Elephant Robotics mechArm 270-Pi Alternatives & Competitors
Ranked Nr. 261 of 207 Cobots
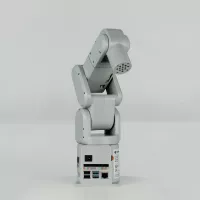
Top 10 mechArm 270-Pi Alternatives
- Elephant Robotics myCobot 280-Pi
- Elephant Robotics All-In-One Suite
- Elephant Robotics mechArm 270-M5
- Elephant Robotics All-In-One Suite
- FANUC CRX-10iA
- HITBOT Z-Arm 2442
- OMRON TM 5-900
- OMRON TM 5-700
- OMRON TM12
- OMRON TM14
- FLEXIV Rizon 4

Elephant Robotics myCobot 280-Pi
Payload 0.25kg | Reach 280mmThe myCobot 280-Pi is a compact six-axis collaborative robotic arm that is designed for desktop use. It is powered by a Raspberry Pi computer and is an ideal tool for education, research, and hobbyist projects.
The myCobot 280-Pi features a lightweight and durable aluminum alloy construction, which makes it easy to move and operate. It is equipped with high-precision stepper motors and a built-in controller that provides smooth and accurate movement control.
The robot arm is easy to set up and use, thanks to its intuitive software platform and user-friendly interface. It supports a wide range of programming languages, including Python, C++, and Scratch, which makes it easy for users with varying levels of coding experience to program and control the robot.
The myCobot 280-Pi is also equipped with a range of sensors, including a 3D camera, a force sensor, and a touch sensor, which enable it to interact with its environment and perform various tasks, such as object recognition and pick-and-place operations.

Elephant Robotics All-In-One Suite
Elephant Robotics' MechArm 270 All-in-one Suite is a powerful robotic arm system that offers a comprehensive set of features to meet a variety of industrial and research needs. The suite includes the MechArm 270 robotic arm, a camera flange, G shape base, adaptive gripper, and suction pump.
The MechArm 270 robotic arm is the centerpiece of the suite, offering six degrees of freedom and a maximum payload of 1.5 kg. The arm is constructed with high-strength aluminum alloy and features precision bearings and high-precision reducers to provide smooth, precise movements. The arm also has a built-in brake system to prevent drift and ensure accurate positioning.
The Camera Flange is a powerful tool that can be attached to the MechArm 270 to enable high-resolution imaging and video capture. The flange can accommodate a variety of cameras, including USB, HDMI, and GigE cameras, and can be rotated 360 degrees to capture images and video from any angle.
The G Shape Base is a sturdy platform that provides a stable and secure base for the MechArm 270. The base is designed to be easy to assemble and disassemble, making it ideal for applications where the arm needs to be moved or repositioned frequently.
The Adaptive Gripper is a versatile tool that can be used to grip and manipulate a wide variety of objects. The gripper features a flexible design that allows it to conform to the shape of the object being gripped, ensuring a secure and stable grip.
The Suction Pump is a powerful tool that can be used to manipulate objects using vacuum suction. The pump features a compact design and can generate up to 45 kPa of suction force, making it ideal for a wide variety of industrial and research applications.
Together, the MechArm 270 All-in-one Suite provides a powerful and versatile robotic arm system that is ideal for a wide variety of industrial and research applications. With its high payload capacity, precise movements, and advanced features, the MechArm 270 All-in-one Suite is a powerful tool that can help streamline production processes, reduce labor costs, and improve product quality.

Elephant Robotics mechArm 270-M5
Payload 0.25kg | Reach 270mmThe mechArm 270-M5 is a six-axis robotic arm developed by Elephant Robotics, designed specifically for collaborative robot (cobots) applications. It is the most compact six-axis collaborative robotic arm available, powered by M5Stack technology.
The mechArm 270-M5 is designed to work safely alongside humans in collaborative environments. It has a compact and lightweight design, making it easy to install and move. The robot arm has a maximum payload of 0.25 kg and a maximum reach of 270 mm.
One of the key features of the mechArm 270-M5 is its use of M5Stack technology. The M5Stack is a modular and open-source development kit that provides a simple and powerful way to create and prototype IoT and robotic projects. The mechArm 270-M5 is powered by M5Stack, which enables it to be easily programmed and controlled using a range of programming languages, including Python and Arduino.
The mechArm 270-M5 is also equipped with advanced safety features, including torque sensors and collision detection sensors, which enable it to stop or slow down its movements if it detects any obstacles in its path. This makes it safe to work alongside humans without the need for fencing or other safety measures.
The mechArm 270-M5 is ideal for a range of collaborative robot applications, including assembly, pick-and-place tasks, and inspection. Its compact size and advanced technology make it an ideal tool for small and medium-sized businesses looking to automate their processes.

Elephant Robotics All-In-One Suite
The Elephant Robotics myCobot 320 All-In-One Suite is a comprehensive package that includes the myCobot 320 robotic arm and a variety of end-effectors that can be used for different tasks. The myCobot 320 is a six-axis collaborative robotic arm that is designed to be compact and easy to use. It is suitable for a wide range of applications, including manufacturing, research, and education.
The All-In-One Suite includes several different end-effectors that can be used with the myCobot 320 robotic arm, including:
1. Suction Cups: The suction cups can be used to pick up and place small objects, such as electronic components, without damaging them.
2. Adaptive Gripper: The adaptive gripper is a versatile end-effector that can be used to grip and manipulate a wide range of objects, including irregularly shaped objects.
3. Soft Gripper: The soft gripper is designed to handle delicate objects, such as food or biological samples. It has a soft, compliant material that can conform to the shape of the object being gripped.
4. Air Compressor: The air compressor is used to power the air parallel gripper. It provides a source of compressed air that can be used to actuate the gripper.
5. Air Parallel Gripper: The air parallel gripper is a powerful end-effector that can be used to grip and manipulate heavy objects. It uses compressed air to actuate the gripper jaws, which can exert a significant amount of force.
The myCobot 320 robotic arm is designed to be easy to use and program. It can be programmed using a variety of programming languages, including Python and Blockly. It also includes an intuitive graphical user interface that makes it easy to control the arm and its end-effectors.

FANUC CRX-10iA
Payload 10kg | Reach 1249mmFanuc's CRX-10iA is a collaborative robot that is designed to work safely and efficiently alongside human workers. The robot is part of Fanuc's CRX series of collaborative robots, which are designed to provide a range of advanced capabilities and features to enhance manufacturing and other industrial processes.
The CRX-10iA is a compact and lightweight robot, with a payload capacity of up to 10 kilograms. It has a reach of up to 1249 millimeters, and can be mounted on the floor, ceiling, or wall, giving it a great deal of flexibility in terms of placement and orientation.
The robot is equipped with a range of advanced sensing and control technologies, including a built-in vision system that allows it to recognize and respond to its environment. It is also designed to work seamlessly with other robots and industrial equipment, making it a powerful tool for improving efficiency and productivity in a range of industrial settings.
One of the key features of the CRX-10iA is its ease of use and programming. The robot is designed with a user-friendly interface that allows operators to quickly and easily program and control its movements and behavior. It is also designed with safety in mind, with features such as collision detection and force sensing that help to prevent accidents and injuries.

HITBOT Z-Arm 2442
Payload 3kgThe Hitbot Z-Arm 2442 is a collaborative robotic arm designed for various industrial applications. This lightweight robotic arm weighs only 19kg and has a compact design, making it easy to install and use in confined spaces. The robot has a built-in motion controller, with 24 I/O ports for extensibility and adding one more arm.
The robot has four axes, with a maximum payload of 3kg and a rated payload of 2kg. The robot arm has a reach of 220mm for the J1 axis, 200mm for the J2 axis, and 240mm for the Z-axis. The rotation range for the J1 axis is ±90°, for the J2 axis is ±164°, and for the R-axis (optional) is ±1080°. The maximum average linear velocity of the robot arm is 1255.45mm/s (with a 1.5kg payload) and 1023.79mm/s (with a 2kg payload). The repeatability of the robot arm is ±0.03mm.
The robot arm supports HITBOT grippers such as Z-EFG-8S, Z-EFG-12, Z-EFG-20, Z-EFG-20S, Z-EFG-30, and Z-EFG-50. Additionally, the robot arm has optional accessories such as grippers, a 5th axis, a 485 board, and a 3D printing kit. The robot arm has a customizable Z-axis height ranging from 0.1-1 meter and supports drag-to-teach programming.
The robot arm has a voltage of 220V/110V 50-60Hz DC24V and power of 500W. The robot arm communicates through Ethernet and has a working temperature range of 0-55℃ with RH85 humidity. The robot arm has digital input (isolated) with 9+3 arm extensibility and digital output (isolated) with 9+3 extensibility for one more arm. The robot arm has collision detection technology, making it safe to operate in human-machine collaboration scenarios.
Overall, the Hitbot Z-Arm 2442 is a high-performance and versatile robotic arm that can be used in various industrial applications, including pick-and-place, assembly, and packaging. With its lightweight and compact design, customizable height, and extensibility, it is an excellent choice for industries looking for cost-effective and efficient automation solutions.

OMRON TM 5-900
Payload 4kg | Reach 900mm
Human and Machine in Perfect Harmony
THE COLLABORATIVE ROBOT
In any manufacturing environment today, the key emphasis is on how you can safely harness the power and precision of robots along with the problem-solving ability of humans to achieve greater productivity.
Designed to work with both humans and machines, the OMRON TM Collaborative Robot lets you attain better efficiency with its wide range of industrial applications while ensuring workplace safety.
DISCOVER OUR KEY BENEFITS:
Flexibility for your Factory
Maximise your resources and increase productivity by configuring the robot system at will to respond to any production requirement. Our Collaborative Robot's versatility allows it to be assigned to almost any task.
The diverse range of applications served by the robot system includes machine tending, loading and uploading, assembling, screwing, gluing, testing, soldering, and logistics.

Quick Start-up & Changeover
Downtime incurs costs, which means you require a robot that can start fast and stay running. The intuitive software of OMRON TM Collaborative Robot facilitates quick programming during startups and changeovers. The simplified programming for these robots requires no coding or pendant, giving users faster startup time. For example, a complete pick-and-place task with vision inspection can be taught in minutes.
Unique Built-in Vision
Unlike others, OMRON TM Collaborative Robot has a built-in intelligent vision system that can be used for pattern matching, object positioning and barcode reading. The integrated camera localises objects in a wide field of vision while the image-enhancement light enables object recognition under almost any conditions.

Easy Mobility
The mobility of the OMRON TM Collaborative Robot allow you to easily relocate and recommission it for any new task.
Safety is Our Priority
To ensure seamless work between robots and humans, we are dedicated to ensuring the safety of our collaborative robots. Our robots comply with the strict safety requirements specified in ISO 10218-1 and ISO/TS 15066.
In some regions, OMRON offers safety assessment service, conducted by trained safety specialists. Do check with your local OMRON representative to find out more.


OMRON TM 5-700
Payload 6kg | Reach 700mm
Human and Machine in Perfect Harmony
THE COLLABORATIVE ROBOT
In any manufacturing environment today, the key emphasis is on how you can safely harness the power and precision of robots along with the problem-solving ability of humans to achieve greater productivity.
Designed to work with both humans and machines, the OMRON TM Collaborative Robot lets you attain better efficiency with its wide range of industrial applications while ensuring workplace safety.
DISCOVER OUR KEY BENEFITS:
Flexibility for your Factory
Maximise your resources and increase productivity by configuring the robot system at will to respond to any production requirement. Our Collaborative Robot's versatility allows it to be assigned to almost any task.
The diverse range of applications served by the robot system includes machine tending, loading and uploading, assembling, screwing, gluing, testing, soldering, and logistics.

Quick Start-up & Changeover
Downtime incurs costs, which means you require a robot that can start fast and stay running. The intuitive software of OMRON TM Collaborative Robot facilitates quick programming during startups and changeovers. The simplified programming for these robots requires no coding or pendant, giving users faster startup time. For example, a complete pick-and-place task with vision inspection can be taught in minutes.
Unique Built-in Vision
Unlike others, OMRON TM Collaborative Robot has a built-in intelligent vision system that can be used for pattern matching, object positioning and barcode reading. The integrated camera localises objects in a wide field of vision while the image-enhancement light enables object recognition under almost any conditions.

Easy Mobility
The mobility of the OMRON TM Collaborative Robot allow you to easily relocate and recommission it for any new task.
Safety is Our Priority
To ensure seamless work between robots and humans, we are dedicated to ensuring the safety of our collaborative robots. Our robots comply with the strict safety requirements specified in ISO 10218-1 and ISO/TS 15066.
In some regions, OMRON offers safety assessment service, conducted by trained safety specialists. Do check with your local OMRON representative to find out more.


OMRON TM12
Payload 12kg | Reach 1300mm
Human and Machine in Perfect Harmony
THE COLLABORATIVE ROBOT
In any manufacturing environment today, the key emphasis is on how you can safely harness the power and precision of robots along with the problem-solving ability of humans to achieve greater productivity.
Designed to work with both humans and machines, the OMRON TM Collaborative Robot lets you attain better efficiency with its wide range of industrial applications while ensuring workplace safety.
DISCOVER OUR KEY BENEFITS:
Flexibility for your Factory
Maximise your resources and increase productivity by configuring the robot system at will to respond to any production requirement. Our Collaborative Robot's versatility allows it to be assigned to almost any task.
The diverse range of applications served by the robot system includes machine tending, loading and uploading, assembling, screwing, gluing, testing, soldering, and logistics.

Quick Start-up & Changeover
Downtime incurs costs, which means you require a robot that can start fast and stay running. The intuitive software of OMRON TM Collaborative Robot facilitates quick programming during startups and changeovers. The simplified programming for these robots requires no coding or pendant, giving users faster startup time. For example, a complete pick-and-place task with vision inspection can be taught in minutes.
Unique Built-in Vision
Unlike others, OMRON TM Collaborative Robot has a built-in intelligent vision system that can be used for pattern matching, object positioning and barcode reading. The integrated camera localises objects in a wide field of vision while the image-enhancement light enables object recognition under almost any conditions.

Easy Mobility
The mobility of the OMRON TM Collaborative Robot allow you to easily relocate and recommission it for any new task.
Safety is Our Priority
To ensure seamless work between robots and humans, we are dedicated to ensuring the safety of our collaborative robots. Our robots comply with the strict safety requirements specified in ISO 10218-1 and ISO/TS 15066.
In some regions, OMRON offers safety assessment service, conducted by trained safety specialists. Do check with your local OMRON representative to find out more.


OMRON TM14
Payload 14kg | Reach 1100mm
Human and Machine in Perfect Harmony
THE COLLABORATIVE ROBOT
In any manufacturing environment today, the key emphasis is on how you can safely harness the power and precision of robots along with the problem-solving ability of humans to achieve greater productivity.
Designed to work with both humans and machines, the OMRON TM Collaborative Robot lets you attain better efficiency with its wide range of industrial applications while ensuring workplace safety.
DISCOVER OUR KEY BENEFITS:
Flexibility for your Factory
Maximise your resources and increase productivity by configuring the robot system at will to respond to any production requirement. Our Collaborative Robot's versatility allows it to be assigned to almost any task.
The diverse range of applications served by the robot system includes machine tending, loading and uploading, assembling, screwing, gluing, testing, soldering, and logistics.

Quick Start-up & Changeover
Downtime incurs costs, which means you require a robot that can start fast and stay running. The intuitive software of OMRON TM Collaborative Robot facilitates quick programming during startups and changeovers. The simplified programming for these robots requires no coding or pendant, giving users faster startup time. For example, a complete pick-and-place task with vision inspection can be taught in minutes.
Unique Built-in Vision
Unlike others, OMRON TM Collaborative Robot has a built-in intelligent vision system that can be used for pattern matching, object positioning and barcode reading. The integrated camera localises objects in a wide field of vision while the image-enhancement light enables object recognition under almost any conditions.

Easy Mobility
The mobility of the OMRON TM Collaborative Robot allow you to easily relocate and recommission it for any new task.
Safety is Our Priority
To ensure seamless work between robots and humans, we are dedicated to ensuring the safety of our collaborative robots. Our robots comply with the strict safety requirements specified in ISO 10218-1 and ISO/TS 15066.
In some regions, OMRON offers safety assessment service, conducted by trained safety specialists. Do check with your local OMRON representative to find out more.
