ATI Industrial Automation Robotic Collision Sensors Alternatives & Competitors
Ranked Nr. 128 of 116 End of Arm Tools
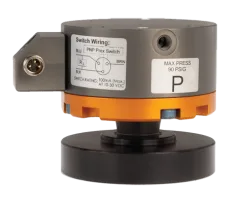
Top 10 Robotic Collision Sensors Alternatives
- Bota Systems PixONE
- RAD Pneumatic Stainless Steel
- RAD Pneumatic High-Angle
- RAD Spring-Loaded
- Hypersen HPS-FT060E
- Applied Robotics QS QUICKSTOP™ COLLISION SENSORS FOR WELDING AND PLASMA CUTTING
- Applied Robotics QS QUICKSTOP™ COLLISION SENSORS
- Hypersen HPS-FT060S
- Hypersen HPS-FT-EN2000-IO
- RAD Pneumatic Spring-Assist
- Hypersen HPS-FT120

Bota Systems PixONE
Payload 250kgThe Bota Systems PixONE is a novel through-hole force-torque sensor designed primarily for robotic applications. Its standout feature is the innovative hollow shaft design, which allows for the integration between a robot's arm and its end-of-arm tooling (EOT). This integration facilitates internal cable routing, which is increasingly preferred by robotic arm manufacturers to prevent cable tangles and movement restrictions, thus enhancing both robot agility and operational safety.
In terms of physical design, the PixONE is distinguished by its minimalistic two-piece structure, which significantly reduces the sensor's weight—making it 30% lighter than other sensors in the market. This reduction in weight is crucial for dynamic robotic systems where additional mass can limit speed and efficiency. Additionally, this streamlined design simplifies the assembly process, further reducing the complexity and potential downtime in industrial settings.
From a technical and operational standpoint, the PixONE is versatile and robust, equipped with an integrated Inertial Measurement Unit (IMU) and a high durability rating of IP67, making it waterproof and suitable for diverse environments. The sensor is available in multiple models, with external diameters starting at just 60mm and through-hole diameters at 15mm. Moreover, it supports high-speed data communication via EtherCAT technology and features Power over Ethernet (PoE) for simplified electrical installations, making it a highly adaptable solution for a broad range of robotic applications, from industrial manufacturing to sensitive medical procedures.

RAD Pneumatic Stainless Steel
The Stainless Steel Ultimatic™ Collision Sensor is RAD’s patented mechanical collision sensor that:
- Stops the robot* within 2 to 10ms of a collision to minimize costly damage to the robot arm and/or tooling. RAD’s collision sensor provides protection even if the robot arm itself is not moving.
- Absorbs the crash energy without releasing the air pressure in the collision sensor. Keeping the air in the collision sensor prevents tooling ‘sag’ and eliminates the effects of compressed air being released into the environment.
- Automatically resets to within ± 0.0005″ (0.013mm) in x, y, and z dimensions and to within ± 0.017º rotationally to maximize uptime and eliminate the need for human intervention.
- Resists corrosion and is able to be cleaned due to its stainless steel construction.
- Offers 8º of angular compliance (please see RAD’s Pneumatic High-Angle Collision Sensor for information on collision sensors with 13º of angular compliance).
- Allows pneumatic adjustment so the user can easily change the amount of resistance the unit must encounter before signaling a collision.
- Has a compliance adjustment feature that lets the user determine the amount of deflection allowed before a signal is sent to the robot’s E-stop or controller.
Robotic Collision Sensors provide robot crash protection and safety by mechanically detecting when the robot arm* has encountered an obstruction, absorbing the crash energy, and quickly stopping the robot to prevent costly damage to the robot arm and tooling.
Operating Principle
RAD’s Stainless Ultimatic™ Collision Sensor works by establishing the minimal points of contact required to restrain all degrees of freedom (movement) in normal operation. When a robotic crash occurs, external forces upset this balance thereby allowing angular, rotational, or compressive compliance. This motion opens a normally closed switch and sends a signal to your robot’s E-stop or controller.
Note: The Stainless Steel Ultimatic™ Collision Sensor can be used as a compliance (alignment) device rather than a collision sensor by simply mounting the unit without wiring it to the robot. Please see the Compliance Device section for more end-effector compliance options.

RAD Pneumatic High-Angle
The Pneumatic High-Angle Ultimatic™ Collision Sensor is RAD’s patented mechanical collision sensor that:
- Stops the robot* within 2 to 6ms of a collision to minimize costly damage to the robot and/or tooling. RAD’s collision sensor provides protection even if the robot itself is not moving.
- Offers a full 13° of angular compliance – 63% more than the original Ultimatic™ Pneumatic Collision Sensor model
- Absorbs the crash energy without releasing the air pressure in the unit thus preventing tooling ‘sag’ and eliminating the effects of compressed air being released into the environment.
- Automatically resets to within ± 0.0005″ (0.013mm) in x, y, and z dimensions and to within ± 0.017º rotationally to maximize uptime and eliminate the need for human intervention.
- Allows pneumatic adjustment so the user can easily change the amount of resistance the unit must encounter before signaling a collision.
- Has a compliance adjustment feature that lets the user determine the amount of deflection allowed before a signal is sent to your robot’s E-stop or controller.
Operating Principle
RAD’s Pneumatic High-Angle Ultimatic™ Collision Sensor works by establishing the minimal points of contact required to restrain all degrees of freedom (movement) in normal operation. When a collision occurs, external forces upset this balance thereby allowing angular, rotational, or compressive compliance. This motion opens a normally closed switch and sends a signal to your robot’s E-stop or controller.
Note: The Pneumatic High-Angle Ultimatic™ Collision Sensor can be used as a compliance (alignment) device by installing the unit without connecting the sensor switch. Please see the Compliance Devices section for more end-effector compliance options.

RAD Spring-Loaded
The Uni-Coupler™ Collision Sensor is RAD’s patented, spring-loaded, mechanical collision sensor that:
- Stops the robot* in the event of a crash to minimize costly damage to the robot and/or tooling. RAD’s collision sensor provides protection even if the robot itself is not moving.
- Absorbs the crash energy by allowing up to 15º of deflection following a collision.
- Automatically resets to within ± 0.002″ (0.051mm) to maximize uptime and eliminate the need for human intervention.
- Allows up to 0.040″ (1.02mm) “give” in the coupling before the load sensing mechanism is activated (in compliant models) to avoid nuisance tripping.
Operating Principle
RAD’s Uni-Coupler™ Collision Sensor is a spring-loaded mechanical device that signals your robot’s E-stop or controller when the tooling encounters an obstruction. The lateral or vertical force applied during a collision opens a normally closed switch that sends the “stop” signal.
Note: The Uni-Coupler™ Collision Sensor can be used as a compliance device by installing the unit without connecting the sensor switch.
* can also be used on linear actuators, pick & place machines, and other automated equipment.

Hypersen HPS-FT060E
Product mass 0.255kgHypersen's HPS-FT060E is a high-performance force and torque sensor designed to measure forces and torques on three spatial axes of XYZ. It is equipped with a high-performance processor and 24-bit ADC, ensuring accurate and reliable data collection. The sensor has a high SNR digital output and provides a 2000Hz output data rate, which is suitable for high-speed applications. The device has a high static overload protection and can withstand forces and torques up to 350% of its maximum rated measurement range without damage.
The HPS-FT060E has a low zero drift & cross-axis effect, and low temperature drift, which ensures the accuracy of the sensor over time. It is available with Ethernet, EtherCAT, Analog, and RS-485 communication, making it compatible with a variety of applications. The device is suitable for use in industrial robots, collaborative robots, factory automation, and more.
The sensor has a measuring range of ±600N for the Fxy axis, ±800N for the Fz axis, and ±15Nm for the Mxy and Mz axes. The precision of the device is 0.2N for the Fxy axis, 0.4N for the Fz axis, and 0.002Nm for the Mxy and Mz axes. The device has an overload limit of 350% of its maximum rated measurement range for all axes of force and moment measurement. The HPS-FT060E has a protection class of IP65 and a hysteresis of 0.1% F.S. The non-linearity is less than 1.25%, and creep is less than 2%. The signal noise is 0.03N for the Fxy axis, 0.12N for the Fz axis, and 0.001N for the Mxy and Mz axes. The crosstalk is less than 2% F.S. for all axes of measurement. The sensor weighs 255g and has a size of 877828.5mm.

Applied Robotics QS QUICKSTOP™ COLLISION SENSORS FOR WELDING AND PLASMA CUTTING
Product mass 0.45-3.72 kg
The QuickSTOPTM is a dynamically variable collision sensor that operates on an air pressure system – and provides excellent protection in machine load/unload robotics applications.
A regulated air supply provides positive, variable pressure to hold the collision sensor rigid during normal operation. At impact, the air chamber seal is opened, immediately signaling the system controller.
Advantages
- Dynamically variable trip points
- Permanent repeatability
- Detects angular, rotational and compressive forces

Applied Robotics QS QUICKSTOP™ COLLISION SENSORS
Product mass 0.11-16.8 kgThe QuickSTOPTM is a dynamically variable collision sensor that operates on an air pressure system – and provides excellent protection in machine load/unload robotics applications.
A regulated air supply provides positive, variable pressure to hold the collision sensor rigid during normal operation. At impact, the air chamber seal is opened, immediately signaling the system controller.
Advantages:
- Dynamically variable trip points
- Permanent repeatability
- Detects angular, rotational and compressive forces

Hypersen HPS-FT060S
Payload 25kg | Product mass 0.502kgHypersen's HPS-FT060S is a high-performance force and torque sensor designed for industrial applications. It is capable of measuring force and torque on three spatial axes of XYZ, making it a valuable tool for a variety of industries. The sensor is equipped with a high-performance processor and 24-bit ADC, which ensures a high signal-to-noise ratio (SNR) digital output, making it suitable for use in demanding industrial environments.
The HPS-FT060S sensor is designed to provide high static overload protection, ensuring reliable and accurate measurement even under challenging conditions. With a 2000Hz output data rate, the sensor can provide real-time measurements, which is particularly useful for applications that require quick responses.
The sensor has low zero drift and cross-axis effect, making it ideal for applications that require precise and accurate measurements. It also has low temperature drift, which ensures that the sensor's accuracy is maintained even in varying temperatures.
The HPS-FT060S is available with Ethernet, EtherCAT, and RS-485 communication interfaces, making it easy to integrate into different systems. The sensor is suitable for use in industrial robots, collaborative robots, factory automation, and other similar applications.
In terms of technical parameters, the HPS-FT060S has a measuring range of ±1000N (Fxy), ±1400N (Fz), ±30Nm (Mxy), and ±30Nm (Mz), with a precision of 0.5N (Fxy), 0.5N (Fz), 0.004Nm (Mxy), and 0.004Nm (Mz). The sensor has a weight of 502g and a size of 877828.5mm, making it compact and easy to handle. It operates within a temperature range of -10~55°C and requires a power supply of 12-24V, consuming 0.5w. The sensor has an external connector type of an anti-fall aviation plug and a protection class of IP65. The sensor has a hysteresis of 0.1(%F.S.), non-linearity of <1.25%, and overload of 350%. The signal noise is 0.04N (Fxy), 0.14 (Fz), 0.001N (Mxy), and 0.002N (Mz), with crosstalk of <2(%F.S).
In conclusion, Hypersen's HPS-FT060S is a high-performance force and torque sensor that is suitable for use in industrial applications. With its high static overload protection, low zero drift, and cross-axis effect, and low temperature drift, the sensor can provide reliable and accurate measurements even in challenging environments. Its high output data rate, communication interfaces, and compact size make it an ideal tool for use in industrial robots, collaborative robots, and factory automation systems.

Hypersen HPS-FT-EN2000-IO
Product mass 0.073kgHypersen's HPS-FT-EN2000-IO is a highly efficient 6D force and torque sensor that can convert RS485 interface to Ethernet(100M) network interface. This sensor supports TCP and UDP communication protocols and measures the six components of force and torque. It comes with integrated functions like signal conditioning, data acquisition and more, making it highly versatile for different applications.
With support for up to 2000Hz data output frequency, HPS-FT-EN2000-IO is highly efficient and can be configured with multiple types of adjustable digital filters. Additionally, users can also configure the sensor coordinate system as per their requirements.
One of the notable features of this sensor is its real-time IO alarm function, which allows for multi-axis configurable alarm threshold. Furthermore, the HPS-FT-EN2000-IO is compatible with binary and ASCII command analysis modes, making it highly suitable for embedded systems and robot control systems.
The HPS-FT-EN2000-IO is commonly used in a wide range of applications, including industrial robots, collaborative robots, medical robots, wind tunnel testing and more. It is highly reliable and comes with a compact size of 70.8 * 55.35 * 24.65 mm and a weight of 73g, making it highly convenient to use.
In terms of technical specifications, the HPS-FT-EN2000-IO has an operating temperature range of -10~55 degrees Celsius and a power requirement of 0.5W. It is a highly efficient and reliable force and torque sensor suitable for various industries and applications.

RAD Pneumatic Spring-Assist
RAD’s Spring-Assist Ultimatic™ Pneumatic Collision Sensor minimizes the potential for costly damage to the robot arm or tooling in the event of a crash and maximizes uptime by automatically returning to within 0.0005″ (0.013mm) of its starting position once it has been separated from the source of the crash.
NOTE: RAD Spring-Assist Ultimatic™ Collision Sensors effectively replace the discontinued EOA MultiClutch Breakaway Safety Devices.
The Spring-Assist Ultimatic™ Collision Sensor is RAD’s patented mechanical collision sensor that:
- Sends a signal to the system’s E-stop or controller within 4 to 10ms of a collision to minimize costly damage to equipment and/or tooling. RAD’s collision sensor provides protection even if the system itself is not moving.
- Absorbs the crash energy without loss of air pressure in the collision sensor. Keeping the air in the collision sensor prevents tooling “sag” and eliminates the effects of compressed air being released into the environment.
- Resets Automatically to within ± 0.0005″ (0.013mm) in X, Y, and Z dimensions and to within ± 0.017º rotationally to maximize uptime and eliminate the need for human intervention.
- Increases Payload Capacity to nearly double that of RAD’s standard U-4622 with no increase in size
- Maintains significant resistance even with no air pressure, reducing tooling sag if air pressure is lost
- Provides angular, rotation and axial (compressive) compliance
- Allows pneumatic adjustment so the user can easily change the amount of resistance the unit must encounter before signaling a collision.
- Has a compliance adjustment feature that lets the user determine the amount of deflection allowed before a signal is sent to the robot’s E-stop or controller.
Operating Principle
RAD’s Spring-Assist Ultimatic™ Collision Sensor works by establishing the minimal points of contact required to restrain all degrees of freedom (movement) in normal operation. When a robotic crash occurs, external forces upset this balance thereby allowing angular, rotational or compressive compliance. This motion opens a normally closed switch and sends a signal to your robot’s E-stop or controller.
Note: The Spring-Assist Ultimatic™ Collision Sensor can be used as a compliance (alignment) device rather than a collision sensor by simply mounting the unit without wiring it to the robot. Please see the Compliance Device section for more end-effector compliance options.