AUTOMATED SCREWING: FASTER, BETTER PRODUCTION
Explore the benefits of automated screwing for faster, more precise production.
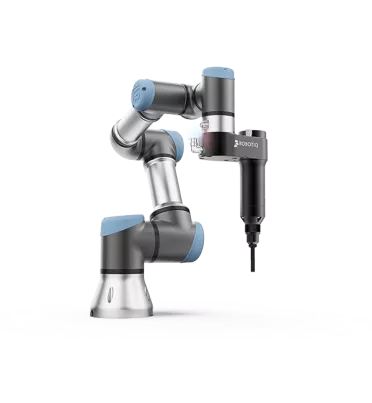
1. What is Screwing?
Screwing in manufacturing is where robots or machines take over the task of putting screws into products. This isn't just about making things faster; it's about precision. Every screw is inserted and tightened just right, every time. Imagine you're building something complex, like a smartphone or a car. Every piece must fit perfectly, and screws hold it all together.
With automated screwing, machines do this work. They use special tools to pick up screws, place them in exactly the right spot, and screw them in with the perfect amount of force. This means products come out looking and working better because there's less chance of mistakes. Plus, it's much quicker than doing it by hand. So, companies can make more products in less time, which is great for meeting high demands. In short, automated screwing makes manufacturing smarter, faster, and more reliable.
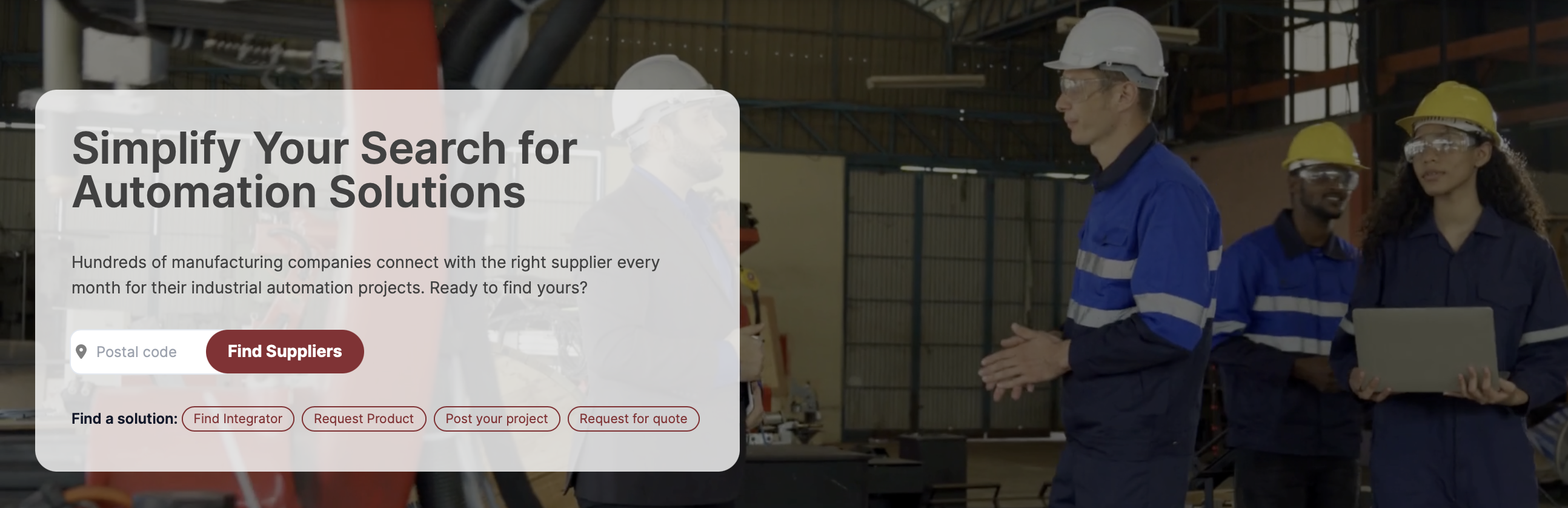
2. Why is Automated Screwing Preferred Over Manual Screwing?
Automated screwing is often chosen over manual screwing for several reasons:
Speed:
Machines can screw parts together much faster than humans. This means products are assembled quicker, letting companies make more in less time.
Consistency:
Robots don’t get tired or distracted. They apply the same amount of force and follow the same path every time, ensuring every screw is perfectly tightened.
Precision:
Automated systems are incredibly accurate. They can place screws precisely where they need to go, reducing the risk of damage to the product.
Cost-Effective:
While setting up automated systems might require an initial investment, they can save money in the long run by lowering labor costs and reducing waste from errors.
Safety:
Using machines for screwing tasks reduces the risk of injuries for workers, as they don't have to perform repetitive, potentially strain-inducing tasks.
3. What Industries Commonly Use Automated Screwing?
Automated screwing makes big tasks easier and products better. Here's where it's commonly used:
Electronics:
Your favorite gadgets, like phones and laptops, are put together with precision. Automated screwing ensures tiny screws are perfectly placed, keeping your devices sleek and functional.
Automotive:
Cars and motorcycles need countless screws for assembly. Automated systems work fast and accurately, making sure every vehicle is sturdy and safe to ride.
Aerospace:
In planes and spacecraft, every screw must be flawless for safety. Automated screwing helps achieve the high level of precision and reliability needed in this critical industry.
Appliance Manufacturing:
From toasters to washing machines, household appliances are assembled more efficiently thanks to automated screwing, ensuring they're ready to make your life easier.
These industries depend on automated screwing for its speed, accuracy, and consistency, helping produce the high-quality products you use every day.
Featured Screwing Cobots:
4. Can Automated Screwing Systems Handle Different Screw Sizes?
Yes, automated screwing systems are quite versatile and can handle different screw sizes. This flexibility is key in industries where products vary in complexity and size.
Adaptable Tools:
These systems come with interchangeable bits and feeders that can adjust to accommodate screws of various sizes and types. It's like having a set of screwdrivers that automatically swap out depending on the job.
Smart Technology:
Many systems are equipped with sensors and software that detect the screw size needed for each part of the product. This ensures the right screw is used every time, much like choosing the correct tool for a task without having to think about it.
Efficiency Across Sizes:
Whether you’re working with tiny screws for electronics or larger ones for automotive parts, these systems ensure each is accurately placed and securely fastened, maintaining high-quality assembly without slowing down production.
Featured Screwing Industrial Robots
5. How Do Automated Screwing Machines Ensure the Correct Torque is Applied?
Automated screwing machines make sure every screw is tightened just right, using something called torque control. Here’s how they do it:
Precision Torque Settings:
These machines have settings that let you choose the exact amount of force, or torque, needed to tighten each screw properly. It's like setting a dial to make sure everything fits snugly without being too loose or too tight.
Feedback Systems:
As screws are tightened, sensors in the machine measure the force being applied. If it's too much or too little, the machine adjusts automatically. This is similar to having a smart wrench that knows when to stop turning.
Consistent Application:
Because they're programmed and automated, these machines apply the same torque every time. This means every screw in every product is consistent, ensuring reliability and quality.
6. Are Automated Screwing Systems Flexible for Different Products?
Yes, automated screwing systems are designed to be flexible and adapt to various products. This adaptability is crucial in industries where product specifications can change often.
Programmable Settings:
These systems can be programmed with different settings for each product. This means they can adjust how they insert and tighten screws based on what's being assembled, ensuring each product is handled correctly.
Interchangeable Tools:
They often come with tools that can be swapped out to match different screw sizes or shapes. It's like having a toolkit that automatically adjusts to whatever you're working on.
Versatile Design:
Many systems have arms or platforms that can move in multiple directions. This allows them to reach different areas of a product, no matter its shape or size, ensuring screws are placed accurately every time.
Featured Screwing 2D Vision Systems:
7. What Types of Screws Can be Used in Automated Screwing Machines?
Automated screwing machines are quite versatile and can work with a wide variety of screw types to fit different manufacturing needs. Here’s a quick rundown:
Machine Screws:
These are used for precise tasks, often in electronics or machinery, where tight tolerances are needed.
Self-tapping Screws:
Great for projects where the screw needs to create its own thread as it's driven into the material, common in wood and plastic assembly.
Self-drilling Screws:
These have a drill bit point to cut through metal, eliminating the need for a pre-drilled hole.
Security Screws:
Designed to prevent tampering, these are used in products requiring a higher level of security.
8. Can Automated Screwing Systems Detect and Correct Errors?
Yes, automated screwing systems are pretty smart! They can both detect and correct errors to ensure everything is assembled just right. Here’s how they do it:
Error Detection:
These systems use sensors and cameras to check if a screw is missing or not properly tightened. It's like having a careful eye that notices if something isn't as it should be.
Automatic Corrections:
If the system finds a problem, it can often fix it on the spot. For example, if a screw isn’t tight enough, the machine can tighten it to the correct level. It's like making a quick fix to ensure everything is perfect.
Alerts for Bigger Issues:
Sometimes, the system might encounter an error it can't fix by itself. In these cases, it sends an alert so a human can step in and solve the problem. This way, you're always in the loop and can keep everything running smoothly
Featured Screwing 3D Vision Systems:
9. How Does Automated Screwing Integrate with Other Production Processes?
Automated screwing systems are designed to seamlessly integrate with other parts of the production line, creating a smooth and efficient workflow. Here’s how they fit into the bigger picture:
Synchronization:
These systems can communicate with other machines, syncing up operations so that each step in the manufacturing process flows into the next without delays. Imagine a relay race where the baton is passed smoothly from one runner to the next.
Quality Control:
They work alongside inspection systems to ensure that each product meets quality standards before moving on. It’s like having a quality checker that makes sure every screw is tight before the product moves to the next stage.
Flexible Programming:
Automated screwing machines can be programmed to adjust to different production runs, making it easy to switch from one product to another without significant downtime. Think of it as changing settings on your phone to match your needs at any moment.
Data Collection:
These systems collect data on their operations, which can be used to optimize the entire production process, helping to identify bottlenecks or areas for improvement.
10. Can Small Businesses Benefit from Automated Screwing?
Yes, small businesses can definitely benefit from automated screwing. Here's how it could be a game changer for you:
Increased Efficiency:
Automated screwing speeds up assembly tasks. This means you can produce more in less time, helping you meet customer orders faster.
Consistent Quality:
Machines are precise. They ensure every screw is placed and tightened correctly, reducing the chance of product defects. This consistency helps maintain your reputation for quality.
Reduced Labor Costs:
Investing in an automated system can save money in the long run. It does the work of several people, allowing you to allocate your team to other tasks that require human insight.
Adaptability:
Modern automated screwing systems are designed to be flexible. They can adjust to different screw sizes and patterns, making them suitable for various products you might be working on.
Need help or have questions? Contact us or book a meeting with Sven, our expert, for personalized support.