Elephant Robotics myCobot Pro 630 Alternatives & Competitors
Ranked Nr. 260 of 207 Cobots
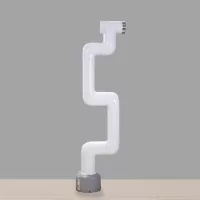
Top 10 myCobot Pro 630 Alternatives
- Elephant Robotics myCobot 280-Pi
- Elephant Robotics myCobot 320 2022-m5
- Elephant Robotics All-In-One Suite
- Elephant Robotics myCobot 280-M5
- Elephant Robotics mechArm 270-M5
- Elephant Robotics mechArm 270-Pi
- Elephant Robotics UltraArm P340
- FANUC CRX-10iA
- RETHINK ROBOTICS BAXTER [permanently unavailable]
- HITBOT Z-Arm 2442
- OMRON TM 5-900

Elephant Robotics myCobot 280-Pi
Payload 0.25kg | Reach 280mmThe myCobot 280-Pi is a compact six-axis collaborative robotic arm that is designed for desktop use. It is powered by a Raspberry Pi computer and is an ideal tool for education, research, and hobbyist projects.
The myCobot 280-Pi features a lightweight and durable aluminum alloy construction, which makes it easy to move and operate. It is equipped with high-precision stepper motors and a built-in controller that provides smooth and accurate movement control.
The robot arm is easy to set up and use, thanks to its intuitive software platform and user-friendly interface. It supports a wide range of programming languages, including Python, C++, and Scratch, which makes it easy for users with varying levels of coding experience to program and control the robot.
The myCobot 280-Pi is also equipped with a range of sensors, including a 3D camera, a force sensor, and a touch sensor, which enable it to interact with its environment and perform various tasks, such as object recognition and pick-and-place operations.

Elephant Robotics myCobot 320 2022-m5
Payload 1kg | Reach 350mmThe myCobot 320 2022-M5, developed by Elephant Robotics, is a six-axis collaborative robot designed to enhance automation and precision in various industries. It features a compact and lightweight design, allowing for flexible deployment in diverse environments such as laboratories, workshops, and small-scale production lines. The robot's modular construction facilitates easy integration with different end-effectors and accessories, enhancing its versatility for tasks like pick-and-place, welding, assembly, and more.
Equipped with advanced sensors and a user-friendly interface, the myCobot 320 ensures safe and intuitive operation alongside human workers. Its advanced motion control algorithms enable high precision and repeatability, making it suitable for intricate tasks requiring fine motor control. The robot’s design supports easy programming through intuitive software, reducing the learning curve for operators and expediting the setup process for various applications.
The myCobot 320 2022-M5 is also notable for its connectivity options, including integration with popular industrial automation platforms and support for various communication protocols. This connectivity enhances its capability to work seamlessly with other robotic systems and automated machinery, contributing to the development of smart manufacturing and Industry 4.0 solutions. Its compact size and robust performance make it an ideal choice for small to medium-sized enterprises looking to implement advanced automation solutions without significant infrastructure changes.

Elephant Robotics All-In-One Suite
The Elephant Robotics myCobot 320 All-In-One Suite is a comprehensive package that includes the myCobot 320 robotic arm and a variety of end-effectors that can be used for different tasks. The myCobot 320 is a six-axis collaborative robotic arm that is designed to be compact and easy to use. It is suitable for a wide range of applications, including manufacturing, research, and education.
The All-In-One Suite includes several different end-effectors that can be used with the myCobot 320 robotic arm, including:
1. Suction Cups: The suction cups can be used to pick up and place small objects, such as electronic components, without damaging them.
2. Adaptive Gripper: The adaptive gripper is a versatile end-effector that can be used to grip and manipulate a wide range of objects, including irregularly shaped objects.
3. Soft Gripper: The soft gripper is designed to handle delicate objects, such as food or biological samples. It has a soft, compliant material that can conform to the shape of the object being gripped.
4. Air Compressor: The air compressor is used to power the air parallel gripper. It provides a source of compressed air that can be used to actuate the gripper.
5. Air Parallel Gripper: The air parallel gripper is a powerful end-effector that can be used to grip and manipulate heavy objects. It uses compressed air to actuate the gripper jaws, which can exert a significant amount of force.
The myCobot 320 robotic arm is designed to be easy to use and program. It can be programmed using a variety of programming languages, including Python and Blockly. It also includes an intuitive graphical user interface that makes it easy to control the arm and its end-effectors.

Elephant Robotics myCobot 280-M5
Payload 0.25kg | Reach 280mmThe Elephant Robotics myCobot 280-M5 is a desktop six-axis collaborative robotic arm that is designed for various applications, including education, research, and light industrial use. It is powered by the M5Stack, an open-source modular prototyping platform that provides a user-friendly and customizable interface for the robot.
One of the key features of the myCobot 280-M5 is its compact and lightweight design, which makes it highly portable and easy to move around in a workspace. The robot arm has a payload capacity of up to 0.25 kg and a maximum reach of 280 mm, making it suitable for a wide range of tasks, including pick-and-place, dispensing, and assembly.
The myCobot 280-M5 is also a collaborative robot, which means it can work safely alongside human operators without the need for safety barriers or cages. The robot has built-in torque sensors that can detect and react to any external force or pressure, ensuring the safety of operators and surrounding personnel.
The M5Stack platform provides a user-friendly interface for programming and controlling the myCobot 280-M5. The platform includes a range of pre-built modules and sensors that can be easily integrated with the robot, as well as a range of programming languages, including Python and Blockly.

Elephant Robotics mechArm 270-M5
Payload 0.25kg | Reach 270mmThe mechArm 270-M5 is a six-axis robotic arm developed by Elephant Robotics, designed specifically for collaborative robot (cobots) applications. It is the most compact six-axis collaborative robotic arm available, powered by M5Stack technology.
The mechArm 270-M5 is designed to work safely alongside humans in collaborative environments. It has a compact and lightweight design, making it easy to install and move. The robot arm has a maximum payload of 0.25 kg and a maximum reach of 270 mm.
One of the key features of the mechArm 270-M5 is its use of M5Stack technology. The M5Stack is a modular and open-source development kit that provides a simple and powerful way to create and prototype IoT and robotic projects. The mechArm 270-M5 is powered by M5Stack, which enables it to be easily programmed and controlled using a range of programming languages, including Python and Arduino.
The mechArm 270-M5 is also equipped with advanced safety features, including torque sensors and collision detection sensors, which enable it to stop or slow down its movements if it detects any obstacles in its path. This makes it safe to work alongside humans without the need for fencing or other safety measures.
The mechArm 270-M5 is ideal for a range of collaborative robot applications, including assembly, pick-and-place tasks, and inspection. Its compact size and advanced technology make it an ideal tool for small and medium-sized businesses looking to automate their processes.

Elephant Robotics mechArm 270-Pi
Payload 0.25kg | Reach 270mmThe MechArm 270-Pi is a six-axis collaborative robotic arm that is designed to be compact and powered by a Raspberry Pi. This robotic arm is a DIY kit that allows users to build their own robotic arm and program it to perform various tasks.
The MechArm 270-Pi is one of the most compact six-axis collaborative robotic arms on the market. It has a reach of 270mm and a payload capacity of 0.25kgs, which makes it ideal for small-scale automation tasks. The arm is designed to be collaborative, which means it can work safely alongside humans without causing any harm.
The robotic arm is powered by a Raspberry Pi, which is a popular single-board computer that can be programmed using a variety of programming languages. The Raspberry Pi provides a user-friendly interface for programming the arm, and it also allows the arm to be integrated with other devices and systems.
The MechArm 270-Pi is a DIY kit, which means that users need to assemble the arm themselves. The kit includes all the necessary components, including the motors, the controller, and the Raspberry Pi. The assembly process is straightforward and can be completed in a few hours.
Once the arm is assembled, users can program it to perform various tasks using Python or other programming languages. The robotic arm can be used for a wide range of applications, such as pick-and-place tasks, machine tending, and quality control.

Elephant Robotics UltraArm P340
Payload 0.65kgThe UltraArm P340 is a 4-axis collaborative robotic arm that is designed to be small and portable. Despite its small size, the arm is equipped with a high-performance stepper motor that allows it to achieve a ±0.1mm repeated positioning accuracy and high stability, making it ideal for precise tasks such as writing, drawing, and laser engraving.
The UltraArm P340 has a classic metal structure and occupies an area of only A5 paper, making it easy to transport and set up in a variety of settings. Additionally, the arm can be freely matched with multiple accessories, such as slide rails, conveyor belts, myAGV, and cameras, allowing it to complete different practical training projects according to specific needs.
The UltraArm P340 is widely used in many fields, including higher education, scientific research, vocational application education, and more. Its versatility, accuracy, and stability make it an ideal tool for a variety of tasks, including pick-and-place, assembly, and material handling. The collaborative capabilities of the arm also ensure the safety of nearby personnel, as it can work alongside human operators without the need for safety barriers or cages.

FANUC CRX-10iA
Payload 10kg | Reach 1249mmFanuc's CRX-10iA is a collaborative robot that is designed to work safely and efficiently alongside human workers. The robot is part of Fanuc's CRX series of collaborative robots, which are designed to provide a range of advanced capabilities and features to enhance manufacturing and other industrial processes.
The CRX-10iA is a compact and lightweight robot, with a payload capacity of up to 10 kilograms. It has a reach of up to 1249 millimeters, and can be mounted on the floor, ceiling, or wall, giving it a great deal of flexibility in terms of placement and orientation.
The robot is equipped with a range of advanced sensing and control technologies, including a built-in vision system that allows it to recognize and respond to its environment. It is also designed to work seamlessly with other robots and industrial equipment, making it a powerful tool for improving efficiency and productivity in a range of industrial settings.
One of the key features of the CRX-10iA is its ease of use and programming. The robot is designed with a user-friendly interface that allows operators to quickly and easily program and control its movements and behavior. It is also designed with safety in mind, with features such as collision detection and force sensing that help to prevent accidents and injuries.

RETHINK ROBOTICS BAXTER [permanently unavailable]
Payload 2.2kg | Reach 1210mmBaxter is a collaborative robot, also known as a cobot, designed and developed by Rethink Robotics. One of the standout features of Baxter is its ability to work safely alongside human operators, without requiring traditional safety barriers or cages. This makes it an ideal option for industrial settings where human-robot collaboration is necessary, such as manufacturing and assembly lines.
One of the most unique aspects of Baxter is its adaptive behavior. Rather than relying on pre-programmed movements, Baxter is able to adapt to changes in its environment and perform a variety of tasks using its advanced sensing and vision capabilities. This makes it incredibly versatile and able to perform a wide range of tasks, from picking and placing objects to performing quality control inspections.
Baxter is also designed with ease of use in mind. Its user-friendly interface and intuitive programming system make it easy for operators to program and teach Baxter new tasks without requiring specialized technical expertise. This means that even operators with limited programming experience can quickly learn to use Baxter and integrate it into their workflow.
Another standout feature of Baxter is its durability and reliability. It is designed to operate in harsh industrial environments and can withstand extreme temperatures and humidity levels. It also has a high payload capacity, allowing it to handle heavy objects and perform tasks that other cobots may not be able to handle.
In terms of specialized specifications, Baxter is compatible with a variety of software systems, including ROS (Robot Operating System) and Python. This makes it easy for users to customize and program Baxter to meet their specific needs and integrate it into their existing systems. Baxter is also designed to be easily upgraded and maintained, ensuring that it remains a valuable tool for industrial automation for years to come.
Overall, Baxter is a highly advanced and versatile cobot that is well-suited for a wide range of industrial automation applications. Its unique features, ease of use, and compatibility with specialized software systems make it a popular choice for manufacturers and other industrial operators looking to improve efficiency, safety, and productivity in their operations.

HITBOT Z-Arm 2442
Payload 3kgThe Hitbot Z-Arm 2442 is a collaborative robotic arm designed for various industrial applications. This lightweight robotic arm weighs only 19kg and has a compact design, making it easy to install and use in confined spaces. The robot has a built-in motion controller, with 24 I/O ports for extensibility and adding one more arm.
The robot has four axes, with a maximum payload of 3kg and a rated payload of 2kg. The robot arm has a reach of 220mm for the J1 axis, 200mm for the J2 axis, and 240mm for the Z-axis. The rotation range for the J1 axis is ±90°, for the J2 axis is ±164°, and for the R-axis (optional) is ±1080°. The maximum average linear velocity of the robot arm is 1255.45mm/s (with a 1.5kg payload) and 1023.79mm/s (with a 2kg payload). The repeatability of the robot arm is ±0.03mm.
The robot arm supports HITBOT grippers such as Z-EFG-8S, Z-EFG-12, Z-EFG-20, Z-EFG-20S, Z-EFG-30, and Z-EFG-50. Additionally, the robot arm has optional accessories such as grippers, a 5th axis, a 485 board, and a 3D printing kit. The robot arm has a customizable Z-axis height ranging from 0.1-1 meter and supports drag-to-teach programming.
The robot arm has a voltage of 220V/110V 50-60Hz DC24V and power of 500W. The robot arm communicates through Ethernet and has a working temperature range of 0-55℃ with RH85 humidity. The robot arm has digital input (isolated) with 9+3 arm extensibility and digital output (isolated) with 9+3 extensibility for one more arm. The robot arm has collision detection technology, making it safe to operate in human-machine collaboration scenarios.
Overall, the Hitbot Z-Arm 2442 is a high-performance and versatile robotic arm that can be used in various industrial applications, including pick-and-place, assembly, and packaging. With its lightweight and compact design, customizable height, and extensibility, it is an excellent choice for industries looking for cost-effective and efficient automation solutions.