Elephant Robotics Pneumatic Gripper Pro without Air Compressor Alternatives & Competitors
Ranked Nr. 7 of 235 Grippers
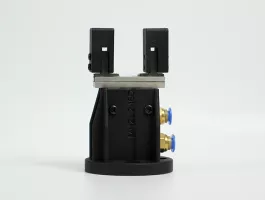
Top 10 Pneumatic Gripper Pro without Air Compressor Alternatives
- Elephant Robotics Pneumatic Gripper Pro with Air Compressor
- Elephant Robotics Electric Parallel Gripper
- Elephant Robotics Adaptive Gripper
- Elephant Robotics Adaptive Gripper Pro
- Onrobot 3FG15 Finger Gripper
- SCHUNK GAP
- AGS Gripper System
- Grip G-GZ125
- Grip G-GZ100
- Grip G-GZ080
- Grip G-GZ063

Elephant Robotics Pneumatic Gripper Pro with Air Compressor
Payload 1kg | Angular | ParallelElephant Robotics' Pneumatic Gripper Pro with Air Compressor is an efficient and reliable solution for industrial automation processes that require precise gripping of objects. Driven by gas and working with a solenoid valve, this gripper is easy to control and offers excellent grip force.
The fingertip of the gripper can be customized and exchanged for users' secondary development, adding flexibility and versatility to its gripping capabilities. The gripper comes with an air compressor, making it a complete and convenient solution for industrial automation processes.

Elephant Robotics Electric Parallel Gripper
Payload 0.1kg | Angular | ParallelElephant Robotics' Electric Parallel Gripper is a versatile and reliable gripping solution that is perfect for a wide range of industrial applications. Its compact structure and multiple connecting holes allow it to meet various installation conditions, while also ensuring a stable and secure grip on objects.
The gripper supports both IO and serial port control, making it easy to integrate with various industrial robotic arms. With its advanced technology and user-friendly interface, the Elephant Robotics Electric Parallel Gripper is an ideal choice for any industry that requires efficient and precise gripping of objects.

Elephant Robotics Adaptive Gripper
Payload 0.15kg | Angular | SoftThe Adaptive Gripper by Elephant Robotics is a versatile robotic end-effector that uses a soft and flexible material to adapt to the shape and size of the object being grasped. It is designed to be applicable to a variety of consumer robotic arms and can be controlled via serial communication.
The gripper is capable of automatically adapting to the width of the clamping object, making it easy to use and eliminating the need for manual adjustments.
The Adaptive Gripper also provides a variety of programming language control interfaces, which allows users to integrate it into their existing automation systems with ease. This makes the Adaptive Gripper suitable for a wide range of applications, such as pick-and-place operations in manufacturing, packaging, and logistics.
The unique and patented design of the Adaptive Gripper allows it to grip objects gently, minimizing the risk of damage or breakage during the handling process.

Elephant Robotics Adaptive Gripper Pro
Payload 1kg | Angular | Parallel领先的先进机器人解决方案提供商 Elephant Robotics 最近推出了其最新产品 Adaptive Gripper Pro。该产品是该公司之前自适应夹持器型号的升级版,具有出色的夹紧力和多功能性,是各种工业自动化应用的理想解决方案。
Adaptive Gripper Pro 最显著的特点之一是其夹紧力增强。这款夹持器的最大夹紧力可达 1000g,能够处理各种物体,从精密部件到较重的物品。夹持器夹紧力增强是由于采用了新的齿轮减速机构,可提供更好的扭矩和夹紧力。
除了增强的夹紧力外,Adaptive Gripper Pro 还支持多种编程环境,使其与各种工业机械臂兼容。这款夹持器可以使用行业标准软件进行编程,包括 ROS、Python 和 C++。这种灵活性使用户能够轻松地将 Adaptive Gripper Pro 集成到现有的自动化系统中,使其成为各种应用的经济高效的解决方案。Adaptive
Gripper Pro 的另一个显著优势是其适应性。夹持器采用模块化设计,允许用户根据特定需求快速轻松地更换不同的夹持模块。这种模块化设计使 Adaptive Gripper Pro 成为需要处理多个不同形状和大小的物体的应用的绝佳选择。

Onrobot 3FG15 Finger Gripper
Payload 10kg | Angular | Parallel | CentricThe OnRobot 3FG15 Finger Gripper stands out as a versatile solution for gripping cylindrical objects, making it particularly well-suited for machine-tending applications like CNC lathe machines. Notably, the gripper's design incorporates automatic centering of workpieces, resulting in swift deployment with a secure and stable grip, while ensuring precise placement. With an impressive payload capacity of up to 15kg, the 3FG15 challenges traditional, larger, and less flexible finger grippers, offering a robust gripping solution for a wide range of industrial tasks.
What sets the OnRobot 3FG15 apart is its capacity to streamline integration with a variety of robot platforms. This compatibility enhances its usability and makes it suitable for diverse automation setups. The gripper's capability to handle substantial loads, its automatic centering feature, and the seamless integration options collectively contribute to its efficiency and effectiveness in various industrial scenarios.
A lesser-known yet significant specification that adds to its uniqueness is the potential for compatibility with specific software systems. The 3FG15's ability to integrate with a range of software platforms enhances its adaptability and simplifies the integration process, making it a valuable asset for industrial automation tasks that require a strong, precise, and adaptable gripping solution.

SCHUNK GAP
Angular | Parallel2-finger angular parallel gripper with gripper finger actuation of up to 90° per jaw.

AGS Gripper System
ParallelAGS Automation's gripper system, also known as PAG impact grippers, are designed for precision picking up of inserts, bushings, rings or screws. These gripper systems come in different sizes, with varying numbers of gripper fingers and stroke sizes, making them suitable for various applications.
One of the notable features of PAG impact grippers is the modular system that allows for optimal adaptation options in both the gripping and attachment directions. This means that these gripper systems can be customized to meet the specific requirements of each application.
The gripper fingers of PAG impact grippers move parallel to each other and are guided by a dovetail guide, ensuring precise and stable gripping of the workpiece. This parallel movement also enables the gripper system to pick up and hold small workpieces securely.
PAG impact grippers are available in both single-acting and double-acting types. The double-acting PAG grippers can be used for both internal and external gripping, while the single-acting PAG grippers are suitable for external gripping.

Grip G-GZ125
AngularThe Angular Gripper with pivoting jaw movement. The double-acting cylinder is actuated by compressed air which actuates the movements. An eccentric mechanism ensures a long service life and a constant gripping torque. In contrast to the Parallel Gripper, the gripping force safety device can only be designed as a closing -GS- version.

Grip G-GZ100
AngularThe Angular Gripper with pivoting jaw movement. The double-acting cylinder is actuated by compressed air which actuates the movements. An eccentric mechanism ensures a long service life and a constant gripping torque. In contrast to the Parallel Gripper, the gripping force safety device can only be designed as a closing -GS- version.

Grip G-GZ080
AngularThe Angular Gripper with pivoting jaw movement. The double-acting cylinder is actuated by compressed air which actuates the movements. An eccentric mechanism ensures a long service life and a constant gripping torque. In contrast to the Parallel Gripper, the gripping force safety device can only be designed as a closing -GS- version.