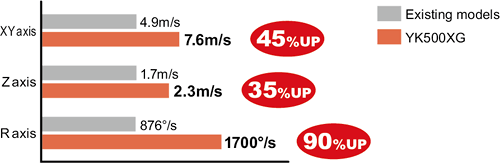
05 Improved maintenance features
The covers on the YAMAHA SCARA robot YK-XG series can be removed from the front or upwards. The cover is separate from the cable so maintenance tasks are easy.
On ordinary robots replacing the grease on the harmonic gear takes a great deal of time and trouble because the gear must be disassembled and position deviations might occur. On YAMAHA SCARA robots however the harmonic gear is the grease-sealed type so no grease replacement is needed (YK-500XG to YK1000XG).
06 Robot R axis inertia moment capacity
SCARA robot performance is not limited to just standard cycle time. Actual work situations include a diverse range of heavy work pieces as well as work with large offsets. Using a low R axis inertia moment in those cases will help drastically cut the cycle time. All YAMAHA SCARA robots have a speed reducer directly coupled to the tip of the rotating axis. The R axis produces an extremely high allowable inertia moment which delivers high speed operation compared to structures where positioning is usually done by a belt after decelerating.
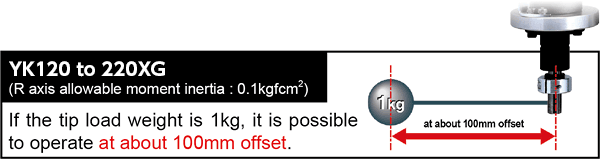
R axis allowable inertia moment : Comparing YK120XG with competitor's models
A large inertia is generated when the offset from the R axis to the load center is large and this can severely restrict the acceleration during operation.
The allowable inertia moment on the YAMAHA XG series is exceedingly large compared to other company SCARA robots in the same class and so can operate at high speed even with a work offset.
Figures when using 1kg load (see view at upper right)
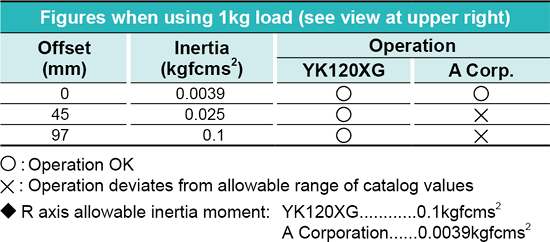
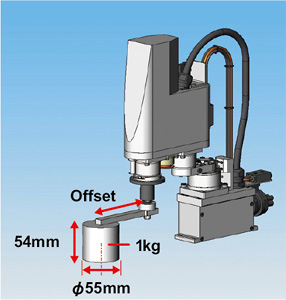
07 Compact
Changing the cable layout made the overall cable height lower than the unit cover.
Also, utilizing a motor with a small overall length and extrusion material base yielded the smallest dimensions among equipment in the same class.
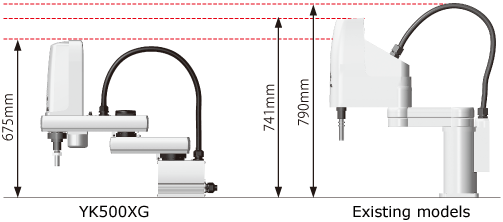
08 Environmentally rugged resolver provides closed loop control
The position detector is a resolver. The resolver has a simple yet strong structure using not electronic components or elements and so has great features such as being extremely tough in harsh environments as well as a low breakdown rate. The resolver structure has none of the detection problems that occur in other detectors such as optical encoders whose electronic components breakdown or suffer from moisture or oil that sticks to the disk. Moreover, mechanical specifications for both absolute and incremental specifications are common to all controllers so one can switch to either absolute or incremental specifications just by setting a parameter.
Also even if the absolute battery is completely worn down, the SCARA can operate on incremental specifications so in the unlikely event of trouble one can feel secure knowing that there will be no need to stop the production line. The backup circuit has been completely renovated and now has a backup period extending to 1 year.
Note. The resolver has a simple structure not using electronic components at all. It is highly resistant to low and high temperatures, impacts, electrical noise, dust particles, oil, etc. and is used in automobiles, trains, and airplanes.
09 Zone control (=Automatically sets the maximum acceleration/deceleration) function
On SCARA robots there is a large difference in the load applied to the motor and the speed reducer depending on whether the robot arm is folded or extended. YAMAHA SCARA robots however can automatically set an optimal maximum acceleration and deceleration using the arm status when starting operation and the arm status when ending operation. This capability means that just entering the initial payload will prevent the robot from exceeding tolerance values for motor peak torque and speed reducer allowable peak torque. So full power can be extracted from the motor whenever needed and a high level of acceleration/deceleration maintained.
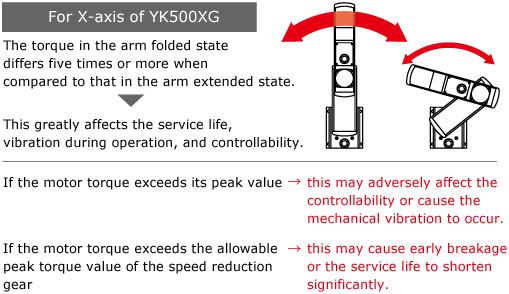
Note.A motor torque that exceeds the peak value will cause bad effects on robot controllability and cause mechanical vibration. Also, exceeding the speed reducer allowable peak torque value will cause early stage robot breakdowns and lead to a drastic drop in the robot service life span.
10 Hollow shaft and tool flange options are selectable
Useful options include a hollow shaft for easy wiring to the tip tool and a tool flange for tool clamping.
*YK250XG/YK350XG/YK400XG/YK500XGL/YK600XGL
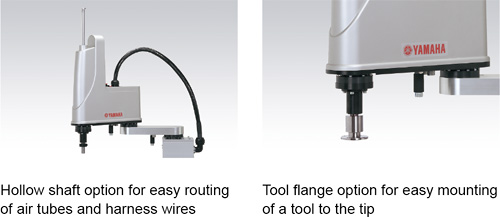
11 History of 30 years
The first YAMAHA robots were SCARA robots. Since the first SCARA robot called "CAME" was produced in 1979, some 30 years of SCARA robot innovations have continually appeared. These SCARA robots have undergone countless modifications in an everchanging marketplace and amassed a hefty record of successful products making them an essential part of the YAMAHA robot lineup.
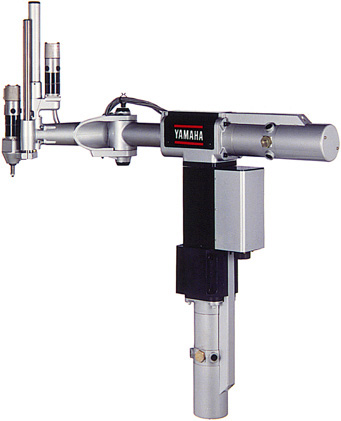

TM Robotics TH1050A
Reach 1050mm | Repeatability 0mm | Payload 20kgThe TH1050A SCARA robot has an arm length of 1050mm, and a maximum payload capacity of 20kg.
The TH1050A is made with a labyrinth structure offering dust protection both inside and out, making it the perfect solution for all applications with a dust-free environment.
Product Features & Benefits:
Heavy duty arm
Rigid arm structure
Highest payload in its class
Up to 20kg payload
Arm lengths from 180 to 1200mm
Ideal for end of line packaging and assembly work

DENSO HS-035/045/055A1
Reach 350-550 mm | Repeatability 0mm | Payload 5kgThe HS-A1 Series of robots are next-generation SCARA robots that are faster and more accurate than the HS Series of robots while having inherited their advantages.
Total arm length|350 / 450 / 550 mm
Vertical stroke(Z)|100・150・200・320mm
Maximum payload|5kg
Cycle time|0.29 sec
Higher speed
The HS-A1 Series of robots maximize motor performance with the latest RC8A controller, improving the standard cycle time to 0.29 seconds.
Higher accuracy
By dynamically reflecting the conditions of the arms into robot controlling, vibration of the robot can be damped in a short time. Suppressing vibration at the time of high-speed conveyance and residual vibration improves accuracy.
A wide choice of options is offered.
The dust-proof, mist-proof type; the clean type; the overhead-mounted type; and the UL-listed configuration model(1)are offered, helping achieve automation in various installation environments.
- (1) The UL-listed configuration model is scheduled to be released in 2017.