SensoPart VISOR® Robotic - Vision sensor Alternatives & Competitors
Ranked Nr. 12 of 93 3D Vision Systems
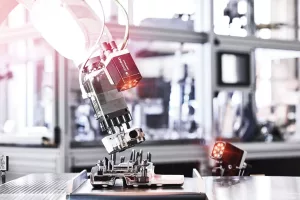
Top 10 VISOR® Robotic - Vision sensor Alternatives
- Pickit 3D Assembly
- ZIVID Zivid Two
- Photonfocus MV2-D1280-O01-3D06-G1
- Photonfocus MV0-D1280-O01-3D06-288-G2
- Photonfocus MV0-D2048x1088-C01-3D06-768-G2
- Photonfocus MV4-D2048x1088-C01-3D06-G2
- Photonfocus MV4-D1280-L01-3D06-G2
- Photonfocus MV4-D1280-L01-3D06-FB
- Photonfocus MV4-D1280-L01-3D07-GT
- Photonfocus MV1-D1024E-3D02-160-G2

Pickit 3D Assembly
Is your assembly agile enough for varying products?
Assemble products more flexibly, reliably and cost-efficiently with 3D robot vision.
How your assembly process benefits from 3D robot vision:
1. Manufacture smarter with reliable 3D robot vision assembly capable of handling objects of different sizes in unfixed positions!
2. Flexibly, rapidly and cost-efficiently switch to new processes and products without major interventions typical for static robot fixtures!
3. Optimize your production line footprint!
4. Reduce costs and downtime resulting from complex production adjustments and maintenance!

ZIVID Zivid Two
Human-like vision for pick and place robotics.
Zivid Two gives you exceptional 3D image quality lightning fast in an ultra-compact form-factor. Design fast, reliable pick and place robots cells capable of handling a wide variety of challenging objects and scenes.
High quality, native color 3D point clouds for better object recognition.
See tiny objects and the fine details.
High resolution and precision point clouds of even very small, densely packed or highly detailed objects. Distinguish features smaller than 5 mm.
2.3 Mpix- HD resolution
55 μm- Point precision
Minimal occlusion- 112 mm baseline
See reflective and shiny objects.
Take images of traditionally challenging parts such as sheet metal, machined and polished parts, glossy packaging, semi-transparent and plastic wrapped objects. Excellent suppression of artifacts from reflections, interreflections, specular highlights and high contrast transitions.
ART- Artifact Reduction Technology
3D HDR-High Dynamic Range
See a wide variety of objects.
The unique combination of native color and high dynamic range enables imaging of a broad range of objects. Plastic, ceramic, metal, cardboard, wood, colored, textured, light, dark and absorptive. Single or mixed SKU bin scenarios, densely stacked or randomly arranged.
3D RGB- Native colors
White light- Broad material coverage
Pick with confidence
True to reality 3D point clouds for more accurate and reliable grasping and manipulation.
Accurate picks and fine manipulation.
Point clouds with true to reality representation of object size, rotation, and absolute position. Enables demanding pick and place operations and gives flexibility in choice of gripper.
< 0.2% at focus distance -Dimension trueness error
3D hand-eye calibration- 10x more accurate
Less mispicks and crashes.
Minimal trueness drift and variation across the full operating temperature range and under mechanical stress from handling and use.
Floating thermal calibration
Mechanical and thermal stability
Work faster.
Improved cycle time with fast 3D point cloud captures.
<100 ms capture time.
Low to medium dynamic range scenes. Wide variety of objects in all shades, except the darkest black and absorptive.
<300 ms capture time.
High dynamic range scenes. Highly shiny and reflective, white and dark absorptive objects in the same scene.
<1s capture time.
Extreme dynamic range scenes or longer working distances. Highly specular, chrome plated and mirror like. Objects positioned with steep angles away from the camera and super absorptive absolute black objects.
On-arm versatility.
Unleashing the potential of on-arm mounting in pick-and-place robotics.
Unrestricted movement.
Compact, lightweight and fast 3D camera for on-arm mounting for even smaller collaborative robots. Minimum impact on maneuverability, usable payload and cycle time.
169 x 122 x 56 mm-Palm sized
940 grams- Maximize robot maneuverability
60 ms- Minimize acquisition time
Extended field of view.
Leverage on-arm camera to cover larger bins, pallets and flow racks. Use a single on-arm camera for multiple bins or pallets.
Multi-view imaging.
Capture images from multiple or different viewpoints to improve object recognition and reliably empty the bin.

Photonfocus MV2-D1280-O01-3D06-G1
MonochromeThe camera MV2-D1280-O01-3D06-G1 is based on the ON Semiconductor PYTHON1300 CMOS image sensor. The PYTHON1300 CMOS image sensor is optimized for low light conditions and is available as standard monochrome version. The camera has the GigE interface (GigEVision).
These cameras focus on demanding applications in industrial image processing. They are optimized for low light applications. Due to the global shutter, even high-speed applications with exposure times in the µs-area are possible.
FEATURES:
- Configurable region of interest (ROI)
- Decimation in y-direction
- 2 look-up tables (12-to-8Bit) on user-defined image region (Region-LUT)
- Constant frame rate independent of exposure time
- Temperature monitoring of camera
- Camera informations readable over SDK
- Ultra low trigger delay and low trigger jitter
- Extended trigger input and strobe output functionality
- Status line in picture
- with Shaft Encoder

Photonfocus MV0-D1280-O01-3D06-288-G2
MonochromeThe camera MV0-D1280-O01-3D06-288-G2 is based on the ON Semiconductor PYTHON1300 CMOS image sensor. The PYTHON1300 CMOS image sensor is optimized for low light conditions and is available as standard monochrome version. The camera has the GigE interface (GigEVision).
These cameras focus on demanding applications in industrial image processing. They are optimized for low light applications. Due to the global shutter, even high-speed applications with exposure times in the µs-area are possible.
FEATURES:
- Configurable region of interest (ROI)
- Decimation in y-direction
- 2 look-up tables (12-to-8Bit) on user-defined image region (Region-LUT)
- Constant frame rate independent of exposure time
- Temperature monitoring of camera
- Camera informations readable over SDK
- Ultra low trigger delay and low trigger jitter
- Extended trigger input and strobe output functionality
- Status line in picture
- with Shaft Encoder

Photonfocus MV0-D2048x1088-C01-3D06-768-G2
MonochromeThe camera MV0-D2048x1088-C01-3D06-768-G2 is based on the CMOSIS CMV2000 V3 CMOS image sensor. The CMV2000 V3 CMOS image sensor is optimized for low light conditions and is available as standard monochrome version. The camera has the GigE interface (GigEVision).
These cameras focus on demanding applications in industrial image processing. They are optimized for low light applications. Due to the global shutter, even high-speed applications with exposure times in the µs-area are possible.
FEATURES:
- Configurable region of interest (ROI)
- Decimation in y-direction
- 2 look-up tables (12-to-8Bit) on user-defined image region (Region-LUT)
- Constant frame rate independent of exposure time
- Temperature monitoring of camera
- Camera informations readable over SDK
- Ultra low trigger delay and low trigger jitter
- Extended trigger input and strobe output functionality
- Status line in picture
- with Shaft Encoder

Photonfocus MV4-D2048x1088-C01-3D06-G2
MonochromeThe 3D CMOS cameras MV4-D2048x1088-C01-3D06-G2 are designed for high triangulation rates. The CMOSIS CMOS image sensor CMV2000, which is optimized for high frame rates and high sensitivity, was combined with two robust algorithms to determine the triangulation line in the FPGA of the camera. The user can either employ a FIR algorithm for asymmetric line profiles or a robust COG algorithm for symmetric profiles.
The triangulation algorithm activated in the camera calculates the line position of a line with 1/16 sub-pixel accuracy. In addition to the output of the height profiles, qualifiers are also output, which can be used to suppress artifacts or characterize the surface.
The camera is equipped with GigE interfaces and is therefore able to capture 3D profiles without a frame grabber or to set up cost-effective multi-camera systems as used for the inspection of profiles. The camera is available with GigE, 10 GigE and 10 GigE fiber interface, according to the GigE Vision and GenICam standards. In addition, the cameras have a complete encoder interface that can be configured for the TTL, RS422, HTL and dHTL interface standards, as well as various outputs. External devices with an RS485 interface can also be optionally controlled. Of course, all I/O's are galvanically decoupled from the camera electronics. The field-tested cooling concept of the MV4 housing provides for a sufficient electronics cooling.
FEATURES:
- Linear Mode / multiple slope (High Dynamic Range Mode)
- Configurable region of interest (ROI)
- Temperature monitoring of camera
- Low trigger delay and low trigger jitter
- Extended trigger input and strobe output functionality
- 4x Isolated inputs or shaft encoder A, B, Z, Y interface (RS422, TTL, D-HTL, HTL)
- 3x Isolated outputs (2x open drain, 1x TTL highspeed)

Photonfocus MV4-D1280-L01-3D06-G2
MonochromeThe 3D CMOS cameras MV4-D1280-L01-3D06-G2 (LUX1310) are designed for high triangulation rates. The LUXIMA CMOS image sensor LUX1310, which is optimized for high frame rates and high sensitivity, was combined with two robust algorithms to determine the triangulation line in the FPGA of the camera. The user can either employ a FIR algorithm for asymmetric line profiles or a robust COG algorithm for symmetric profiles.
The triangulation algorithm activated in the camera calculates the line position of a line with 1/16 sub-pixel accuracy. In addition to the output of the height profiles, qualifiers are also output, which can be used to suppress artifacts or characterize the surface.
The camera is equipped with GigE interfaces and is therefore able to capture 3D profiles without a frame grabber or to set up cost-effective multi-camera systems as used for the inspection of profiles. The camera is available with GigE, 10 GigE and 10 GigE fiber interface, according to the GigE Vision and GenICam standards. In addition, the cameras have a complete encoder interface that can be configured for the TTL, RS422, HTL and dHTL interface standards, as well as various outputs. External devices with an RS485 interface can also be optionally controlled. Of course all I/O's are galvanically decoupled from the camera electronics.
3D triangulation rate at different ROI's:
Resolution | Profiles [fps] |
1280 x 1024 | 1065 |
1280 x 512 | 2119 |
1280 x 256 | 4193 |
1280 x 128 | 8207 |
1280 x 64 | 15739 |
1280 x 32 | 29088 |
1280 x 16 | 41880 |
1280 x 11 | 41880 |
Features:
- Linear Mode / multiple slope (High Dynamic Range Mode)
- Temperature monitoring of camera
- Low trigger delay and low trigger jitter
- Extended trigger input and strobe output functionality
- 4x Isolated inputs or shaft encoder A, B, Z, Y interface (RS422, TTL, D-HTL, HTL)
- 3x Isolated outputs (2x open drain, 1x TTL highspeed)

Photonfocus MV4-D1280-L01-3D06-FB
MonochromeThe 3D CMOS cameras MV4-D1280-L01-3D06-FB (LUX1310) are designed for high triangulation rates. The LUXIMA CMOS image sensor LUX1310, which is optimized for high frame rates and high sensitivity, was combined with two robust algorithms to determine the triangulation line in the FPGA of the camera. The user can either employ a FIR algorithm for asymmetric line profiles or a robust COG algorithm for symmetric profiles.
The triangulation algorithm activated in the camera calculates the line position of a line with 1/16 sub-pixel accuracy. In addition to the output of the height profiles, qualifiers are also output, which can be used to suppress artifacts or characterize the surface.
The camera is equipped with GigE interfaces and is therefore able to capture 3D profiles without a frame grabber or to set up cost-effective multi-camera systems as used for the inspection of profiles. The camera is available with GigE, 10 GigE and 10 GigE fiber interface, according to the GigE Vision and GenICam standards. In addition, the cameras have a complete encoder interface that can be configured for the TTL, RS422, HTL and dHTL interface standards, as well as various outputs. External devices with an RS485 interface can also be optionally controlled. Of course all I/O's are galvanically decoupled from the camera electronics.
3D triangulation rate at different ROI's:
Resolution | Profiles [fps] |
1280 x 1024 | 1065 |
1280 x 512 | 2119 |
1280 x 256 | 4193 |
1280 x 128 | 8207 |
1280 x 64 | 15739 |
1280 x 32 | 29088 |
1280 x 16 | 50505 |
1280 x 11 | 65600 |
FEATURES:
- Linear Mode / multiple slope (High Dynamic Range Mode)
- Temperature monitoring of camera
- Low trigger delay and low trigger jitter
- Extended trigger input and strobe output functionality
- 4x Isolated inputs or shaft encoder A, B, Z, Y interface (RS422, TTL, D-HTL, HTL)
- 3x Isolated outputs (2x open drain, 1x TTL highspeed)

Photonfocus MV4-D1280-L01-3D07-GT
MonochromeThe 3D CMOS cameras MV4-D1280-L01-3D07-GT (LUX1310) are designed for high triangulation rates. The LUXIMA CMOS image sensor LUX1310, which is optimized for high frame rates and high sensitivity, was combined with a robust Multi Peak Linefinder algorithm to determine up to four triangulation lines in a single scan in the FPGA of the camera.
The triangulation algorithm activated in the camera calculates the line position of the four laser lines with 1/64 sub-pixel accuracy. In addition to the output of the height profiles, qualifiers are also output, which can be used to suppress artifacts or characterize the surface.
The camera is equipped with GigE interfaces and is therefore able to capture 3D profiles without a frame grabber or to set up cost-effective multi-camera systems as used for the inspection of profiles. The camera is available with10 GigE interface, according to the GigE Vision and GenICam standards. In addition, the cameras have a complete encoder interface that can be configured for the TTL, RS422, HTL and dHTL interface standards, as well as various outputs. External devices with an RS485 interface can also be optionally controlled. Of course all I/O's are galvanically decoupled from the camera electronics.
3D triangulation rate at different ROI's:
Resolution | Profiles [fps] |
1280 x 1024 | 1065 |
1280 x 512 | 2119 |
1280 x 256 | 4193 |
1280 x 128 | 8207 |
1280 x 64 | 15739 |
1280 x 32 | 29088 |
1280 x 16 | 50505 |
1280 x 11 | 65600 |
FEATURES:
- Up to 65600 profiles/s @ 1280 x 11 resolution
- Detection of up to 4 peaks in a single scan
- High reliability and accuracy of 3D reconstruction, due to the non-linear interpolation technique used in the detection algorithm
- Laser line detection with up to 1/64 sub pixel accuracy
- Linear Mode / multiple slope (High Dynamic Range)
- Configurable region of interest (ROI)
- Temperature monitoring of camera
- Low trigger delay and low trigger jitter
- Extended trigger input and strobe output functionality
- 4x Isolated inputs or shaft encoder A, B, Z, Y interface (RS422, TTL, D-HTL, HTL)
- 3x Isolated outputs (2x open drain, 1x TTL highspeed)
- Free GUI available (PF 3D Suite) for an easy system set up and visualisation of 3D scans

Photonfocus MV1-D1024E-3D02-160-G2
MonochromeThe CMOS camera MV1-D1024E-3D02-160-G2 was developed for laser triangulation of highly reflective materials. The Photonfocus CMOS sensor A1024B with a full well capacity (FWC) of 200 ke- optimized for high dynamic range applications and a high signal to noise ratio (SNR) was combined with a robust algorithm for line determination.
The laser line detection algorithm is able to compute the peak position of a laser line with sub-pixel accuracy. Thus, the height profile of an object gets computed within the camera, making additional calculations in the PC needless.
3D triangulation rate on different region of interest:
Resolution | Profiles [fps] |
1024 x 1024 | 150 |
1024 x 256 | 590 |
1024 x 128 | 1170 |
1024 x 64 | 2300 |
1024 x 32 | 4400 |
1024 x 20 | 6750 |
512 x 16 | 14770 |
Laser line with LinLog® Technology: | Laser line without LinLog® Technology: |
![]() | ![]() |
Typical triangulation setup:

Features:
- Detection of a laser line (peak detector) with sub-pixel accuracy
- Configurable region of interest (ROI)
- Dynamic range up to 120dB via LinLog®
- Image correction
- Ultra low trigger delay and low trigger jitter
- Extended trigger input and strobe output functionality
- Isolated inputs (2 single ended, 2 differential) and outputs (2 single ended)
- A/B shaft encoder interface (RS-422 (G2 models) or HTL (H2 models))
- Free GUI available (PF 3D Suite) for an easy system set up and visualisation of 3D scans