TOKYO ROBOTICS TOROBO ARM Alternatives & Competitors
Ranked Nr. 95 of 207 Cobots
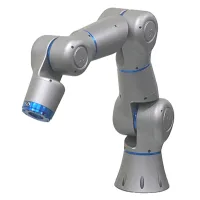
Top 10 TOROBO ARM Alternatives
- YASKAWA HC10DTP Classic
- YASKAWA HC20SDTP
- FRANKA EMIKA Panda
- KUKA LBR IIWA 7 R800
- HANWHA HCR5
- AUBO i10
- FRANKA EMIKA PANDA RESEARCH ROBOT
- Agile Robots Yu 5
- DOOSAN A0509
- Estun Automation S20-180 Pro
- HANWHA HCR3

YASKAWA HC10DTP Classic
Payload 10kg | Reach 1379mmThe YASKAWA HC10DTP Classic is a collaborative robot (cobot) that exemplifies versatility and safety in automation tasks. It has a payload capacity of 10 kg and offers a substantial working reach of 1,379 mm (absolute) and 1,200 mm (effective), making it well-suited for a variety of tasks from assembly to quality inspection. This cobot is engineered for both experienced system integrators and newcomers to robotics, simplifying complex automation challenges with user-friendly interfaces like hand-guiding, a standard teach pendant, and the more intuitive Smart Pendant.
A standout feature of the HC10DTP Classic is its ability to switch between safely monitored slow speeds and full power operations, a hybrid mode that enhances both safety and productivity. This flexibility allows the cobot to perform more dynamic tasks with improved cycle times. Direct Teach buttons on the wrist further streamline programming, allowing users to easily set and modify tasks on the fly. Additionally, integrated safety functions, such as automatic withdrawal from pinch points, underscore its commitment to operator safety.
Applications of the HC10DTP Classic are diverse, reflecting its broad utility in settings that demand both precision and adaptability. It is frequently utilized in scenarios like palletizing, machine tool loading/unloading, and component assembly. The cobot’s design also supports a variety of end-of-arm-tooling options, facilitated by media cables pre-routed within the arm, enhancing its utility without the clutter of external cables. This adaptability makes the HC10DTP Classic a valuable asset across multiple industries, including automotive, electronics, and consumer goods.

YASKAWA HC20SDTP
Payload 20kg | Reach 1412mmThe Yaskawa HC20SDTP is a 6-axis collaborative robot designed for operation in tight spaces. With a payload capacity of 20 kg and a maximum reach of 1412 mm, this model is tailored for applications requiring a shorter reach and high rigidity, such as screw fastening and assembly tasks. Its compact design allows it to fit into confined environments where space is limited, making it suitable for both small and medium-sized manufacturing setups.
The HC20SDTP features an integrated torque sensor in each joint, enabling safe collaborative operation without the need for additional safety fencing. This feature supports its use in environments where human operators and robots work in close proximity. The robot’s robust cast aluminum housing provides durability while maintaining a lightweight structure, ensuring both strength and ease of handling.
Programming and integration are simplified through Yaskawa’s Smart Pendant, which includes configuration wizards for easy setup and Plug&Play functionality for grippers. The robot’s operational flexibility is further enhanced by its multiple mounting options—ceiling, wall, or floor—making it adaptable to various production layouts.

FRANKA EMIKA Panda
Payload 3kg | Reach 800mmThe Franka Emika Panda is a versatile 7-axis robotic arm designed with advanced mechatronics and control capabilities. It stands out for its dexterity and human-centric design, featuring torque sensors on all joints that enable precise and responsive manipulation. With a payload of 3 kg, a reach of 850 mm, and a repeatability of 0.1 mm, the Panda is well-suited for tasks requiring precision and delicacy. Weighing 18 kg, it is lightweight and compact, making it easily deployable in various workspaces, including research labs, educational institutions, and industrial environments.
A key feature of the Panda is its integration of force sensitivity and adaptability, making it ideal for applications that involve close human-robot collaboration. This capability is achieved through its compliance control and collision detection, enabling safe interactions without the need for extensive safety barriers. The robot also supports intuitive programming through tools like Franka Control Interface (FCI) and APIs that cater to users with varying levels of expertise, from beginners to advanced developers.
The Panda is widely used in applications such as assembly, dispensing, remote tool control, and welding, as well as in research areas like robotics and AI. Its open software ecosystem and modular hardware design make it highly customizable for specific tasks. This combination of precision, safety, and flexibility has made the Franka Emika Panda a favored choice for automation solutions that prioritize seamless human-robot collaboration.

KUKA LBR IIWA 7 R800
Payload 7kg | Reach 800mmThe KUKA LBR IIWA 7 R800 is a highly adaptable collaborative robot designed for precision tasks in industrial settings. With a reach of 800 mm and a rated payload capacity of 7 kg, it is suitable for applications that require precise handling and manipulation of parts. The robot offers a high degree of flexibility with its 7 axes and can operate safely alongside human workers, meeting Category 3 and Performance Level d safety standards according to EN ISO 13849-1.
This robot is designed to function within a temperature range of 5°C to 45°C and has an IP54 protection rating, ensuring resistance to dust and splashes of water. It is equipped with the KUKA Sunrise Cabinet for its control system, providing robust and reliable operation. The LBR IIWA 7 R800 also features a pose repeatability of ±0.1 mm, which enhances its accuracy in tasks requiring fine motor control.
The KUKA LBR IIWA 7 R800 is versatile in its mounting options, allowing for floor, ceiling, or wall installation. It operates at varying speeds depending on the axis, with the maximum speed for the A1 axis reaching 98°/s under rated payload conditions. This makes it well-suited for tasks such as assembly, material handling, and quality inspection in dynamic production environments.

HANWHA HCR5
Payload 5kg | Reach 915mmThe Hanwha HCR5 is a versatile 6-axis robot arm designed to meet the demands of various industrial applications. With a payload capacity of 5 kg and a reach of 915 mm, it is capable of handling medium-sized components with precision and efficiency. Its repeatability of 0.1 mm ensures high accuracy in operations, making it suitable for tasks requiring meticulous handling and consistency. Weighing 20 kg, the HCR5 offers a balance of strength and agility, allowing it to be easily integrated into different work environments.
This robot is particularly effective in dispensing applications, where it can precisely apply adhesives, sealants, and other materials, ensuring consistent quality in manufacturing processes. Its ability to accurately control the flow and placement of materials makes it ideal for industries such as electronics and automotive manufacturing, where precision is crucial for product integrity and performance. The HCR5's remote TCP (Tool Center Point) capabilities also enable it to manipulate tools with high precision, enhancing its versatility in handling various tasks.
In welding applications, the Hanwha HCR5 excels in providing stable and accurate welds, contributing to the production of durable and high-quality metal joints. Its compact design and precise movements make it suitable for welding operations in confined spaces or on intricate components. The HCR5's adaptability and precision make it a valuable tool in industries seeking to automate complex processes while maintaining high standards of quality and efficiency.

AUBO i10
Payload 10kg | Reach 1350mmThe AUBO-i10 is a lightweight collaborative robot designed for human-centric agile manufacturing. With a 10 kg payload and 1350 mm reach, it provides flexibility and ease of integration into various industrial environments. Its six axes allow for a wide range of motion, making it suitable for tasks such as machine tending, assembly, and packaging. The robot's compact design and user-friendly features facilitate quick deployment and adaptation without extensive programming knowledge.
A key feature of the AUBO-i10 is its collaborative functionality, allowing it to operate safely alongside human workers without the need for additional safety equipment, provided a risk assessment is completed. Its hand-guiding teaching method and integrated teach pendant simplify programming and operational adjustments. Safety is reinforced through power and force limiting functions that automatically stop the robot if a collision is detected, and real-time feedback is provided by embedded sensors.
The robot supports open-source architecture, including ROS (Robot Operating System) compatibility, and features a CAN bus network for inter-joint communication. This openness, combined with its low cost of ownership and high positional repeatability, makes the AUBO-i10 an appealing choice for both industrial automation and academic research. Its versatility and ease of reconfiguration contribute to its efficiency in high-mix, low-volume applications.

FRANKA EMIKA PANDA RESEARCH ROBOT
Payload 3kg | Reach 855mmThe Franka Research 3 (FR3) is a highly precise and versatile robotic arm designed for advanced research in robotics and AI. It features 7 degrees of freedom (DOF) with torque sensors at each joint, enabling force-sensitive and agile operation. The arm offers a 3 kg payload, an 855 mm reach, and industrial-grade pose repeatability of ±0.1 mm, ensuring minimal path deviation even at high speeds.
FR3 integrates with various ecosystems including ROS, ROS 2, and MATLAB/Simulink, providing robust support for low-level programming and control. Its real-time control capabilities are accessible through the Franka Control Interface (FCI), which operates at 1 kHz for precise torque control and sensor signal measurement. This makes it suitable for experiments requiring detailed control and customization.
Applications of the FR3 include reactive and robust manipulation in dynamic environments, collaborative manipulation with humans, and the development of advanced motion planning and control algorithms. Its adaptability makes it ideal for both academic research and practical implementation in diverse robotic tasks.

Agile Robots Yu 5
Payload 7kg | Reach 1000mmThe Agile Robots Yu 5 Industrial is a high-precision collaborative robot equipped with torque sensors on all six axes, allowing for precise force control and delicate tactile manipulation. It can handle payloads of up to 7 kg with a reach of 850 mm or 5 kg with a 1000 mm reach, making it ideal for intricate tasks in electronics assembly and quality inspection. Additionally, the robot's high repeatability of ±0.05 mm ensures exceptional accuracy, even in applications requiring meticulous handling and placement.
The Yu 5 is designed for seamless human-robot collaboration, adhering to the latest safety standards with features like safely limited drive speed, torque, and position controls. Its intuitive user interface includes a browser-based programming interface, integrated Python API, and hand-guiding capabilities with programmable buttons, facilitating quick setup and easy integration into various industrial settings. This user-centered approach allows operators to adjust the robot for flexible, small-batch production without extensive training.
Applications of the Yu 5 Industrial span across sectors requiring precision and adaptability, such as automotive assembly, where it handles repetitive tasks in constrained spaces, and medical device assembly, where sensitive handling is crucial. The robot’s versatility extends to consumer electronics testing, where its force-sensing capabilities allow it to replicate real-world usage scenarios to verify product durability, further underscoring its role in high-stakes manufacturing environments.

DOOSAN A0509
Payload 5kg | Reach 900mmThe Doosan A0509, part of the A-SERIES collaborative robots, is designed for compact and versatile industrial automation. It supports payloads from 5 to 9 kg, making it suitable for tasks like polishing, assembly, and packaging. The robot's compact design allows it to work effectively in confined spaces while maintaining a high level of productivity.
A key feature of the A0509 is its integrated force-torque sensor. This sensor enables precise force and torque measurement, essential for handling delicate or complex tasks such as detailed assembly and polishing. The sensor enhances the robot’s adaptability and precision in various applications.
The A0509 is also distinguished by its advanced safety algorithms, meeting TÜV SÜD’s stringent safety standards. This allows the robot to work safely alongside human operators without the need for safety barriers. Additionally, its high IP rating ensures durability in harsh environments, and its compatibility with ROS and Doosan’s software streamlines integration into existing systems.

Estun Automation S20-180 Pro
Payload 20kg | Reach 1777.5mmThe Estun S20-180 Pro is a six-degree-of-freedom robotic arm designed for precision motion control in various industrial applications. It features a payload capacity of 20 kg and an arm reach of 1777.5 mm, making it suitable for tasks that require handling medium-weight components. The robot's repeatability of 0.1 mm ensures accurate performance in repetitive operations, enhancing the quality and consistency of production processes.
This robot incorporates multiple security designs, including adjustable collaborative drag mode and collision detection levels, to ensure safe operation alongside human workers. It complies with safety certifications such as EN ISO 13849-1 PLd Cat.3 and EN ISO 10218-1, providing reliable protection during collaborative tasks. Additionally, the S20-180 Pro's flexible installation options allow it to be mounted at any angle, offering versatility in deployment across different industrial settings.
The S20-180 Pro supports a range of applications, from precision assembly to material handling, due to its excellent motion control capabilities and ease of use. With a maximum speed of 3.2 m/s at the tool end and IP54 protection, it is well-suited for environments that require high-speed and reliable performance. Its compatibility with MODBUS RTU and RS485 communication protocols ensures seamless integration with existing automation systems, facilitating efficient and effective operation.