HITBOT Z-Arm 2442 Alternatives & Competitors
Ranked Nr. 272 of 207 Cobots
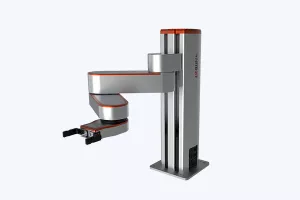
Top 10 Z-Arm 2442 Alternatives
- Elephant Robotics mechArm 270-Pi
- Elephant Robotics All-In-One Suite
- FANUC CRX-10iA
- OMRON TM 5-700
- OMRON TM 5-900
- OMRON TM12
- OMRON TM14
- FLEXIV Rizon 4
- FANUC CRX-5iA
- HITBOT Z-Arm 1832
- FANUC CRX-25iA

Elephant Robotics mechArm 270-Pi
Payload 0.25kg | Reach 270mmThe MechArm 270-Pi is a six-axis collaborative robotic arm that is designed to be compact and powered by a Raspberry Pi. This robotic arm is a DIY kit that allows users to build their own robotic arm and program it to perform various tasks.
The MechArm 270-Pi is one of the most compact six-axis collaborative robotic arms on the market. It has a reach of 270mm and a payload capacity of 0.25kgs, which makes it ideal for small-scale automation tasks. The arm is designed to be collaborative, which means it can work safely alongside humans without causing any harm.
The robotic arm is powered by a Raspberry Pi, which is a popular single-board computer that can be programmed using a variety of programming languages. The Raspberry Pi provides a user-friendly interface for programming the arm, and it also allows the arm to be integrated with other devices and systems.
The MechArm 270-Pi is a DIY kit, which means that users need to assemble the arm themselves. The kit includes all the necessary components, including the motors, the controller, and the Raspberry Pi. The assembly process is straightforward and can be completed in a few hours.
Once the arm is assembled, users can program it to perform various tasks using Python or other programming languages. The robotic arm can be used for a wide range of applications, such as pick-and-place tasks, machine tending, and quality control.

Elephant Robotics All-In-One Suite
The Elephant Robotics myCobot 320 All-In-One Suite is a comprehensive package that includes the myCobot 320 robotic arm and a variety of end-effectors that can be used for different tasks. The myCobot 320 is a six-axis collaborative robotic arm that is designed to be compact and easy to use. It is suitable for a wide range of applications, including manufacturing, research, and education.
The All-In-One Suite includes several different end-effectors that can be used with the myCobot 320 robotic arm, including:
1. Suction Cups: The suction cups can be used to pick up and place small objects, such as electronic components, without damaging them.
2. Adaptive Gripper: The adaptive gripper is a versatile end-effector that can be used to grip and manipulate a wide range of objects, including irregularly shaped objects.
3. Soft Gripper: The soft gripper is designed to handle delicate objects, such as food or biological samples. It has a soft, compliant material that can conform to the shape of the object being gripped.
4. Air Compressor: The air compressor is used to power the air parallel gripper. It provides a source of compressed air that can be used to actuate the gripper.
5. Air Parallel Gripper: The air parallel gripper is a powerful end-effector that can be used to grip and manipulate heavy objects. It uses compressed air to actuate the gripper jaws, which can exert a significant amount of force.
The myCobot 320 robotic arm is designed to be easy to use and program. It can be programmed using a variety of programming languages, including Python and Blockly. It also includes an intuitive graphical user interface that makes it easy to control the arm and its end-effectors.

FANUC CRX-10iA
Payload 10kg | Reach 1249mmFanuc's CRX-10iA is a collaborative robot that is designed to work safely and efficiently alongside human workers. The robot is part of Fanuc's CRX series of collaborative robots, which are designed to provide a range of advanced capabilities and features to enhance manufacturing and other industrial processes.
The CRX-10iA is a compact and lightweight robot, with a payload capacity of up to 10 kilograms. It has a reach of up to 1249 millimeters, and can be mounted on the floor, ceiling, or wall, giving it a great deal of flexibility in terms of placement and orientation.
The robot is equipped with a range of advanced sensing and control technologies, including a built-in vision system that allows it to recognize and respond to its environment. It is also designed to work seamlessly with other robots and industrial equipment, making it a powerful tool for improving efficiency and productivity in a range of industrial settings.
One of the key features of the CRX-10iA is its ease of use and programming. The robot is designed with a user-friendly interface that allows operators to quickly and easily program and control its movements and behavior. It is also designed with safety in mind, with features such as collision detection and force sensing that help to prevent accidents and injuries.

OMRON TM 5-700
Payload 6kg | Reach 700mm
Human and Machine in Perfect Harmony
THE COLLABORATIVE ROBOT
In any manufacturing environment today, the key emphasis is on how you can safely harness the power and precision of robots along with the problem-solving ability of humans to achieve greater productivity.
Designed to work with both humans and machines, the OMRON TM Collaborative Robot lets you attain better efficiency with its wide range of industrial applications while ensuring workplace safety.
DISCOVER OUR KEY BENEFITS:
Flexibility for your Factory
Maximise your resources and increase productivity by configuring the robot system at will to respond to any production requirement. Our Collaborative Robot's versatility allows it to be assigned to almost any task.
The diverse range of applications served by the robot system includes machine tending, loading and uploading, assembling, screwing, gluing, testing, soldering, and logistics.

Quick Start-up & Changeover
Downtime incurs costs, which means you require a robot that can start fast and stay running. The intuitive software of OMRON TM Collaborative Robot facilitates quick programming during startups and changeovers. The simplified programming for these robots requires no coding or pendant, giving users faster startup time. For example, a complete pick-and-place task with vision inspection can be taught in minutes.
Unique Built-in Vision
Unlike others, OMRON TM Collaborative Robot has a built-in intelligent vision system that can be used for pattern matching, object positioning and barcode reading. The integrated camera localises objects in a wide field of vision while the image-enhancement light enables object recognition under almost any conditions.

Easy Mobility
The mobility of the OMRON TM Collaborative Robot allow you to easily relocate and recommission it for any new task.
Safety is Our Priority
To ensure seamless work between robots and humans, we are dedicated to ensuring the safety of our collaborative robots. Our robots comply with the strict safety requirements specified in ISO 10218-1 and ISO/TS 15066.
In some regions, OMRON offers safety assessment service, conducted by trained safety specialists. Do check with your local OMRON representative to find out more.


OMRON TM 5-900
Payload 4kg | Reach 900mm
Human and Machine in Perfect Harmony
THE COLLABORATIVE ROBOT
In any manufacturing environment today, the key emphasis is on how you can safely harness the power and precision of robots along with the problem-solving ability of humans to achieve greater productivity.
Designed to work with both humans and machines, the OMRON TM Collaborative Robot lets you attain better efficiency with its wide range of industrial applications while ensuring workplace safety.
DISCOVER OUR KEY BENEFITS:
Flexibility for your Factory
Maximise your resources and increase productivity by configuring the robot system at will to respond to any production requirement. Our Collaborative Robot's versatility allows it to be assigned to almost any task.
The diverse range of applications served by the robot system includes machine tending, loading and uploading, assembling, screwing, gluing, testing, soldering, and logistics.

Quick Start-up & Changeover
Downtime incurs costs, which means you require a robot that can start fast and stay running. The intuitive software of OMRON TM Collaborative Robot facilitates quick programming during startups and changeovers. The simplified programming for these robots requires no coding or pendant, giving users faster startup time. For example, a complete pick-and-place task with vision inspection can be taught in minutes.
Unique Built-in Vision
Unlike others, OMRON TM Collaborative Robot has a built-in intelligent vision system that can be used for pattern matching, object positioning and barcode reading. The integrated camera localises objects in a wide field of vision while the image-enhancement light enables object recognition under almost any conditions.

Easy Mobility
The mobility of the OMRON TM Collaborative Robot allow you to easily relocate and recommission it for any new task.
Safety is Our Priority
To ensure seamless work between robots and humans, we are dedicated to ensuring the safety of our collaborative robots. Our robots comply with the strict safety requirements specified in ISO 10218-1 and ISO/TS 15066.
In some regions, OMRON offers safety assessment service, conducted by trained safety specialists. Do check with your local OMRON representative to find out more.


OMRON TM12
Payload 12kg | Reach 1300mm
Human and Machine in Perfect Harmony
THE COLLABORATIVE ROBOT
In any manufacturing environment today, the key emphasis is on how you can safely harness the power and precision of robots along with the problem-solving ability of humans to achieve greater productivity.
Designed to work with both humans and machines, the OMRON TM Collaborative Robot lets you attain better efficiency with its wide range of industrial applications while ensuring workplace safety.
DISCOVER OUR KEY BENEFITS:
Flexibility for your Factory
Maximise your resources and increase productivity by configuring the robot system at will to respond to any production requirement. Our Collaborative Robot's versatility allows it to be assigned to almost any task.
The diverse range of applications served by the robot system includes machine tending, loading and uploading, assembling, screwing, gluing, testing, soldering, and logistics.

Quick Start-up & Changeover
Downtime incurs costs, which means you require a robot that can start fast and stay running. The intuitive software of OMRON TM Collaborative Robot facilitates quick programming during startups and changeovers. The simplified programming for these robots requires no coding or pendant, giving users faster startup time. For example, a complete pick-and-place task with vision inspection can be taught in minutes.
Unique Built-in Vision
Unlike others, OMRON TM Collaborative Robot has a built-in intelligent vision system that can be used for pattern matching, object positioning and barcode reading. The integrated camera localises objects in a wide field of vision while the image-enhancement light enables object recognition under almost any conditions.

Easy Mobility
The mobility of the OMRON TM Collaborative Robot allow you to easily relocate and recommission it for any new task.
Safety is Our Priority
To ensure seamless work between robots and humans, we are dedicated to ensuring the safety of our collaborative robots. Our robots comply with the strict safety requirements specified in ISO 10218-1 and ISO/TS 15066.
In some regions, OMRON offers safety assessment service, conducted by trained safety specialists. Do check with your local OMRON representative to find out more.


OMRON TM14
Payload 14kg | Reach 1100mm
Human and Machine in Perfect Harmony
THE COLLABORATIVE ROBOT
In any manufacturing environment today, the key emphasis is on how you can safely harness the power and precision of robots along with the problem-solving ability of humans to achieve greater productivity.
Designed to work with both humans and machines, the OMRON TM Collaborative Robot lets you attain better efficiency with its wide range of industrial applications while ensuring workplace safety.
DISCOVER OUR KEY BENEFITS:
Flexibility for your Factory
Maximise your resources and increase productivity by configuring the robot system at will to respond to any production requirement. Our Collaborative Robot's versatility allows it to be assigned to almost any task.
The diverse range of applications served by the robot system includes machine tending, loading and uploading, assembling, screwing, gluing, testing, soldering, and logistics.

Quick Start-up & Changeover
Downtime incurs costs, which means you require a robot that can start fast and stay running. The intuitive software of OMRON TM Collaborative Robot facilitates quick programming during startups and changeovers. The simplified programming for these robots requires no coding or pendant, giving users faster startup time. For example, a complete pick-and-place task with vision inspection can be taught in minutes.
Unique Built-in Vision
Unlike others, OMRON TM Collaborative Robot has a built-in intelligent vision system that can be used for pattern matching, object positioning and barcode reading. The integrated camera localises objects in a wide field of vision while the image-enhancement light enables object recognition under almost any conditions.

Easy Mobility
The mobility of the OMRON TM Collaborative Robot allow you to easily relocate and recommission it for any new task.
Safety is Our Priority
To ensure seamless work between robots and humans, we are dedicated to ensuring the safety of our collaborative robots. Our robots comply with the strict safety requirements specified in ISO 10218-1 and ISO/TS 15066.
In some regions, OMRON offers safety assessment service, conducted by trained safety specialists. Do check with your local OMRON representative to find out more.


FLEXIV Rizon 4
Payload 4kg | Reach 780mmThe first adaptive robot, among the most advanced in its class. Designed for advanced manufacturing, assembly, and inspection applications. The robot is capable of high-precision movement and can perform a wide range of tasks, including pick-and-place operations, material handling, and surface inspection.
It is possible because the robot is equipped with advanced sensors and algorithms that allow it to detect and avoid collisions with objects and people in its workspace.
One of the key features of the Rizon 4 is its high level of flexibility and adaptability. The robot can be easily reprogrammed to perform different tasks or to work with different types of objects, making it a versatile solution for manufacturers with changing needs.
The Rizon 4 is also designed with advanced technologies that enhance its accuracy and reliability. For example, the robot is equipped with Flexiv's patented "Robotics Intelligence Operating System" (RIOS), which uses machine learning and other advanced algorithms to optimize the robot's performance and adapt to changes in its environment.
In addition to its advanced capabilities, the Rizon 4 is also designed with ease of use in mind. The robot is intuitive to program and operate, and can be controlled using a simple touch screen interface.

FANUC CRX-5iA
Payload 5kg | Reach 994mmThe CRX-5iA Collaborative Robot, featuring a 5kg payload and 994mm reach, stands out as an ideal choice for manufacturers with limited robotic experience. The CRX series introduces a user-friendly FANUC programming interface, incorporating drag-and-drop technology on a touchscreen pendant. Its sensitivity to contact detection ensures safe collaboration with human workers in diverse industrial and manufacturing tasks. Notably, the CRX-5iA, like the entire CRX series, offers 8 years of zero maintenance, underscoring FANUC's commitment to industrial reliability.
Installation is streamlined with the CRX-5iA's lightweight and compact design, allowing easy integration into various work areas without the need for a crane or lifting equipment. The robot operates on standard 120V power and utilizes FANUC's latest compact R-30iB Mini Plus Controller, optimizing space efficiency. Programming is simplified through lead-through teaching and drag-and-drop capabilities on the teach pendant, supported by instructional CRX e-Learning videos for quick setup. The CRX-5iA ensures versatility in peripherals, with two connection ports on the J6 axis facilitating quick interchangeability for end-of-arm tooling, such as grippers and cameras. Additionally, FANUC intelligent features enable seamless connection to iRVision, force sensors, and more, enhancing its adaptability for diverse industrial applications.

HITBOT Z-Arm 1832
Payload 1kgHITBOT Z-Arm 1832, is a cutting-edge robotic arm designed for precision, flexibility, and collaboration. This robotic arm has a compact design, measuring only 500mm in height and weighing 11KG, making it easy to deploy in various application scenarios.
The HITBOT Z-Arm 1832 is a 4-axis collaborative robotic arm with a maximum payload of 1KG and a rated payload of 0.5KG. It has a linear velocity of 1017mm/s and a repeatability of ±0.02mm. The J1 and J2 axes have an arm reach of 160mm and a rotation range of ±90° and ±143°, respectively. The Z-axis has a reach of 180mm, while the R-axis has a reach of ±1080°. This range of motion enables the robotic arm to perform various tasks with great precision.
One of the standout features of the HITBOT Z-Arm 1832 is its ease of use. It is designed to be simple but versatile, with a handheld teaching programming system that makes it easy to program and use. Additionally, it supports SDK secondary development, allowing users to customize its functionality according to their needs.
Another essential feature of the HITBOT Z-Arm 1832 is its collaborative and safe design. It supports collision detection, which ensures smart human-machine collaboration and prevents accidental collisions. This makes it safe to use in various settings, including those where humans are present.
The HITBOT Z-Arm 1832 is compatible with a range of HITBOT grippers, including the Z-EFG-8S, Z-EFG-12, Z-EFG-20, and Z-EFG-20S. It also has I/O ports for digital input and output (isolated) and customizable Z-axis height, with drag-to-teach capabilities.
In conclusion, the Hatbox's 832 Collaborative Robotic Arm, the HITBOT Z-Arm 1832, is a top-of-the-line robotic arm that is both compact and precise. Its flexibility, simplicity, and versatility make it an ideal choice for various applications, while its collaborative and safe design ensures that it can be used safely in various settings.