Willow Garage ROS - Robot Operating System Alternatives & Competitors
Ranked Nr. 4 of 85 Robot Software
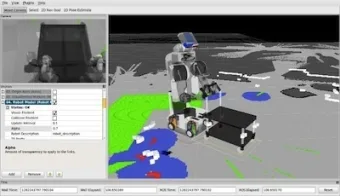
Top 10 ROS - Robot Operating System Alternatives
- Open Robotics GAZEBO
- ABB RobotStudio®
- RoboDK RoboDK
- FANUC ROBOGUIDE
- MathWorks MATLAB
- Coppelia Robotics CoppeliaSim
- KUKA KUKA.Sim
- Cyberbotics Ltd. Webots
- Delfoi SPOT
- Oqton 3D Inspection Software
- MVTec MERLIC

Open Robotics GAZEBO
Simulation | Developer tools | VisionGazebo, developed by Open Robotics, is a collection of open-source software libraries designed to simplify the development of high-performance applications. While its primary audience includes robot developers, designers, and educators, Gazebo is versatile and can be adapted to various use cases. The modular design of Gazebo allows users to choose specific libraries tailored to their application's needs, promoting flexibility and avoiding unnecessary dependencies.
One of Gazebo's standout features is its trust and reliability, ensured through a curation and maintenance process led by Open Robotics in collaboration with a community of developers. Each library within Gazebo serves a specific purpose, reducing code clutter and promoting consistency between libraries. The development and maintenance process adheres to a rigorous protocol, including multiple reviews, code checkers, and continuous integration, ensuring the software's stability and robustness.
Gazebo offers an array of powerful features, making it an excellent option for industrial automation. It includes built-in robot models like PR2 and Pioneer2 DX, enabling users to start simulations quickly. The TCP/IP transport allows simulations to run on remote servers, providing flexibility and scalability. The 3D graphics environment offers advanced and realistic rendering, enhancing the simulation experience. Additionally, Gazebo supports custom plugin development for its API, facilitating integration with other software systems. The dynamic simulation capabilities, along with various sensors and camera modules, make it a comprehensive tool for testing and validating robotic systems in a virtual environment. Furthermore, Gazebo's compatibility with cloud simulations allows users to run simulations on platforms like AWS, leveraging the power of cloud computing for their automation needs.

ABB RobotStudio®
Offline programming | Simulation | Developer tools | VisionABB's RobotStudio stands out as a powerful simulation and offline programming software, widely regarded as the most used tool of its kind in the world. Its offline programming capability enables programming, training, and optimization of robot systems without disrupting production, ensuring maximum return on investment and minimizing production downtime.
Built on the ABB Virtual Controller, RobotStudio offers realistic simulations using actual robot programs and configuration files from the shop floor. Its feature-rich package includes Virtual Meetings, enabling collaboration through sharing digital robot solutions in web meetings, reducing travel expenses and time. The Digital Twin concept allows real-time simulation of the production system without affecting ongoing production, facilitating changes and optimization in the virtual world.
RobotStudio's Virtual Commissioning replicates the production cell virtually, solving technical issues in advance and speeding up commissioning. The Stop Position Simulation visualizes optimal braking distance with millisecond precision, enhancing SafeMove usage, reducing cell footprint, and streamlining commissioning. Moreover, the Augmented Reality feature overlays modeled solutions as holograms in the real-life production environment, accessible through augmented reality glasses or smart devices. These unique specifications make ABB's RobotStudio an ideal option for industrial automation and offline programming.

RoboDK RoboDK
Offline programming | Simulation | Developer tools | VisionRoboDK is a comprehensive robotic simulation and programming software that offers a user-friendly experience with five easy steps to simulate and program robots. It provides access to an extensive library of over 500 industrial robot arms from various manufacturers like ABB, Fanuc, KUKA, and Universal Robots. Moreover, it supports external axes such as turntables and linear rails, allowing users to model and synchronize additional axes effortlessly.
The software facilitates precise tool definition by loading 3D models of tools and converting them to robot tools by drag-and-drop actions. Users can calibrate robot tools accurately using RoboDK. Additionally, it enables the loading of 3D models of parts and placing them in a reference frame for a quick proof of concept. The simulation capabilities enable users to create robot paths using an intuitive interface, integrating with CAD/CAM software and accessing plug-ins for various design software.
RoboDK's standout feature lies in its ability to generate robot programs offline with just two clicks, supporting over 40 robot manufacturers with more than 70 post-processors. It eliminates the need for programming experience, making it accessible to a broader user base. Furthermore, it automatically generates error-free paths, avoids singularities, axis limits, and collisions, ensuring efficient and collision-free robot programming. The software's capability to split long programs enables easy loading into the robot controller, streamlining the programming process for industrial automation tasks.

FANUC ROBOGUIDE
Offline programming | Simulation | Developer tools | Vision | WeldingFANUC ROBOGUIDE is a leading offline programming robot simulation software designed for FANUC robots. It offers process-focused robot simulation packages, enabling users to create, program, and simulate robotic workcells in a 3D virtual environment without the need for physical prototypes. This reduces costs and risks, allowing users to visualize single and multi-robot workcell layouts before actual installation.
ROBOGUIDE comes with various feature-specific modules. Handling Pro is ideal for material handling, packing, assembly, and material removal tasks, supporting line tracking and path programming. Paint Pro simplifies the painting process, allowing users to select paths and areas graphically for automatic program generation. Pallet Pro & Pallet tools enable users to build and test palletizing applications, offering a library of different pallet configurations. Weld Pro specializes in arc welding, featuring capabilities for CADD path programming.
In addition to the key features, ROBOGUIDE offers advanced functionalities like Auto Place, Duty, Cable, Vision, Spray, and COORD (coordination). These features enhance the software's versatility, enabling users to tackle complex and advanced systems efficiently. ROBOGUIDE supports CADD files, has built-in CADD models, and facilitates pre-programming, streamlining the setup and testing of sophisticated automation systems. Its compatibility with various software systems and extensive capabilities make it a unique and powerful option for industrial automation, providing valuable assistance to manufacturers and robotics developers.

MathWorks MATLAB
Simulation | Developer tools | VisionMathWorks MATLAB is a widely-used programming and numeric computing platform utilized by engineers and scientists for data analysis, algorithm development, and model creation. It offers a powerful desktop environment, combining iterative analysis and design processes with a programming language that directly handles matrix and array mathematics. One standout feature is the Live Editor, allowing users to create executable notebooks that seamlessly integrate code, output, and formatted text.
MATLAB boasts professionally developed and thoroughly tested toolboxes, providing a wide range of functionalities for various applications. Interactive apps in MATLAB enable users to visualize algorithms in action with their data, facilitating iteration until desired results are achieved. Additionally, MATLAB's scalability allows for seamless analysis execution on clusters, GPUs, and clouds, with minimal code adjustments. Users can harness the power of these distributed computing resources without the need to rewrite their code or learn complex big data programming techniques.
Moreover, MATLAB's compatibility with various hardware architectures and its ability to scale easily make it an attractive option for industrial automation. Its tolerance for extreme temperatures or specific software systems is not explicitly mentioned in the provided information, but MATLAB's ability to handle distributed computing and its support for GPUs and clusters can be beneficial for industrial applications that require efficient processing of large datasets and complex algorithms.

Coppelia Robotics CoppeliaSim
Simulation | Developer tools | VisionCoppelia Robotics' CoppeliaSim is a leading robotics simulator known for its distributed control architecture, granting individual control over objects through embedded scripts, plugins, ROS nodes, and custom solutions. This unique versatility makes it an ideal choice for multi-robot applications, allowing developers to write controllers in C/C++, Python, Java, Lua, Matlab, or Octave, catering to diverse programming preferences. The simulator finds extensive application in fast algorithm development, factory automation simulations, prototyping, robotics education, remote monitoring, safety validation, digital twin simulations, and more.
CoppeliaSim's standout features include its Remote API, enabling seamless communication with external applications. Its support for multiple physics engines, such as Newton dynamics, vortex studio, and Bullet physics library, ensures accurate and realistic simulations. Additionally, it offers capabilities like inverse and forward kinematics calculations, motion planning with the OMPL library, sensor simulation (including proximity and vision sensors), and importing/exporting videos, images, mesh data, and text in various formats. The platform's data visualization and recording capabilities, collision detection, customizable dynamic particles, and building block concept further enhance its appeal as a comprehensive tool for research, development, and testing in robotics.

KUKA KUKA.Sim
Offline programming | Simulation | Developer toolsKUKA.Sim is a smart simulation software designed for efficient offline programming of KUKA robots. It enables users to optimize system and robot operations outside the production environment quickly and easily, leading to increased productivity, safety, and competitiveness. The software brings robot applications to life virtually, allowing real-time depiction and analysis of robot motion sequences. With features like reachability check and collision detection, users can ensure the feasibility of robot programs and work cell layouts, providing maximum planning reliability for manufacturing processes while minimizing costs and effort. KUKA.Sim's user-friendly interface allows for the simulation of a robot system in just a few minutes, even without deep programming knowledge.
The standout features of KUKA.Sim include its ability to offer real-time simulation and optimization of robot motion sequences, helping users identify and resolve potential issues before implementing them in the actual production environment. The software's reachability check and collision detection features add an extra layer of safety and accuracy to the programming process, ensuring that robot programs and work cell layouts are feasible and efficient. By utilizing KUKA.Sim for offline programming, manufacturers can reduce production downtimes, leading to increased productivity and overall competitiveness.
One of the unique aspects of KUKA.Sim is its ease of use and quick setup, allowing users to simulate a robot system in just a few minutes, even with limited programming knowledge. This accessibility makes it an attractive option for users of varying skill levels, enabling them to take advantage of the benefits of offline programming without requiring extensive training. Additionally, the software's compatibility with KUKA robots further streamlines the programming and implementation process, making it a specialized and efficient solution for industrial automation needs.

Cyberbotics Ltd. Webots
SimulationWebots, developed by Cyberbotics Ltd., is an open-source, multi-platform simulation software tailored for robotics research, development, and education. It provides a comprehensive environment for modeling, programming, and simulating robots, offering tools that support a wide range of robotic systems. The software has been continuously maintained since 1998, ensuring robust functionality and compatibility with emerging technologies.
One of Webots' standout features is its extensive built-in library of pre-designed robots, sensors, and objects, which accelerates the simulation setup process. Additionally, its support for importing CAD models allows users to simulate custom robotic designs with high fidelity. Webots also features a web interface with streaming capabilities, enabling remote interaction and visualization of simulations in real time. Its automatic test suite for code ensures reliability and repeatability, making it suitable for professional and academic use.
Webots is widely used in various fields, including industry, research, and education, due to its flexibility and robust support ecosystem. Common applications include testing algorithms for autonomous navigation, robot design validation, and conducting online simulation challenges. With a large community and resources available, Webots is a key tool for fostering innovation and advancing robotic systems.

Delfoi SPOT
Offline programmingDelfoi SPOT is a fast, user-friendly, parametric and feature based offline programming software. The software can effectively utilise the features of a 3D CAD model. The necessary tools can be created in the software’s internal tool library, where the geometrical information is generated automatically. It is possible to create programs quickly and without the need for trial and error, and regardless of the robot brand.
Process features
- Import spot data from external source
- Manual spot picking
- Easy modification
- Robot synchronization
- IO-signals
- Collision detection; see advanced features
- Automatic path checking
- Management of robot tool changes
- Versatile calibration tools to ensure extreme accuracy for tool paths
Advanced features
- Automatic spot-welding path solver for collision free tool paths
- SPOT Importer – Import spot weld positions from external file: CSV, XML, Custom

Oqton 3D Inspection Software
Monitoring | Calibration | Developer toolsOqton's 3D Inspection Software offers an accessible solution for scan-based 3D inspection, making it easier for engineers and quality assurance managers across different industries to improve their manufacturing processes. By utilizing 3D scanning technologies to capture point-cloud data, the software allows for quick cataloguing and inspection of parts being manufactured, resulting in improved part quality, faster time-to-market, and significant cost savings through reduced scrap and enhanced process sustainability.
The software's unmatched accuracy, flexibility, and speed are its key features, making it an ideal tool for optimizing the quality process of production environments. Its user-friendly interface enables more people to access and use the technology, while its compatibility with different 3D scanning devices allows for greater flexibility in integration with existing systems. Additionally, the software's ability to quickly identify defects and deviations in parts being manufactured helps reduce errors and increases overall quality control.
Oqton's 3D Inspection Software is also designed to lower the barrier to entry for scan-based 3D inspection, making it accessible to more people in more production environments. This means that companies of all sizes can benefit from the technology, and it can be easily integrated into different manufacturing processes. Overall, Oqton's 3D Inspection Software provides an effective solution for improving quality control, reducing waste, and enhancing sustainability in manufacturing operations.