Specim INSIGHT Alternatives & Competitors
Ranked Nr. 2 of 85 Robot Software
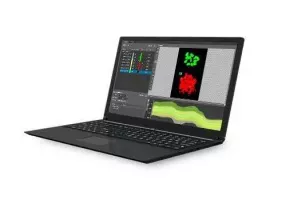
Top 10 INSIGHT Alternatives
- National Instruments LabVIEW
- FANUC ROBOGUIDE
- RoboDK RoboDK
- ABB RobotStudio®
- MathWorks MATLAB
- KUKA KUKA.Sim
- W.A.T. Solutions Workspace
- Tesseract Solutions KMeleon Software
- OCTOPUZ Robot programming and simulation software
- Delfoi PAINT
- Delfoi SPRAY-X

National Instruments LabVIEW
Offline programming | Simulation | Monitoring | Developer tools | VisionNational Instruments LabVIEW is a graphical programming environment used by engineers to develop automated research, validation, and production test systems. Its standout features include thousands of available analysis functions, enabling complex data processing, and configurable, interactive display elements for real-time data visualization. LabVIEW also offers drivers for automating instruments and data acquisition hardware, ensuring seamless integration with various equipment.
A unique aspect of LabVIEW is its compatibility with other programming languages and industry-standard protocols, allowing smooth integration into existing software systems. This makes it an excellent choice for industrial automation setups that require data exchange and collaboration between different platforms. Moreover, LabVIEW's versatility and adaptability make it a preferred option for businesses with diverse automation needs, as it can accommodate various instruments and hardware.
Another lesser-known advantage of LabVIEW is its robustness in handling extreme temperatures and harsh industrial environments. This capability makes it a reliable solution for automation applications in challenging conditions, such as manufacturing processes that involve high temperatures or rugged outdoor environments. Overall, LabVIEW's extensive functionalities, compatibility, and resilience make it a unique and powerful option for engineers seeking to develop sophisticated automated test and control systems.

FANUC ROBOGUIDE
Offline programming | Simulation | Developer tools | Vision | WeldingFANUC ROBOGUIDE is a leading offline programming robot simulation software designed for FANUC robots. It offers process-focused robot simulation packages, enabling users to create, program, and simulate robotic workcells in a 3D virtual environment without the need for physical prototypes. This reduces costs and risks, allowing users to visualize single and multi-robot workcell layouts before actual installation.
ROBOGUIDE comes with various feature-specific modules. Handling Pro is ideal for material handling, packing, assembly, and material removal tasks, supporting line tracking and path programming. Paint Pro simplifies the painting process, allowing users to select paths and areas graphically for automatic program generation. Pallet Pro & Pallet tools enable users to build and test palletizing applications, offering a library of different pallet configurations. Weld Pro specializes in arc welding, featuring capabilities for CADD path programming.
In addition to the key features, ROBOGUIDE offers advanced functionalities like Auto Place, Duty, Cable, Vision, Spray, and COORD (coordination). These features enhance the software's versatility, enabling users to tackle complex and advanced systems efficiently. ROBOGUIDE supports CADD files, has built-in CADD models, and facilitates pre-programming, streamlining the setup and testing of sophisticated automation systems. Its compatibility with various software systems and extensive capabilities make it a unique and powerful option for industrial automation, providing valuable assistance to manufacturers and robotics developers.

RoboDK RoboDK
Offline programming | Simulation | Developer tools | VisionRoboDK is a comprehensive robotic simulation and programming software that offers a user-friendly experience with five easy steps to simulate and program robots. It provides access to an extensive library of over 500 industrial robot arms from various manufacturers like ABB, Fanuc, KUKA, and Universal Robots. Moreover, it supports external axes such as turntables and linear rails, allowing users to model and synchronize additional axes effortlessly.
The software facilitates precise tool definition by loading 3D models of tools and converting them to robot tools by drag-and-drop actions. Users can calibrate robot tools accurately using RoboDK. Additionally, it enables the loading of 3D models of parts and placing them in a reference frame for a quick proof of concept. The simulation capabilities enable users to create robot paths using an intuitive interface, integrating with CAD/CAM software and accessing plug-ins for various design software.
RoboDK's standout feature lies in its ability to generate robot programs offline with just two clicks, supporting over 40 robot manufacturers with more than 70 post-processors. It eliminates the need for programming experience, making it accessible to a broader user base. Furthermore, it automatically generates error-free paths, avoids singularities, axis limits, and collisions, ensuring efficient and collision-free robot programming. The software's capability to split long programs enables easy loading into the robot controller, streamlining the programming process for industrial automation tasks.

ABB RobotStudio®
Offline programming | Simulation | Developer tools | VisionABB's RobotStudio stands out as a powerful simulation and offline programming software, widely regarded as the most used tool of its kind in the world. Its offline programming capability enables programming, training, and optimization of robot systems without disrupting production, ensuring maximum return on investment and minimizing production downtime.
Built on the ABB Virtual Controller, RobotStudio offers realistic simulations using actual robot programs and configuration files from the shop floor. Its feature-rich package includes Virtual Meetings, enabling collaboration through sharing digital robot solutions in web meetings, reducing travel expenses and time. The Digital Twin concept allows real-time simulation of the production system without affecting ongoing production, facilitating changes and optimization in the virtual world.
RobotStudio's Virtual Commissioning replicates the production cell virtually, solving technical issues in advance and speeding up commissioning. The Stop Position Simulation visualizes optimal braking distance with millisecond precision, enhancing SafeMove usage, reducing cell footprint, and streamlining commissioning. Moreover, the Augmented Reality feature overlays modeled solutions as holograms in the real-life production environment, accessible through augmented reality glasses or smart devices. These unique specifications make ABB's RobotStudio an ideal option for industrial automation and offline programming.

MathWorks MATLAB
Simulation | Developer tools | VisionMathWorks MATLAB is a widely-used programming and numeric computing platform utilized by engineers and scientists for data analysis, algorithm development, and model creation. It offers a powerful desktop environment, combining iterative analysis and design processes with a programming language that directly handles matrix and array mathematics. One standout feature is the Live Editor, allowing users to create executable notebooks that seamlessly integrate code, output, and formatted text.
MATLAB boasts professionally developed and thoroughly tested toolboxes, providing a wide range of functionalities for various applications. Interactive apps in MATLAB enable users to visualize algorithms in action with their data, facilitating iteration until desired results are achieved. Additionally, MATLAB's scalability allows for seamless analysis execution on clusters, GPUs, and clouds, with minimal code adjustments. Users can harness the power of these distributed computing resources without the need to rewrite their code or learn complex big data programming techniques.
Moreover, MATLAB's compatibility with various hardware architectures and its ability to scale easily make it an attractive option for industrial automation. Its tolerance for extreme temperatures or specific software systems is not explicitly mentioned in the provided information, but MATLAB's ability to handle distributed computing and its support for GPUs and clusters can be beneficial for industrial applications that require efficient processing of large datasets and complex algorithms.

KUKA KUKA.Sim
Offline programming | Simulation | Developer toolsKUKA.Sim is a smart simulation software designed for efficient offline programming of KUKA robots. It enables users to optimize system and robot operations outside the production environment quickly and easily, leading to increased productivity, safety, and competitiveness. The software brings robot applications to life virtually, allowing real-time depiction and analysis of robot motion sequences. With features like reachability check and collision detection, users can ensure the feasibility of robot programs and work cell layouts, providing maximum planning reliability for manufacturing processes while minimizing costs and effort. KUKA.Sim's user-friendly interface allows for the simulation of a robot system in just a few minutes, even without deep programming knowledge.
The standout features of KUKA.Sim include its ability to offer real-time simulation and optimization of robot motion sequences, helping users identify and resolve potential issues before implementing them in the actual production environment. The software's reachability check and collision detection features add an extra layer of safety and accuracy to the programming process, ensuring that robot programs and work cell layouts are feasible and efficient. By utilizing KUKA.Sim for offline programming, manufacturers can reduce production downtimes, leading to increased productivity and overall competitiveness.
One of the unique aspects of KUKA.Sim is its ease of use and quick setup, allowing users to simulate a robot system in just a few minutes, even with limited programming knowledge. This accessibility makes it an attractive option for users of varying skill levels, enabling them to take advantage of the benefits of offline programming without requiring extensive training. Additionally, the software's compatibility with KUKA robots further streamlines the programming and implementation process, making it a specialized and efficient solution for industrial automation needs.

W.A.T. Solutions Workspace
SimulationIndustrial Grade Simulation Software for Education
Workspace LT™ brings Industrial Grade Robot and Automation Simulation to Educational Institutions. Developed for the Educational market, Workspace LT™ provides an affordable Windows-based solution for teaching the concepts and programming of Robots and other manufacturing automation equipment.
Workspace LT™ offers full offline programming, and the ability to simulate complex workcells with multiple robots and automation devices. While targeted at the educational market, Workspace LT™ is designed to allow you to make maximum use of the resources at your disposal.
Features:
- 3D CADD support
- Robot library (inbuild and custom) (ABB, Fanuc, KAWASAKI, KUKA, Motaman, MATLAB, Nachi, Panasonic, microbot )
- 3D mouse support
- Support robot languages (AS Rapid, Inform II TP, Karel II, Karel III,)
- Accurate simulation & kinematic modeling.
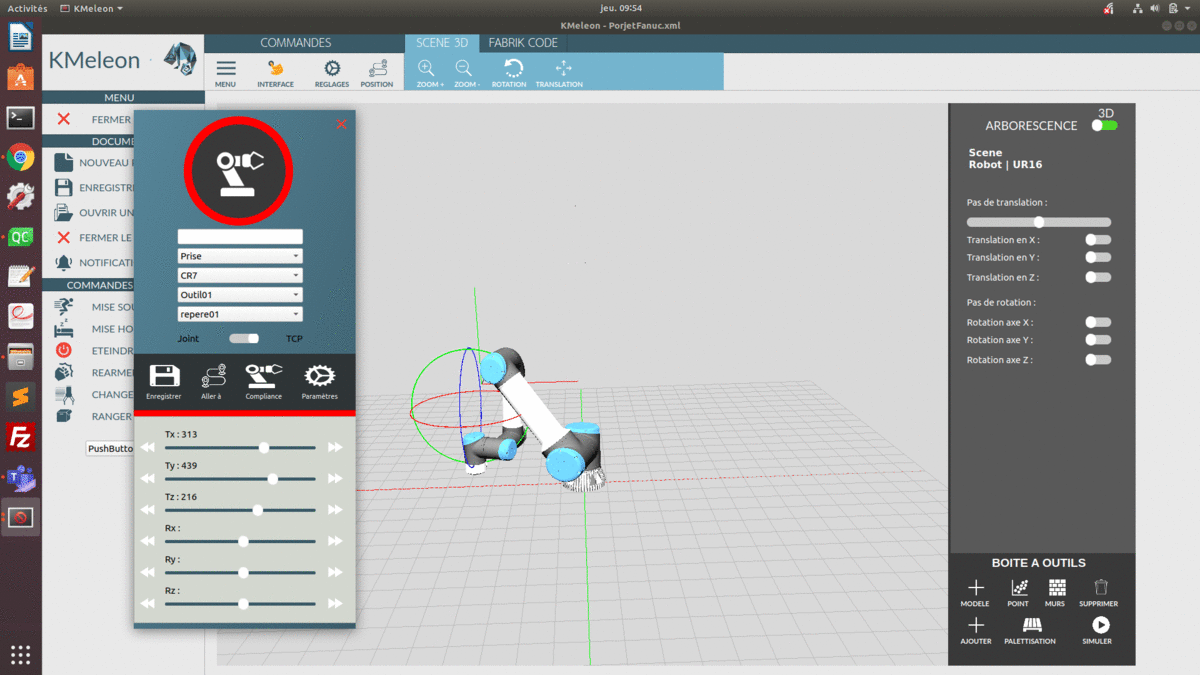
Tesseract Solutions KMeleon Software
Simulation- Set-up all of your line on a single software : robots, tools, controllers, sensors.
- Thanks to the technology FabrikCode, you'll be able to program without typing any line of code. Thanks to this technology based on "Drag & Drop" you'll gain more freedom.
- KMeleon gives you access to a universal language for the robotic programming of the main robot suppliers (Fanuc, ABB, Kuka, UR, Staubli…)
- Try your programs on KMeleon or on a robot, you'll choose ! Thanks to the 3D simulation interface you can simulate the different moves and measure your cycle time in no time.

OCTOPUZ Robot programming and simulation software
Offline programming | SimulationChange the way industrial robots work for you
OCTOPUZ Offline Robot Programming (OLRP) software enables complex robot applications to be programmed in a virtual, offline environment, without disruption to your manufacturing process and without the need for an onsite robot programming expert. OCTOPUZ eliminates the need for your robots to be taken out of production, greatly improving your productivity and bottom line.
Build
Jump right into your next project with a personalized digital twin template of your robot cell.
Quickly setup your project environment using your cell template containing all of your fixed components.
Import your exact CAD part directly into your environment and easily position it exactly where you need it.
Program
Efficiently program your part with integrated tools for creating and optimizing robot motions.
Program multiple robots simultaneously, with support for many different robot brands in unique configurations. Regardless of robot brand, the programming process is identical.
Reduce your programming time with simple, effective tools which put your robot exactly where you need it.
Get your programs ready for production by identifying and solving your robot errors automatically.
Simulate
Validate the accuracy of your welding program through simulation in your digital twin.
Choose how you want see your project in action - by simulating start-to-finish, or by scrubbing to any location in your programs.
Optimize your project by calculating cycle time instantly.
Code
Create accurate robot code ready for immediate production.
Quickly generate your ready-to-run robot code in your robot brand's unique language.
View and update your robot code directly in OCTOPUZ; no need for a separate text editor.

Delfoi PAINT
Offline programmingDelfoi PAINT is a fast, user-friendly offline programming software that is based on set parameters and features and has been developed on the back of more than 20 years of professional expertise. The software is able to effectively utilise the features of the 3D CAD model to be painted and information about the surface topology. It is possible to create programmes quickly and without the need for trial and error, and regardless of the robot brand or model thanks to unique, universal robot code support.
Process features
- Analysis of the paint thickness
- Precise smooth surface paint simulation for the completed painting process
- Optional selection and creation of different colour gradients for the painting simulation/analysis
- Flexible pattern tools to create painting paths based on surface topology
- Automated, unrestricted management of all external robot axes (e.g. gantry positioners, linear tracks and multi-axis paint positioning devices)
- Conveyour tracking for one or multi-robot sytems
- An extensive painting robot library ready for use
- Management of robot painting gun and brush changes
- Easy and fast fine adjustment of all painting paths and the robots via points
- Versatile calibration tools to ensure extreme precision in the programming of modelled cells